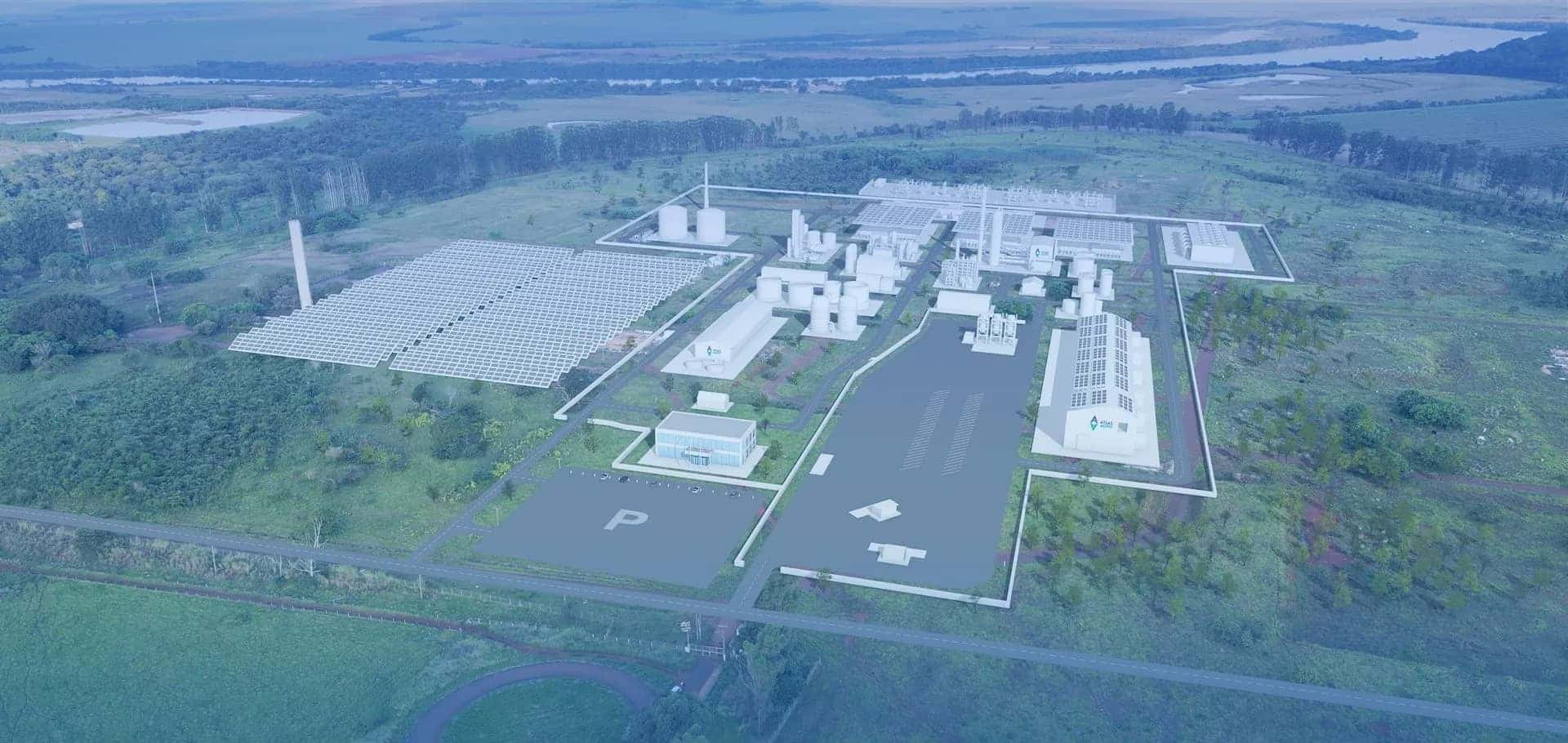
Organic Fertilizer Production Line In USA
installation country
USA
Production Capacity
10-12T/H
Project Investment
$530,000
Product type
Powder/Pellet
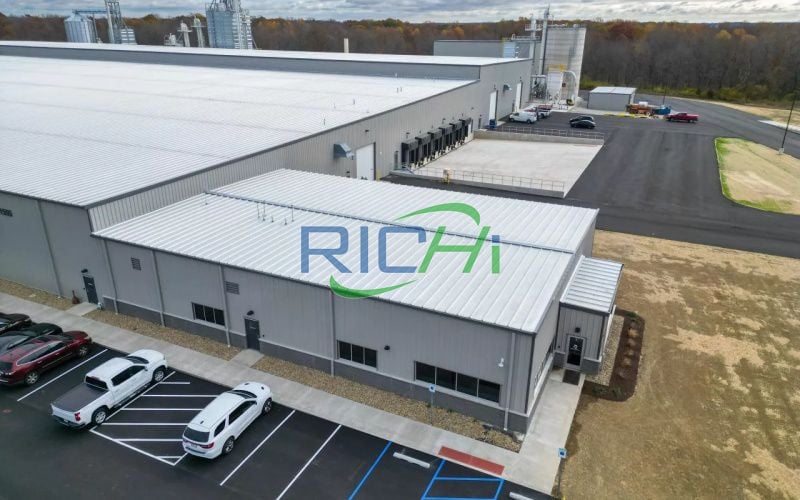
This is a large-scale organic fertilizer production line in United States project and the 8th livestock and poultry manure fertilizer project we have built in the United States. The project mainly uses pig manure, chicken manure and cow manure as the main raw materials.
