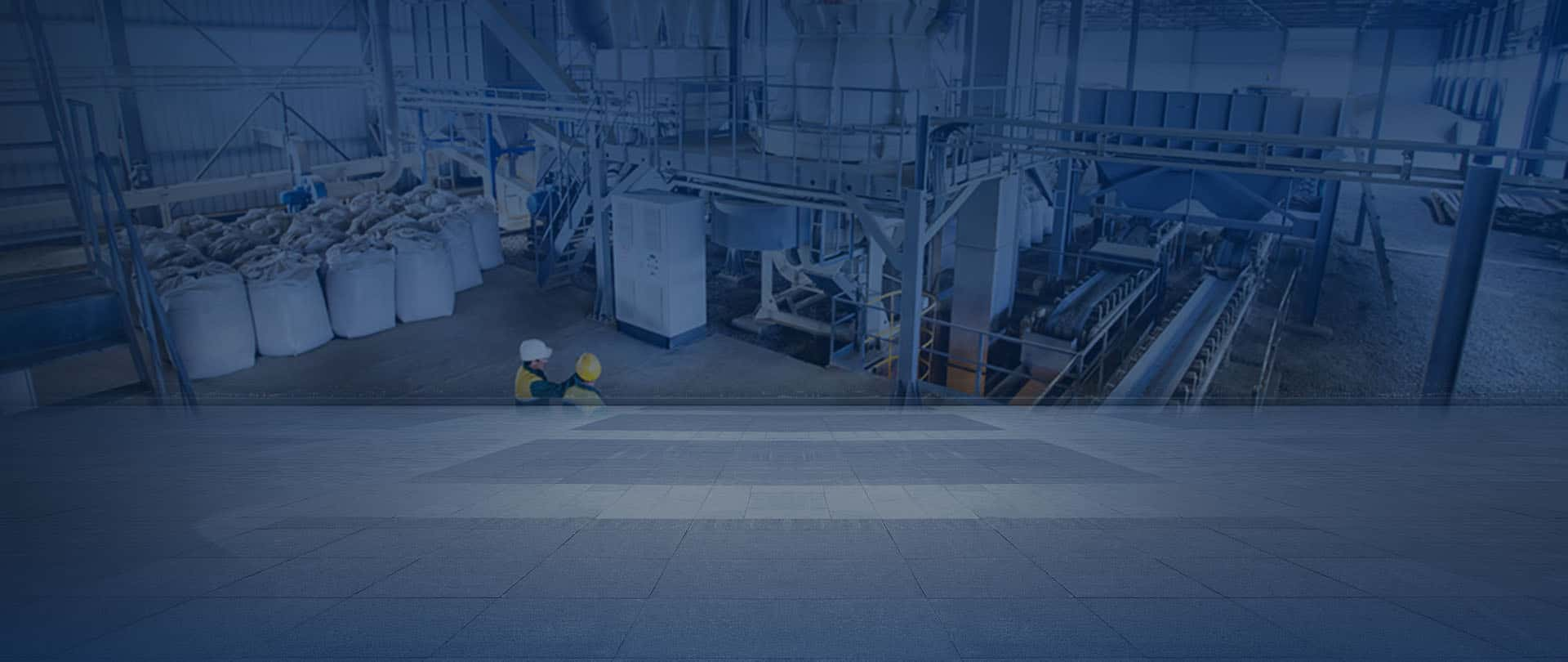
Fertilizer Mixing Machine
Fertilizer mixing machine is a versatile batch type mixer for blending powder & bulk materials.
This blender is broadly used in fertilizer, feed, food, chemical, pharmaceutical, building materials, plastic, and other processing industries, whichever need to blend raw materials homogenously together.
RICHI MACHINERY manufacture fertilizer mixing equipment. Standard and custom designs are available to meet the varied fertilizer processing requirements of our customers.
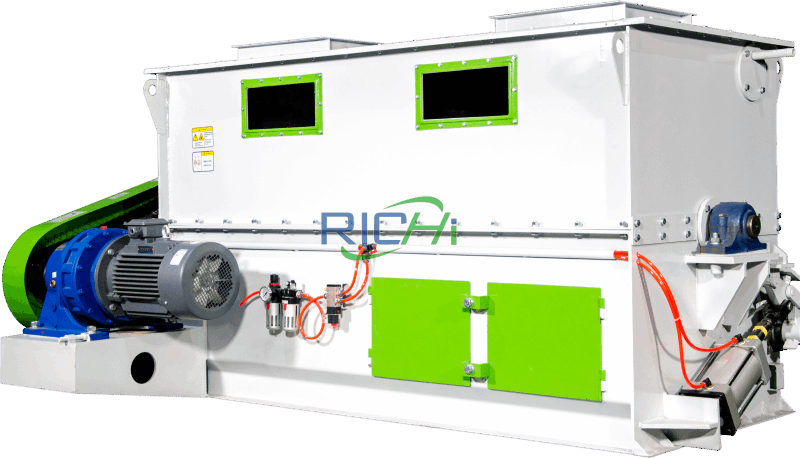
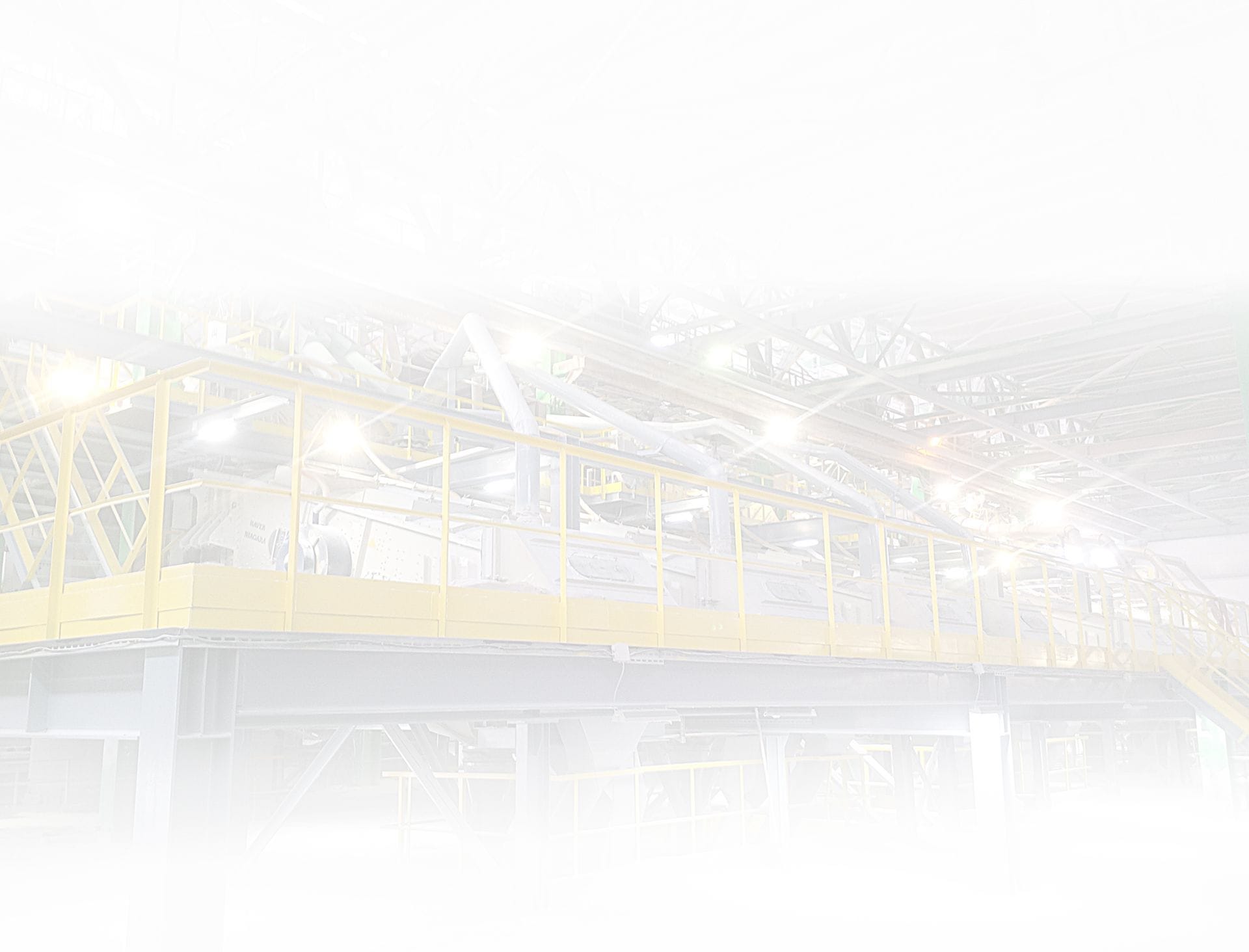
fertilizer mixer for sale
— Richi Machinery —
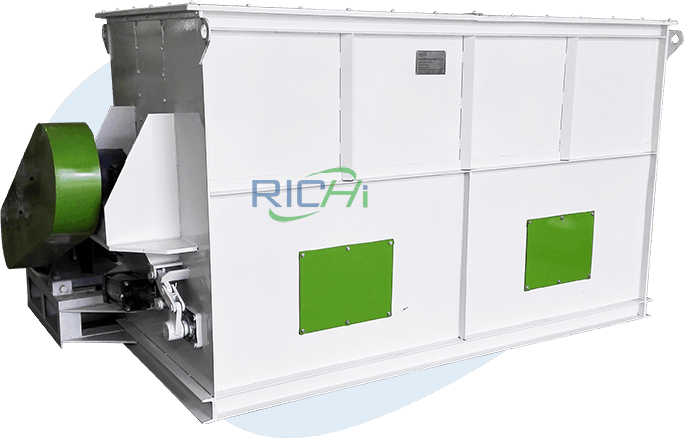
The batch-style RICHI fertilizer mixing machine is a proven workhorse in bulk solids processing. The mixer has a wide range of applications and can mix powders with powders, powders with liquids, especially paste-like, viscous or heavy materials.
Our fertilizer mixers mainly use ribbon structure. These mixers are the backbone of fertilizer industry when it comes to mixing. They are the most popular mixing equipment thanks to their relatively low initial purchase cost, maintenance costs, and production costs per pound of product produced. Industrial ribbon mixers can blend almost anything.
In the fertilizer processing technology, this mixer can evenly mix nitrogen, phosphorus, potassium and other elements to make compound fertilizer. It can also mix organic materials such as livestock and poultry manure and straw to make organic fertilizer. It can evenly mix trace elements such as zinc, iron and boron into fertilizer.
