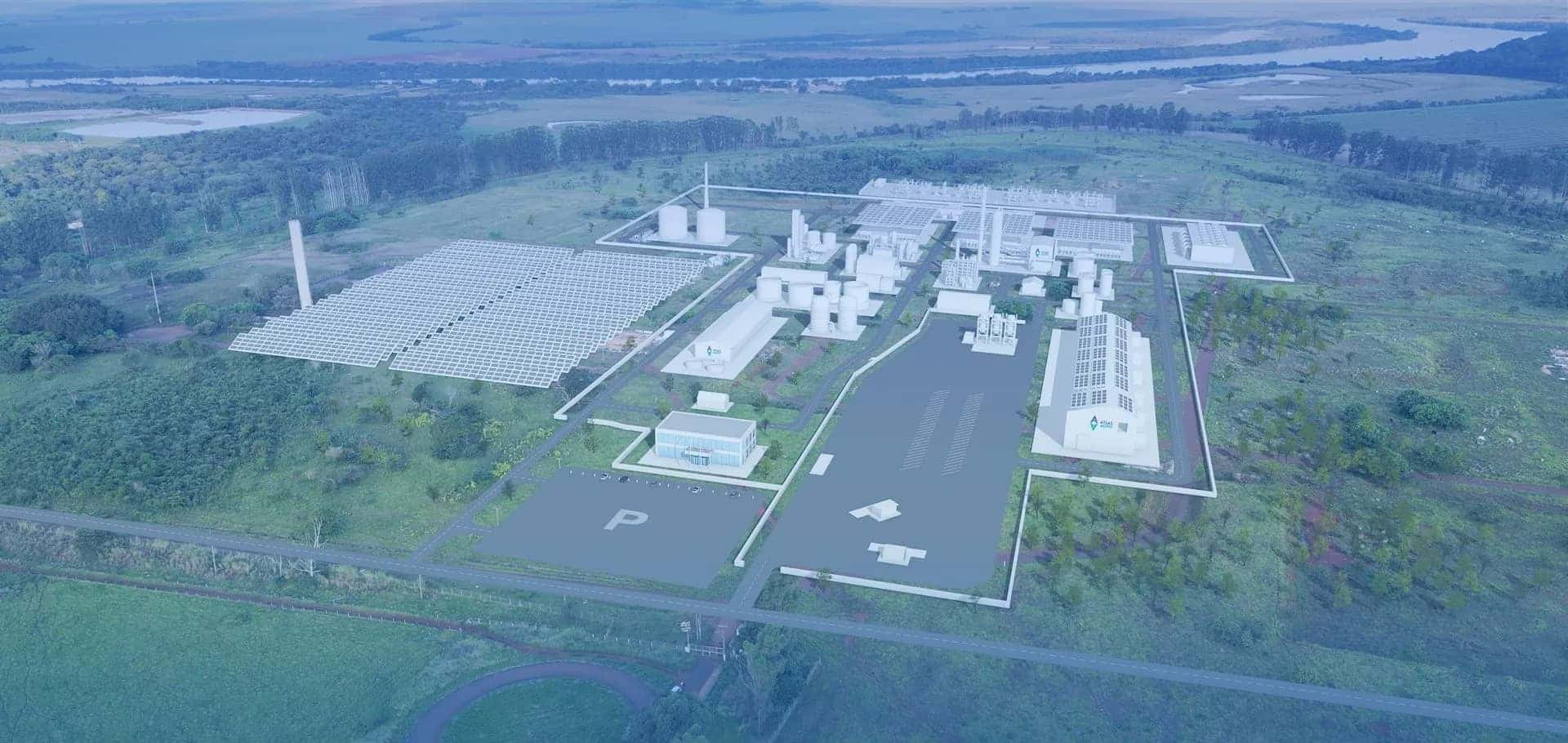
Organic Fertilizer Production Plant In Thailand
installation country
Thailand
Production Capacity
4T/H
Project Investment
$150,000
Product type
Pellets
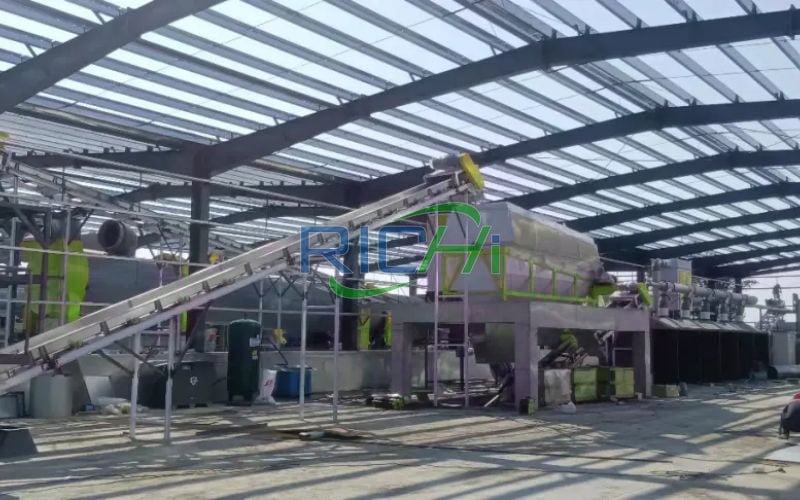
This is an organic fertilizer production plant in thailand project invested by a Thailand fertilizer company. It was built in 2019 and undertaken by RICHI MACHINERY.