With the rapid development of large-scale breeding industry, on the one hand, it provides a large amount of meat food for the society, and on the other hand, the manure and waste generated in the production process have become a serious source of environmental pollution. At present, most farms implement dry manure cleaning technology, and the treatment of manure and wastewater mostly adopts traditional methods such as biogas tanks, septic tank fermentation, and precipitation, which has a great impact on the atmosphere and water environment.
The prevention and control of livestock and poultry manure pollution is a systematic project. It is necessary to adhere to the scientific governance principle of prevention first and recycling, and shift agricultural production from conventional methods to green and organic methods to fundamentally solve the serious pollution problem of livestock and poultry manure.
In this context, the client of the project, an agricultural company, invested 530,000 US dollars to build a bio-organic fertilizer production line project to solve the problem of livestock and poultry manure in the area.
By using the production principle of microbial fermentation agents, it developed bio-organic fertilizer, digested harmful elements in livestock and poultry manure, eliminated the pollution of local waters by livestock and poultry, and solved the serious pollution problem of most livestock and poultry manure in the area. The labor quota of the organic fertilizer production plant in United States project is 18 people, working 280 days a year, working 16 hours a day, and no production at night.
RICHI MACHINERY
Construction scale and content
The construction content of this organic fertilizer production line in United States project is shown in the table below.
No. | Indicator Name | Content | Remarks |
Main engineering | Fermentation workshop 1 | 1F, building area of 120m2 | Newly built, reinforced structure factory |
Fermentation workshop 2 | 1F, building area of 412m2 | Newly built, reinforced structure factory | |
Powder stacking workshop | 1F, building area of 210m2 | Newly built, reinforced structure factory | |
Pelletizing workshop | 1F, building area of 180m2 | Newly built, reinforced structure factory | |
Finished product packaging warehouse | 1F, building area of 180m2 | Newly built, reinforced structure factory | |
Storage and transportation engineering | Cow dung accumulation area | 1F, building area of 212m2 | Newly built, reinforced structure factory |
Chicken dung accumulation area | 1F, building area of 92m2 | Newly built, reinforced structure factory | |
Sludge accumulation area | 1F, building area of 60m2 | Newly built, reinforced structure factory | |
Semi-finished product spare warehouse | 1F, building area of 450m2 | Newly built, reinforced steel structure factory | |
Finished product spare warehouse | 1F, building area of 120m2 | Newly built, reinforced steel structure factory | |
Auxiliary engineering | Office and living area | 1F, building area of 280m2, with toilet, production office, guard room, business room, office, finance room, restaurant, kitchen | Newly built, brick-concrete structure |
RICHI MACHINERY
Main product plan
The main products of this organic fertilizer production line in United States project are shown in the table below.
Product Name | QTY | Remarks |
Organic Fertilizer | 10,000 tons/a | Granular, bagged (25kg/bag) |
40,000 tons/a | Powder. Bagged (25kg/bag) |
The product quality standards of this project comply with the U.S. organic fertilizer industry standards. The relevant technical indicators are shown in the table below.
Item | Indicator |
Organic matter mass fraction (on a drying basis)% | ≥45 |
Total nutrients (N+P2O5+K2O) mass fraction (on a drying basis)% | ≥5.0 |
Water (H2O) mass fraction/% | ≤30 |
Acidity (pH) | 5.5~8.5 |
Total arsenic (As) (on a dry basis) mg/kg | ≤15 |
Total mercury (Hg) (on a dry basis) mg/kg | ≤2 |
Total lead (Pb) (on a dry basis) mg/kg | ≤50 |
Total cadmium (Cd) (on a dry basis) mg/kg | ≤3 |
Total chromium (Cr) (on a dry basis) mg/kg | ≤150 |
RICHI MACHINERY
Main raw and auxiliary materials
The consumption of main raw and auxiliary materials for this organic fertilizer production line in United States project is detailed in the table below.