From fertilizer, manure, feed, seasonings and beverage mixes to pharmaceutical, chemical, plastic, and agricultural powders or granules, the wide range of applications that are efficiently and economically processed in a RICHI fertilizer mixer makes it a popular and versatile choice in various industries.
This blender can heat, cool, or dry materials under vacuum. It can also coat solid particles with small amounts of liquid. In addition, it can mix wet applications such as soups, batters, slurries and certain pastes.
0.5-20
Mixing amount per batch (KG/P)
4-45
Power(KW)
● RICHI MACHINERY
application of fertilizer mixing machine
Fertilizer mixers can process a wide variety of raw materials, including livestock and poultry manure, straw, agricultural and forestry waste, garden waste, industrial waste, kitchen waste, inorganic fertilizer raw materials, trace element fertilizers, soil conditioners, sludge, brewer’s grains, seaweed, bagasse, beet pulp, pulp waste, animal hair, etc.
By mixing these raw materials, high-quality organic fertilizers, compound fertilizers and soil conditioners can be made to meet the needs of different crops and soils. When using a fertilizer mixer, it is necessary to pre-treat the raw materials according to their characteristics, and control the mixing ratio and moisture to ensure the mixing effect and fertilizer quality.
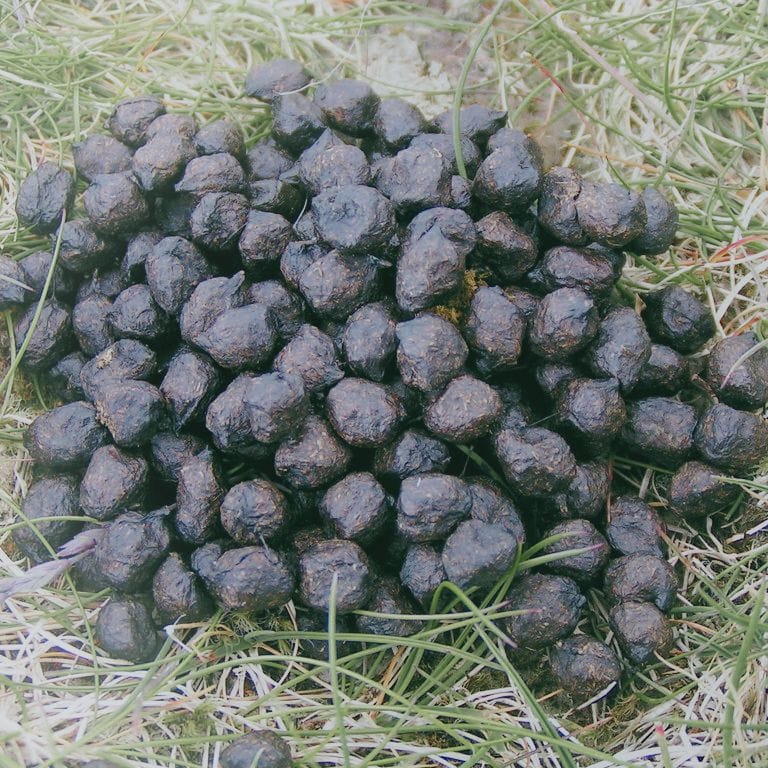
animal manure
Fertilizer mixers can mix livestock and poultry manure with other dry raw materials to adjust their moisture content and improve their physical properties for subsequent composting or pelleting. When mixing, it is necessary to control the moisture content.