In 2024, the customer contacted us again because the customer wanted to transform the coal-fired drying furnace into a gas-fired drying furnace; the coal-fired hot water boiler was changed to a gas-fired hot water boiler; the production workshop added environmental protection equipment such as bag dust collectors and cyclone dust collectors.
The fermentation workshop added odor collection and treatment equipment; eliminated straw, livestock and poultry manure and other raw materials, and used more easily available and lower-cost sugar residues, edible fungus residues, plant ash, etc. as raw materials for production.
This project does not increase the land area and building area, and does not increase production capacity. The production capacity of the whole plant’s bio-organic fertilizer is 10,000 t/a.
After the completion of this technical transformation project, the customer company will add 5 employees, a total of 25 employees after the technical transformation is completed, 300 production days per year, and implement an 8-hour work system in one shift. Employees do not live in the factory area.
RICHI MACHINERY
Construction content
According to customer needs, the construction content of this organic fertilizer production plant in thailand project is as follows:
Engineering classification | Engineering name | Main construction content and scale | |
Existing Engineerings | Technical transformation Engineerings | ||
Main engineering | Fermentation workshop | Located in the middle of the plant, with a construction area of 1,600m2, used for fermentation | The fermentation workshop adds gas collection hoods, photocatalytic devices and other devices to collect and treat odor |
North workshop | Located in the north and east of the plant, 1 , with a construction area of 1,400m2. Used for mixing, granulation, metering and packaging | The North Workshop is equipped with cyclone dust collectors and bag dust collectors to treat production process dust | |
The West Workshop | is located on the west side of the factory, with 1 building area of 1,000m2. Used for drying, mixing, granulation, etc., coal-fired drying furnace and coal-fired hot water boiler are both located in this workshop | In the west workshop, the coal-fired drying furnace is converted into a gas-fired drying furnace, and the coal-fired hot water boiler is converted into a gas-fired hot water boiler, and a low-nitrogen burner is installed to reduce nitrogen oxide emissions, and a bag dust collector is installed to treat production process dust and drying and cooling dust | |
Storage and transportation engineering | 1 raw material warehouse | , located in the north of the factory, for raw material storage, with a construction area of 2400m2 | / |
1 finished product warehouse | , located in the north of the factory, for product storage, with a construction area of 1400m2 | / | |
3 warehouses | , located in the west and southeast of the factory, for product storage, etc., with a construction area of 1200m2. | / | |
Storage building | 1 building, 2 floors, building area 740m2. Located in the middle and east of the factory, used for raw material storage | / | |
Auxiliary engineering | Office | 1 building, located in the middle and east of the factory, building area 300m2. | / |
Communication room | 1 building, located in the south of the factory, building area 20m2. | / | |
Canteen | 1 building, located in the southwest of the factory, building area 350m2. | Add grease trap and oil fume purification device, grease trap has been built, oil fume purification device to be built | |
Bathroom | 1, located in the southwest of the factory, with a construction area of 50m2. | Hot water is provided by the gas hot water boiler in the west workshop | |
Distribution room | 1, located in the northeast of the factory, with a construction area of 20m2 | / | |
Maintenance workshop | 1, located in the northeast of the factory, with a construction area of 40m2 | / |
RICHI MACHINERY
Main technical and economic indicators
The main technical and economic indicators of the organic fertilizer production plant in thailand project include the following:
No. | Item | QTY | Remarks |
1 | Total land area | 23333.3m2 | No additional land area will be added to this project |
2 | Building area | 10520m2 | No additional building area will be added to this project |
3 | Annual production capacity | 10,000 tons | No additional production capacity |
4 | Number of working days per year | 300d | No additional production time |
5 | Number of production hours per year | 2400h | No additional production time |
6 | Number of employees | 25 | 5 additional employees |
RICHI MACHINERY
List of main equipment
The main fertilizer manufacturing equipment of this organic fertilizer production plant in thailand project is shown in the table below.