No. | Name | Annual Usage | Remarks |
1 | Pig manure, cow manure, chicken manure and other poultry manure | 40000t/d, 8000t/a | Purchased from outside |
2 | Rice husk, straw and other auxiliary materials | 2000t/a | Purchased from outside |
3 | Fermentation strains | 6.7t/a | Purchased from outside |
4 | Packaging bags | 1.5 million/a | Purchased from outside |
5 | Biomass pellets | 300t/a | Purchased from outside |
RICHI MACHINERY
Process design
Construction period:
The construction period of this organic fertilizer production line in United States project mainly includes site leveling, plant construction, interception and drainage ditches and environmental protection facilities. The specific process is site leveling, plant construction, decoration construction, road and greening construction before delivery.
Operation period:
This project uses closed tank trucks purchased by the customer company to transport the manure produced by the farm, and enters the production of organic fertilizer after entering the factory. The production process is as follows:
(1) Mixing of raw and auxiliary materials
Use poultry manure such as pig manure, cow manure, chicken manure and other poultry manure raw materials, crush the auxiliary materials, add them to the mixing device, and stir them evenly according to a certain raw material component ratio, add organic material strains, add 1 kg of organic fertilizer agent per ton of raw materials, mix them thoroughly, and pre-ferment.
(2) Fermentation:
The materials such as livestock and poultry manure, straw powder and fermentation bacteria are stirred and fully mixed, and then added to the fermentation tank by a forklift for fermentation. Aerobic high-temperature fermentation is adopted, and the fermentation temperature is controlled at 60-70℃. The oxygen content in the fermentation pile is maintained between 5~15%. The compost temperature rises to above 60 degrees. After 48 hours, the compost is turned.
However, when the temperature exceeds 70 degrees, the compost must be turned immediately. When turning the compost, it is necessary to turn the lower layer materials into the upper part of the pile evenly and thoroughly as much as possible to fully decompose. The number of turnings depends on the degree of decomposition of the materials.
The designed fermentation time is about 7 days. The odor generated during the fermentation process is collected and treated by the biological filter deodorization system, and then discharged to the air through a 15-meter-high exhaust pipe.
(3) Crushing
The fermented clinker is crushed and stirred, and the particle size is controlled at 70-80 mesh. A part of it is directly packaged to produce powdered organic solid fertilizer, which is packaged and stored.
(4) Granulation:
Use an organic fertilizer granulator machine to granulate. If the moisture is insufficient, water needs to be added.
(5) Drying and cooling:
This process consists of a drum manure dryer equipment, a drum cooler, a hot air furnace, a dust collector, a fan, etc. The design adopts a drying process of downstream drying and countercurrent cooling.
The wet granular material conveyed by the belt from the granulator enters the inclined drying cylinder through the middle bin at the front of the dryer. At the same time, the hot air sent by the hot air furnace enters the drying cylinder in a downstream manner.
Driven by the shoveling plate in the rotating cylinder, the material is shoveled to form a dense material curtain that is evenly distributed, which increases the contact between the material and the hot air, increases the heat transfer coefficient, and avoids short-circuiting of the hot air flow.
The wet and dusty exhaust gas that completes the heat exchange at the discharge port is introduced into the cyclone dust collector by the centrifugal fan for dust removal and then discharged outdoors. The material is discharged and enters the next process, thereby completing the drying operation of the material.
(6) Measuring and packaging:
Since the granules produced by the granulator are not very uniform, they will also be broken after drying, cooling, conveying, and lifting. In order to ensure that the final product pellets are consistent and convenient to use, the products must be graded and packaged. This process consists of a drum grading screen, a metering and packaging system, a belt conveyor, an elevator, a finished product warehouse, etc.
RICHI MACHINERY
List of main organic fertilizer manufacturing machines
The main organic manure fertilizer making machines used in this project are shown in the table below.
No. | Equipment Name | QTY |
1 | Manure Compost Turner | 1 |
2 | fertilizer feeding machine | 1 |
3 | Fertilizer Crusher machine | 2 |
4 | Fertilizer drum screen | 3 |
5 | Batching machine | 1 |
6 | organic fertilizer mixer machine | 1 |
7 | Buffer silo | 1 |
8 | Fertilizer packaging scale | 2 |
9 | organic fertilizer granulator machine | 2 |
10 | Hot air furnace | 1 |
11 | Fertilizer drying machine | 2 |
12 | Induced draft fan | 1 |
13 | Cyclone dust collector | 3 |
14 | High-level palletizer | 1 |
15 | cow chicken manure conveyor belt | 16 |
RICHI MACHINERY
General layout
The project site is rectangular, with flood diversion ditches around the workshops. Each production workshop is independently set up. The north side of the plant is the raw material yard and fermentation workshop, and the south side of the project is the crushing, screening, drying and granulation workshop.