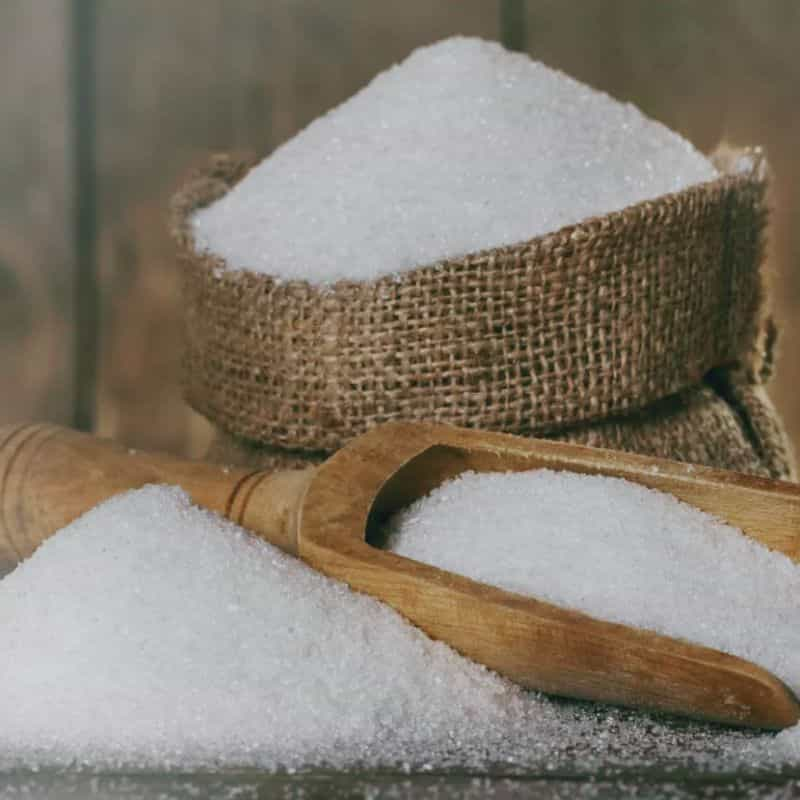
Inorganic raw materials
Fertilizer mixers can evenly mix a variety of inorganic raw materials, trace elements, and soil conditioners to make compound fertilizers that meet the needs of crops for nutrients such as nitrogen, phosphorus, and potassium.
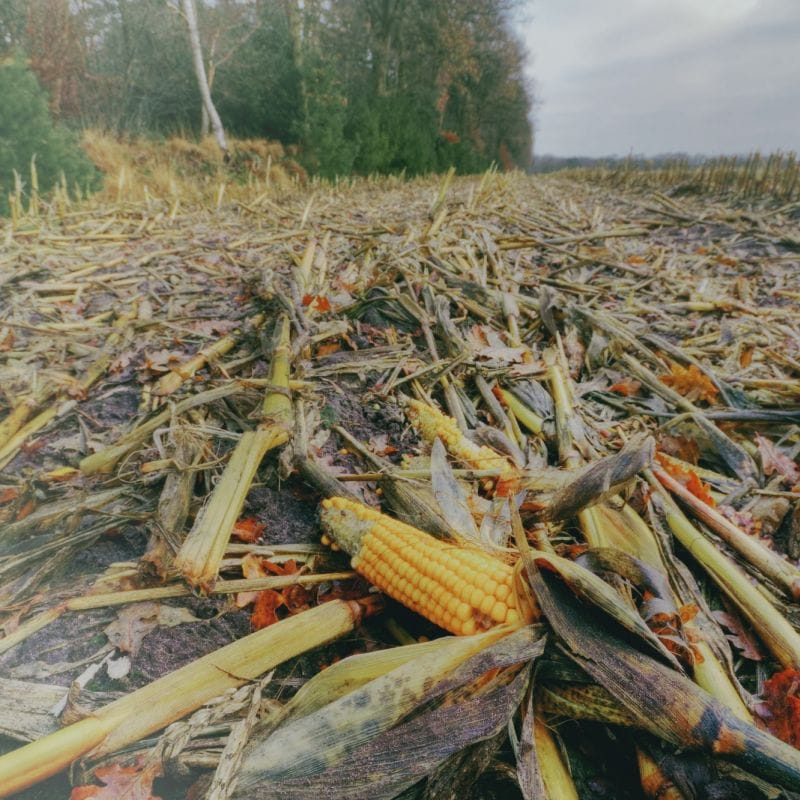
Agricultural and forestry waste
The fertilizer mixer can crush the straw and mix it with other raw materials (such as livestock and poultry manure) to adjust the carbon-nitrogen ratio, promote the fermentation process, and make high-quality organic fertilizer. The straw needs to be crushed to an appropriate particle size in advance so that it can be mixed evenly.
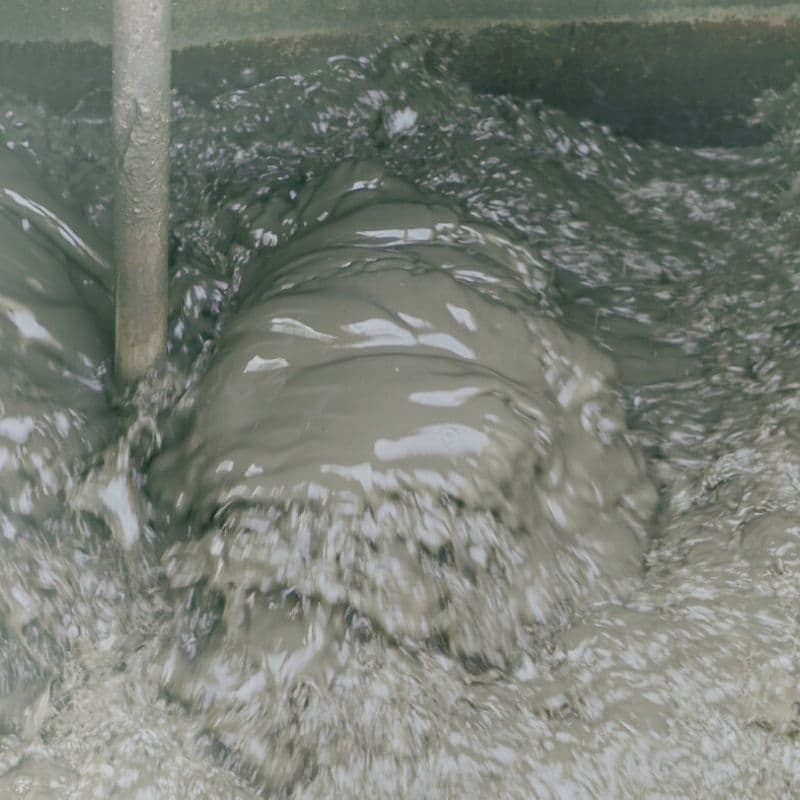
Sludge
Fertilizer mixers can mix sludge with other raw materials, adjust its water content and carbon-nitrogen ratio, and make it into organic fertilizer or soil conditioner. Sludge needs to be tested to ensure that its heavy metal content meets the standard.