No. | Existing Project | ||||
Equipment Name | QTY | Equipment Name | QTY | Usage Process | |
1 | Disc fertilizer Granulator | 1 | Low Nitrogen Burner | 2 | Gas Drying Furnace |
2 | fertilizer mixing machine | 4 | Pulse Bag Dust Collector | 6 | Treatment of production process dust |
3 | Rotary screening machine | 3 | High-efficiency cyclone separator | 2 | Treatment of drying dust and feeding dust |
4 | Ring die organic fertilizer granulator machine | 4 | UV photolysis | 1 | Treatment of fermentation waste gas |
5 | Vibrating screening machine | 3 | Draught fan | 15 | / |
6 | Drum fertilizer granulator | 1 | Gas drying furnace | 2 | Drying |
7 | Drying drum | 1 | Oil fume purifier | 1 | Treatment of canteen oil fume waste gas |
8 | Cooling drum | 1 | Gas hot water boiler | 1 | Provide heat for bathroom |
9 | Automatic metering packaging machine | 4 | |||
10 | Bag sewing machine | 4 | |||
11 | Steam generator | 2 | |||
12 | Air compressor | 5 | |||
13 | fertilizer crusher machine | 2 | |||
14 | Secondary Screener | 1 | |||
15 | Heat Sealing Machine | 3 | |||
16 | Conveyor Belt | 10 | |||
17 | Coal-fired drying furnace | 2 | |||
18 | Coal-fired hot water boiler | 1 |
Note: Coal-fired drying furnace and gas-fired drying furnace are non-standard equipment made of refractory bricks.
RICHI MACHINERY
Main raw material consumption
For customers, since raw materials such as sugar residue, edible fungus residue and wood ash are more easily available, and after calculation by the customer company, the investment cost is lower.
Therefore, after the completion of the organic fertilizer production plant in thailand project, customers will eliminate raw materials such as straw and livestock and poultry manure and use raw materials such as sugar residue, edible fungus residue and wood ash instead. In addition, the use of these new raw materials for organic fertilizer production has little impact on the environment.
The technical transformation project will generate an additional annual electricity consumption of 30,000 kWh, which will be supplied by the local power supply station.
No. | Name | Annual consumption | Remarks |
1 | Sugar residue | 7,500t | Water content 40%~50% |
2 | Edible fungus residue | 3,000t | Water content 60%~70% |
3 | Wood ash | 2,500t | Water content 20%~30% |
4 | Natural gas | 253,000m3 | / |
RICHI MACHINERY
General layout
The organic fertilizer production plant in thailand project mainly transforms the original coal-fired drying furnace into a gas-fired drying furnace; the coal-fired boiler is changed to a gas-fired hot water boiler, located in the west workshop; environmental protection equipment is added nearby to the pollution-producing link: an odor collection and treatment device is added above the fermentation pile in the fermentation workshop, and dust collection and dust removal equipment is added to the dust-producing point in the production workshop; the canteen adds a grease trap and oil fume purification device.
The layout satisfies the smoothness of the process flow, reflects the convenience of waste gas collection and transportation, and is convenient for treatment; after taking effective treatment measures, the production waste gas and equipment operation noise have little impact on the office and living area; the general layout is basically reasonable.
RICHI MACHINERY
thailand project organic fertilizer manufacturing process flow
After the technical transformation is completed, the process flow of the organic fertilizer production plant in thailand project is as follows:
Production process flow of the north workshop:
- Mixing: Use a mixer to mix sugar residue and edible fungus residue in the fermentation workshop.
- Fermentation: The fermentation workshop is an independent workshop with a concrete anti-seepage structure on the ground. The fermentation is room temperature fermentation. The fermentation is open-type fermentation, which is turned once a day by the fertilizer mixer machine. This project adopts the form of secondary fermentation, the first fermentation time is 20-30 days, and the second is 10 days. The odor is treated by UV photocatalysis to produce waste lamps.