The USA fertilizer plant project layout basically ensures the smooth and compact process flow, while saving the plant area to the maximum extent, reducing the material transportation process, and the plant area has a high degree of greening. Therefore, the plant layout is reasonable.
RICHI MACHINERY
What is the prospect of building an organic fertilizer production line in the United States?
There is a very good prospect for building an organic fertilizer production line in United States. The main reasons include the large-scale development of American agriculture, the rapid growth of organic agriculture, the promotion of environmental protection policies, and the increasing demand of consumers for sustainable agricultural products. The following is a detailed analysis of this prospect:
- American agricultural background
The United States is one of the world’s largest agricultural producers. It has a large agricultural scale, a high degree of mechanization, and developed animal husbandry and planting industries, which produce a large amount of agricultural waste (such as livestock and poultry manure, crop residues).
American agriculture is moving towards a sustainable direction. Reducing the use of chemical fertilizers and improving soil health are important trends at present.
Organic fertilizers can replace some chemical fertilizers, help improve soil structure and increase soil fertility, and meet the needs of sustainable agriculture.
- Market demand
- Growth of organic agriculture: The United States is the world’s largest organic food market. The area of organic agriculture is increasing year by year, and the demand for organic fertilizers continues to grow.
- Consumer preference: American consumers have a high acceptance of organic food, which has promoted the development of organic agriculture and in turn driven the demand for organic fertilizers.
- Increased environmental awareness: More and more farmers and consumers are concerned about environmental protection and tend to use environmentally friendly agricultural inputs, such as organic fertilizers.
- Policy support
- Farm Bill: The U.S. Farm Bill provides financial support for organic and sustainable agriculture, including subsidies for organic fertilizer production.
- Environmental Protection Agency (EPA) policy: EPA has strict regulations on the management of agricultural waste and encourages the conversion of waste such as livestock and poultry manure into organic fertilizer.
- State-level policy: Many state governments provide additional financial support or tax incentives for organic agriculture and environmental protection projects.
- Emission reduction targets: The U.S. government is committed to reducing greenhouse gas emissions. Organic fertilizer production can reduce greenhouse gases such as methane produced during the decomposition of organic waste.
- Technology and production feasibility
- Mature organic fertilizer production technology: The United States is a world leader in agricultural technology and environmental protection technology, and its organic fertilizer production technology is very mature.
- Large-scale production: The United States has a large agricultural scale, which is suitable for the construction of large-scale organic fertilizer production lines to achieve scale benefits.
- Utilization of byproducts: Byproducts (such as biogas) generated during the production of organic fertilizers can be further utilized to improve economic benefits.
- Competition and Challenges
- Market competition: Although the organic fertilizer market in the United States has grown rapidly, some local and international companies have entered the market, and competition may intensify.
- Initial investment cost: The construction of an organic fertilizer production line requires a certain amount of capital investment, including equipment procurement, technology introduction, and factory construction.
- Stability of raw material supply: The stable operation of the production line depends on the continuous supply of agricultural waste, and it is necessary to establish long-term cooperative relationships with farms, food processing companies, etc.
- Strict environmental protection requirements: The United States has high environmental protection requirements, and the production line needs to comply with relevant emission standards and waste treatment regulations.
- Economic benefits
- Cost and benefits: Agricultural waste has a low cost as a raw material, while the selling price of organic fertilizer is high, especially in areas where organic agriculture is developed, with a large profit margin.
- Stable market demand: With the promotion of organic agriculture, the market demand for organic fertilizer will continue to grow.
- Export potential: American organic fertilizer can not only meet local demand, but also be exported to other countries and regions.
- Development Suggestions
- Market Research: Before investing, it is necessary to conduct a detailed survey of the organic fertilizer market in various states in the United States to understand demand, competition and policy support.
- Cooperation Model: Cooperate with local farms, food processing companies or waste management companies to ensure raw material supply and sales channels.
- Environmental Technology: Use advanced environmental technology to ensure that the production line complies with US environmental regulations.
- Brand Building: Improve the market competitiveness of products through certification (such as organic certification) and brand promotion.
There is a very good prospect for building an organic fertilizer production line in the United States, especially driven by organic agriculture, environmental policies and consumer demand, market demand will continue to grow.
However, investors need to fully consider challenges such as market competition, initial investment and environmental requirements, and formulate a reasonable business plan to ensure the successful operation of the project. By leveraging the technological advantages and policy support of the United States, the organic fertilizer production line is expected to become an investment project with both economic and environmental benefits.
If you are interested in building an organic fertilizer production line in United States project, feel free to contact RICHI Machinery for technical support on organic fertilizer processing plant design, equipment configuration, production line layout, civil engineering solutions, etc.!