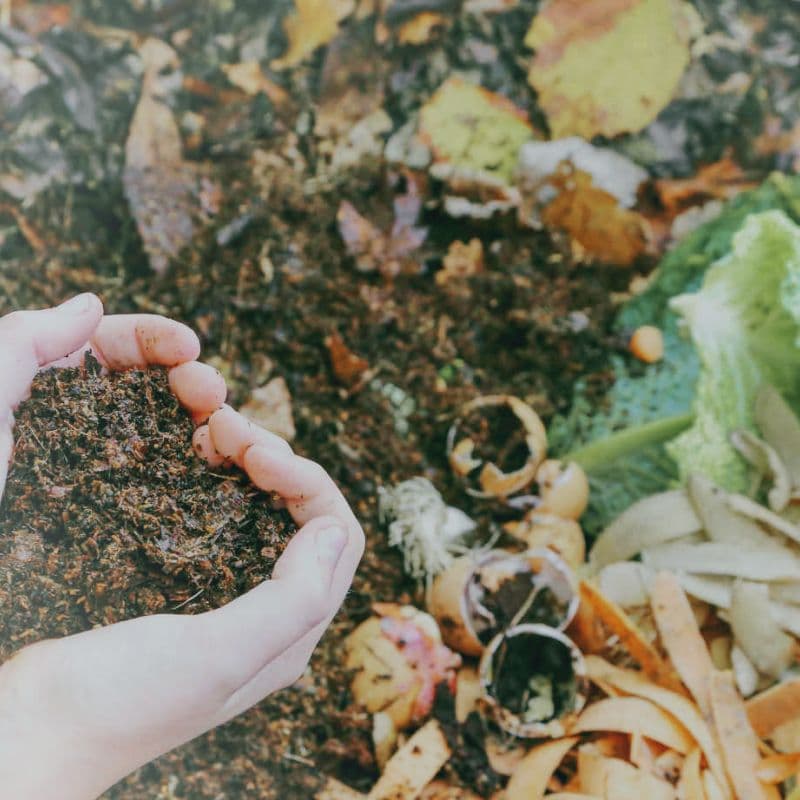
food waste
Fertilizer mixers can mix food waste with other raw materials to adjust their carbon-nitrogen ratio and water content for subsequent composting. Food waste needs to be pre-treated (such as removing grease and salt) to avoid negative impacts on soil and crops.
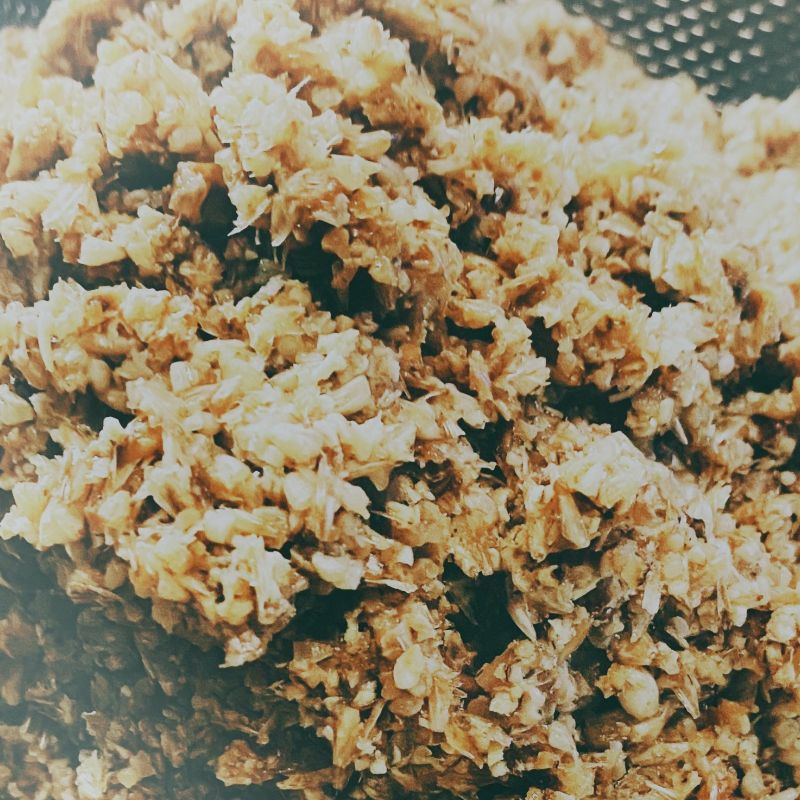
Brewer’s grains
Fertilizer mixers can mix brewer’s grains with other raw materials to make high-quality organic fertilizer. Brewer’s grains need to be dried in advance or mixed with other dry raw materials to avoid excessive moisture affecting the mixing effect.
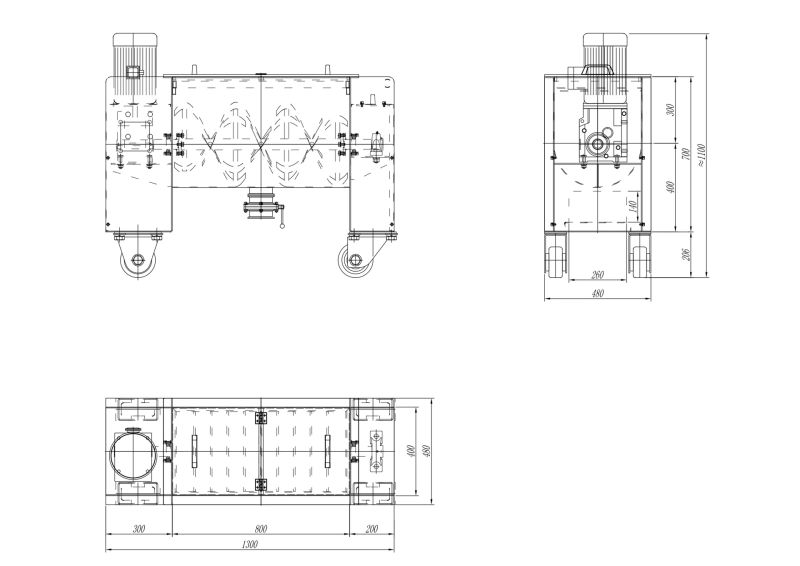
Richi Machinery
how does a fertilizer mixing machine work?
Our fertilizer mixing equipment consist of a U-shaped horizontal trough and a solid agitator shaft mounted with spokes that support outer and inner helical blades called ribbons. Powered by a gearmotor drive, the agitator rotates and produces a peripheral speed of up to approximately 300 fpm.