- Mixing: The fermented materials are transported to the north workshop and mixed with a fertilizer mixing machine and plant ash.
- Screening: The stirred materials are transported to the vibrating screen by the conveyor belt for screening, and the large particles are returned for fermentation. The particles that meet the requirements are sent to the granulator by the conveyor belt for granulation.
- Granulation: Granulation is carried out using a ring die organic fertilizer granules making machine. The fertilizer pelletizer machine uses the rotation of the ring die roller to generate extrusion force between the material particles to form organic fertilizer pellets.
- Screening: The above products are screened using a flat screen, and the small particles are returned to the fertilizer pellet making machine for re-granulation. The particles that meet the requirements (particle size 3-5mm) are inspected.
- Inspection, measurement, packaging and storage: The organic matter of the biofertilizer is inspected, and the qualified ones are measured by a fertilizer bagging machine, packaged and stored, and the unqualified products are returned for fermentation.
Production process of the west workshop:
- Mixing: In the fermentation workshop, sugar residue and edible fungus residue are mixed by a mixer.
- Fermentation: The fermentation workshop is an independent workshop with a concrete anti-seepage structure on the ground. Fermentation is performed at room temperature. The fermentation is open and the mixer is turned once a day. This project adopts a secondary fermentation form. The first fermentation time is 20-30 days and the second is 10 days. The odor is treated by UV photocatalysis to produce waste lamps.
- Mixing: The fermented materials are transported to the west workshop by a fertilizer blending machine and mixed with plant ash.
- Screening: The stirred materials are transported to the vibrating screen by a conveyor belt for screening. The large particles are returned for fermentation. The particles that meet the requirements are transported to the granulator by a conveyor belt for granulation.
- Granulation: The ring die new type organic fertilizer granulator and the disc granulator are used for granulation in succession. Under the action of centrifugal force, friction and gravity, combined with the cohesiveness and plasticity of the material itself, the ball cores are bonded to each other and gradually formed during the movement.
- Drying: The materials are transported to the dryer by conveyor belt. The heat source for drying comes from the drying furnace, which uses natural gas as fuel. The hot air directly contacts the organic fertilizer, and the biofertilizer is dried under the action of the heat.
- Screening: The dried biofertilizer is screened by a vibrating screen, and the small particles are returned to the organic fertilizer granule machine. The particles that meet the requirements (particle size of about 3mm) are inspected and packaged after cooling.
- Inspection, measurement, packaging and storage: The organic matter of the biofertilizer is inspected, and the qualified ones are measured by an automatic metering machine, packaged and stored, and the unqualified products are returned for fermentation. The gas hot water boiler is set on the south side of the west workshop to provide hot water for the bathroom, and a low-nitrogen burner has been configured.
RICHI MACHINERY
What is the prospect of building an organic fertilizer production plant in thailand?
The prospect of building an organic fertilizer plant project in Thailand is relatively optimistic. The following is an analysis of several key factors:
Favorable factors:
- Policy support: The Thai government actively promotes organic agriculture, encourages the use and production of organic fertilizers through subsidies, tax cuts and other policies, and provides a good policy environment for the industry.
- Market demand growth: As consumers pay more attention to food safety and environmental protection, the demand for organic agricultural products continues to rise, which in turn drives the demand for organic fertilizers.
- Enhanced environmental awareness: Thai society pays more and more attention to environmental protection. Organic fertilizers, as environmentally friendly products that reduce the use of chemical fertilizers and improve soil health, have received more attention.
- Agricultural foundation: Thailand has developed agriculture and a large demand for chemical fertilizers. Organic fertilizers have a broad market space as a substitute.
- Rich raw materials: Thailand has developed animal husbandry and agriculture, and the raw materials needed for organic fertilizer production (such as livestock and poultry manure and crop waste) are in sufficient supply.
- Geographical advantage: Thailand is located in the center of Southeast Asia, which is convenient for export to neighboring countries.
Challenges for starting organic fertilizer production plant in thailand:
- Market competition: The organic fertilizer market is highly competitive, and new entrants need to face competition from existing companies.
- Technical limitations: Some companies have backward production technology, which may affect product quality and market competitiveness.
- Consumer awareness: Some farmers lack awareness of organic fertilizers, which may affect their acceptance and market promotion.
If you are interested in building an organic fertilizer production plant in thailand project, feel free to contact RICHI Machinery for technical support on organic fertilizer processing plant design, equipment configuration, production line layout, civil engineering solutions, etc.!