The ribbons move material radially — the outer ribbons move the ingredients in toward the blender’s center, and the inner ribbons move ingredients out toward the blender wall. The difference in the outer and inner ribbons’ speeds moves material laterally or axially (along the blender’s horizontal axis), in opposite directions. The radial and two-way axial mixing actions promote small-scale random motion (diffusion), large-scale random motion (convection), and shear resulting from particle-to-agitator, particle-to-wall, and particle-to-particle collisions.
The most effective design of ribbon layout is the double spiral in which the outer ribbon moves the product in one direction and the inner ribbon moves it in the opposite direction. The helical ribbons rotate and move materials both radially and laterally, and thus mixing materials form convection & tumble motion to insure thorough mixing homogeneity in short cycle times (usually 2-10 minutes). The ribbon agitators are designed for loading ratio that will be 40% – 60% of ribbon blender’s nominal capacity.
Technical features of fertilizer mixing machine
— Richi Machinery —
The fertilizer mixing machine from RICHI MACHINERY runs from a 0.5m³ blender up to a 7.5m³. Power can run up to 45kw, and each machine is sized and constructed based on the bulk density and special features of the customer’s product. This ensures you get the performance you need for the products you produce. Plus, our designs focus on high levels of sanitation and safety while requiring only low levels of maintenance.
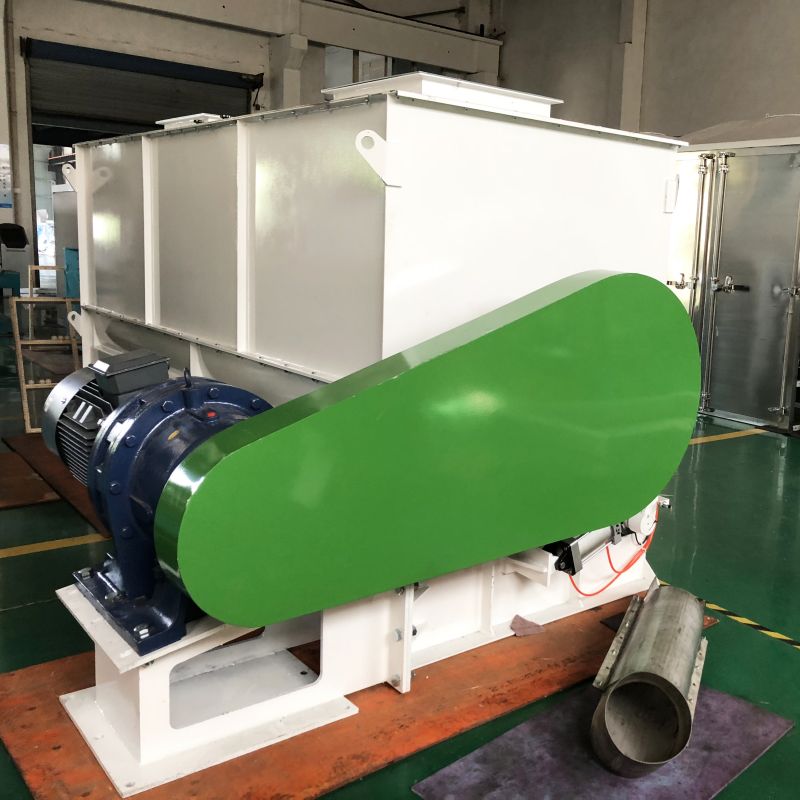
The fertilizer mixing equipment adopts a double-ribbon structure, which can quickly lift the material from the bottom to the top and then drop it from the top, forming a strong three-dimensional mixing effect, ensuring that the material reaches a highly uniform mixing state in a short time.
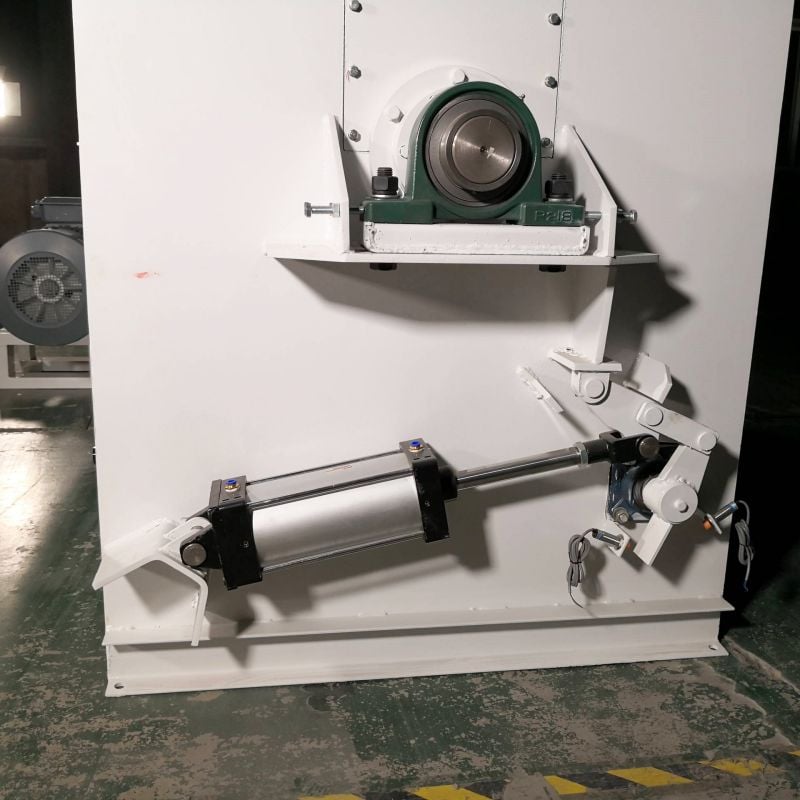
The bottom discharge method of the fertilizer mixer machine adopts a pneumatic large-opening structure for powder materials, which has the advantages of fast unloading and no residue.
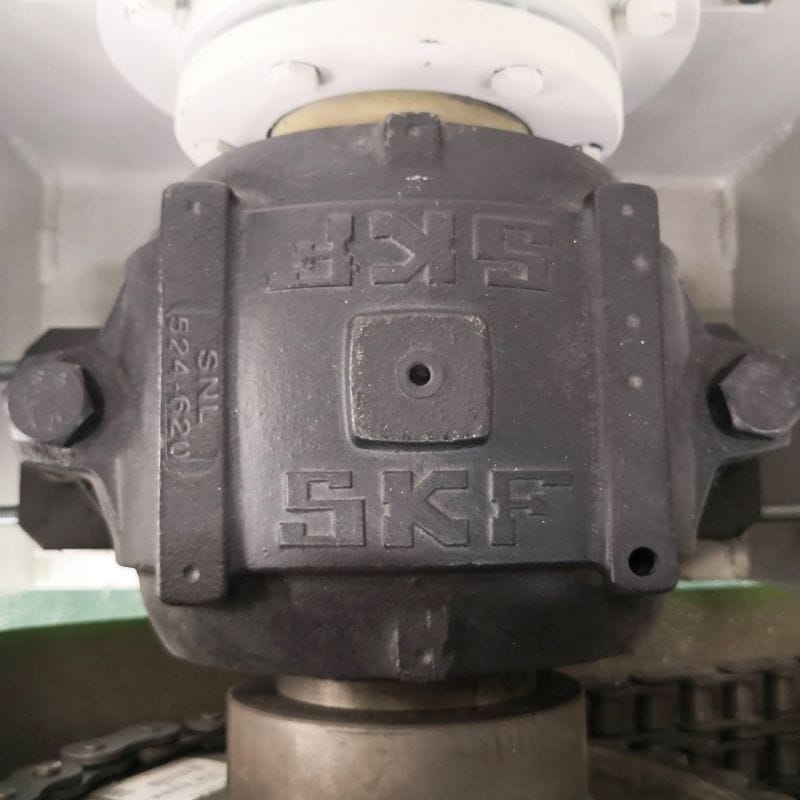
The fertilizer mixer adopts an optimized ribbon structure and drive system to reduce the energy consumption of the equipment during operation. Compared with traditional mixers, the ribbon mixer has lower energy consumption and reduces production costs while ensuring efficient mixing.
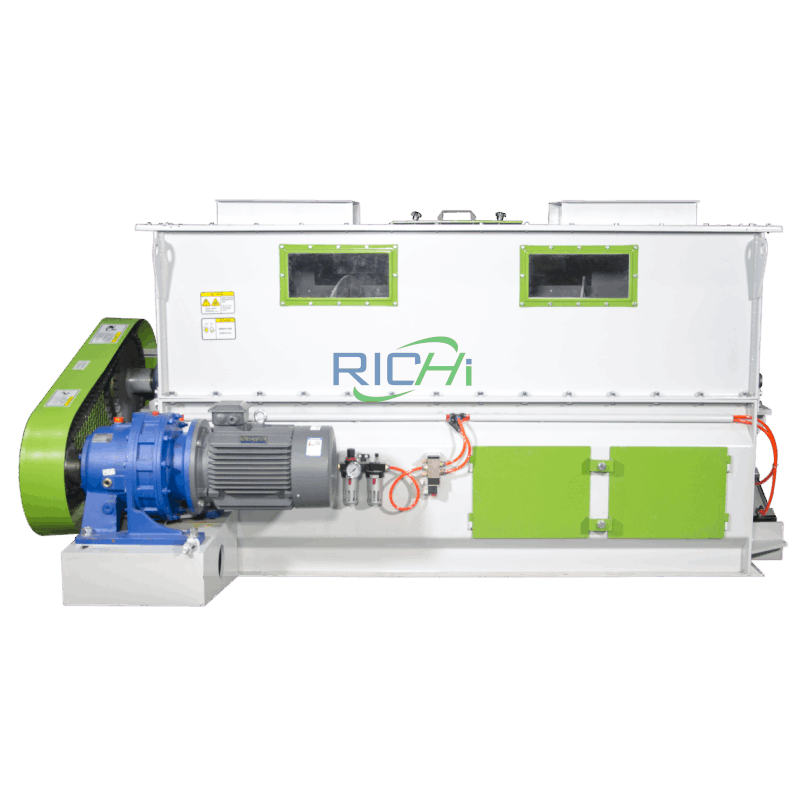
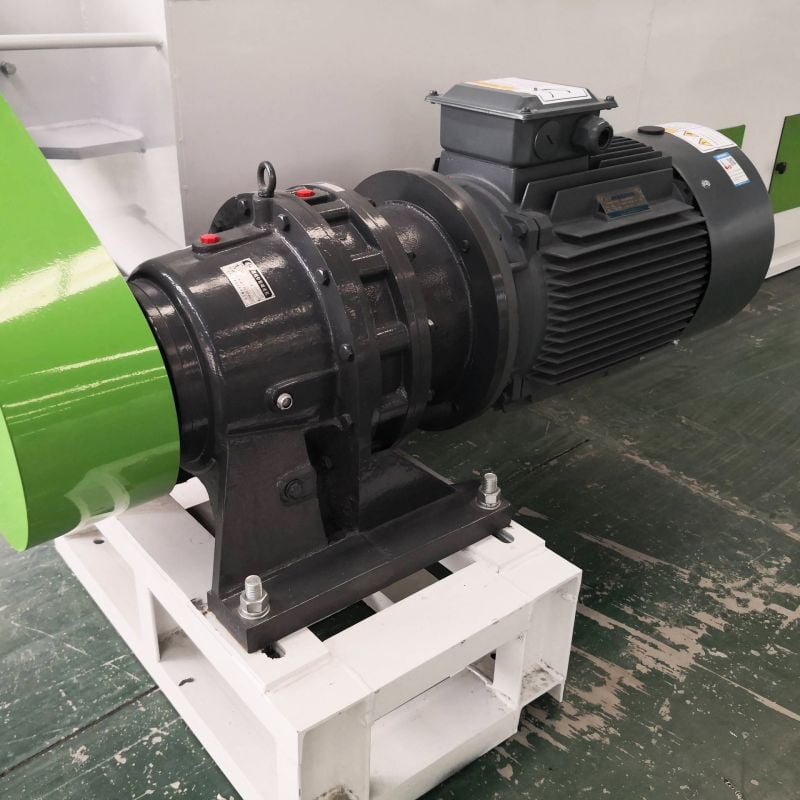
The double-ribbon design of the fertilizer mixing machine allows the material to be continuously divided, sheared and reorganized during the mixing process, ensuring that each part of the material can be fully contacted.
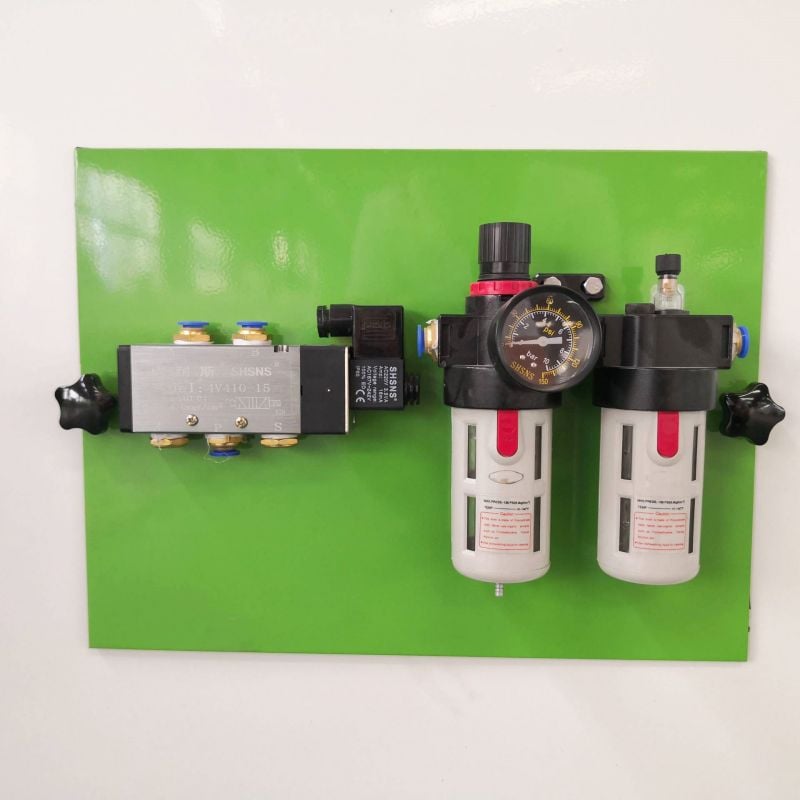
The mixer can handle materials of various forms and specific gravities, including powder, granules, flakes, fibers and sticky materials. Whether it is light or heavy materials, the ribbon mixer can achieve uniform mixing without damaging the materials.
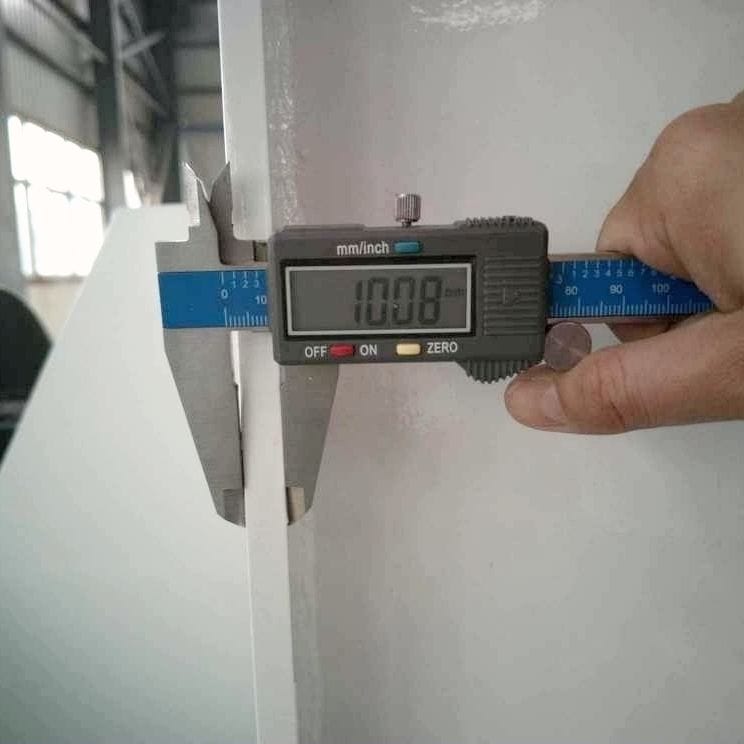
The fertiliser mixer adopts a fully enclosed design, combined with an efficient sealing device to ensure that there is no dust leakage during the mixing process. It not only improves the working environment, but also reduces the waste of raw materials, and is particularly suitable for handling materials that are prone to dust.
fertilizer mixing machine parameters
Model | Power (kw) | Mixing amount per batch (kg/P) | Effective volume (m³) |
SLHY0.5A | 4 | 250 (manual feeding) | 0.5 |
SLHY1.0A | 7.5 | 500 (manual feeding) | 1 |
SLHY1.0A | 7.5 | 500 (pneumatic feeding) | 1 |
SLHY 2.5L | 18.5 | 1000 (pneumatic feeding) | 2.5 |
SLHY3.5L | 30 | 1500 (pneumatic feeding) | 3.5 |
SLHY5.0L | 37 | 2000 (pneumatic feeding) | 5 |
SLHY7.5L | 45 | 3000 (pneumatic feeding) | 7.5 |
Advantages of fertilizer mixing machine
The fertilizer mixer machine has become an ideal mixing equipment for the fertilizer industry due to its efficient mixing ability, high uniformity, strong adaptability, low energy consumption design, easy cleaning and maintenance, and good sealing. Its unique technical features not only improve production efficiency, but also ensure product quality, meeting the high requirements of the fertilizer industry, especially the organic fertilizer and compound fertilizer industries, for mixing processes.
Custom Design
RICHI fertilizer mixer machines’ drive components is custom equipped to ensure trouble free operation for decades of years.
Sanitary Polish
RICHI fertilizer mixing machine blenders are fine polished, the surface is smooth, scratch free.
Easy Cleaning
Usually, the opening at top cover is very large to touch into the inner surface for cleaning purpose.
Good mixing effect
The mixing uniformity can reach more than 99%, which is particularly suitable for industries with high requirements for mixing uniformity, such as the mixing of trace elements and basic fertilizers in fertilizer production.
Easy to operate
The use of the fertilizer mixer is very convenient. Just put the materials into the machine and set the mixing time and speed.
Automatic control:
Equipped with PLC control system to realize automatic operation and reduce manual intervention.
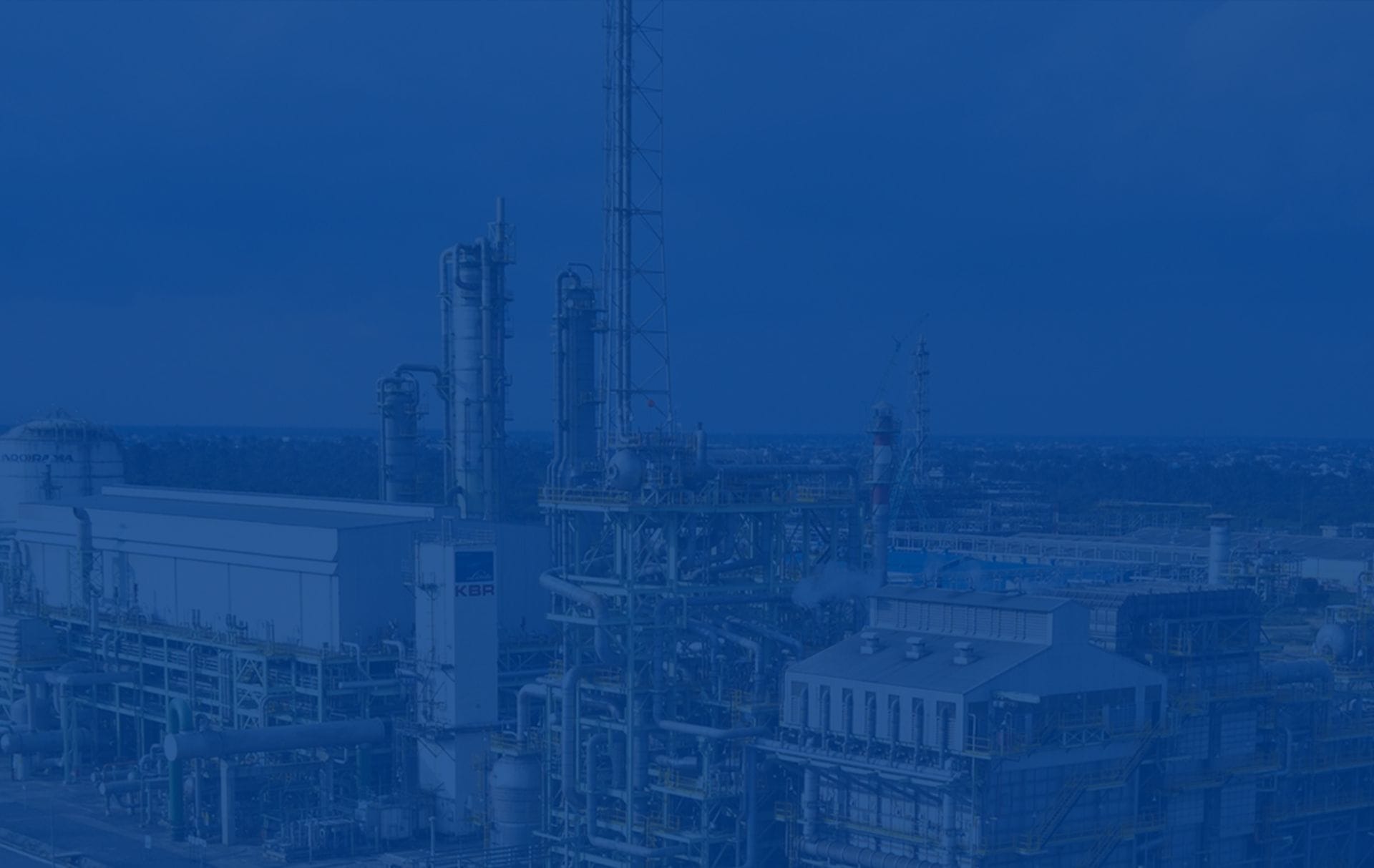
fertilizer mixing machine project
Currently, our fertilizer mixing machine is being used in more than 400 fertilizer processing sites around the world. Among these projects, nearly 20% of the fertilizer mixers are customized. We design your fertilizer mixing equipment exactly how you need it, with many optional and custom features available. For example, our blenders can be constructed in a standard-duty, heavy-duty, or extra-heavy-duty form. We can manufacture them with 316 SS, 304 SS, mild steel, or other types and grades of steel.
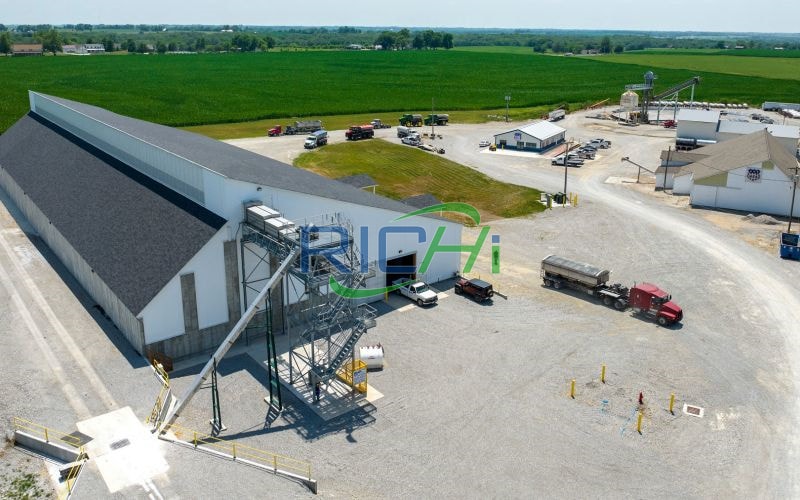
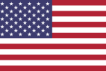
● USA
fertilizer mixer for sale United States
- Applied to: Chicken manure fertilizer processing project
- Mixer model: SLHY7.5L
- Mixed raw materials: chicken manure, straw, wood
→
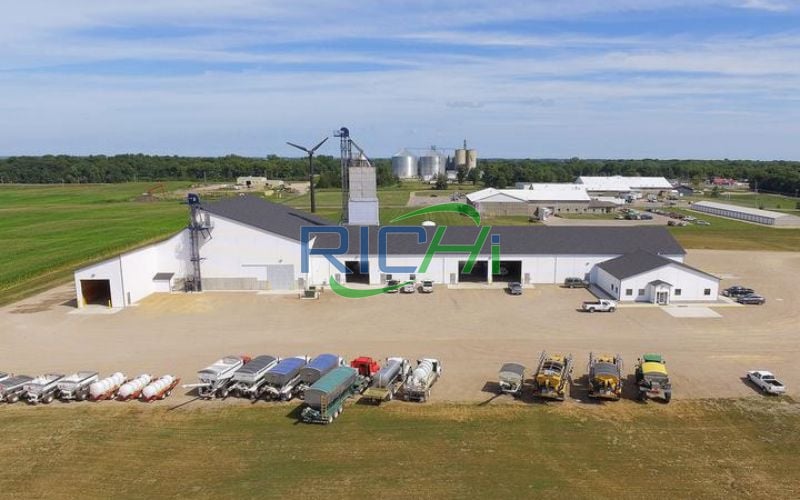
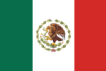
● Mexico
fertilizer mixing equipment in Mexico
- Applied to: compound fertilizer processing project
- Mixer model: SLHY3.5L
- Mixed raw materials: NPK, Urea
→
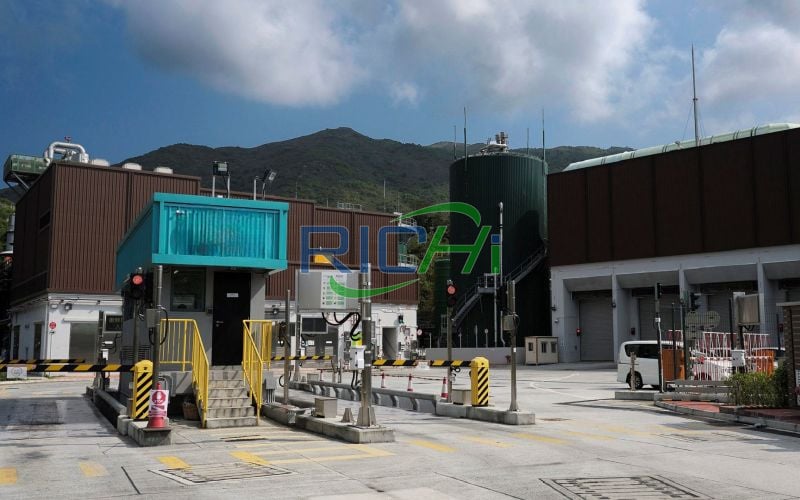
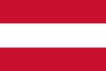
● Austria
fertilizer mixer machine in Austria
- Applied to: poultry manure organic fertilizer processing project
- Mixer model: SLHY5.0L
- Mixed raw materials: poultry manure, wood
→
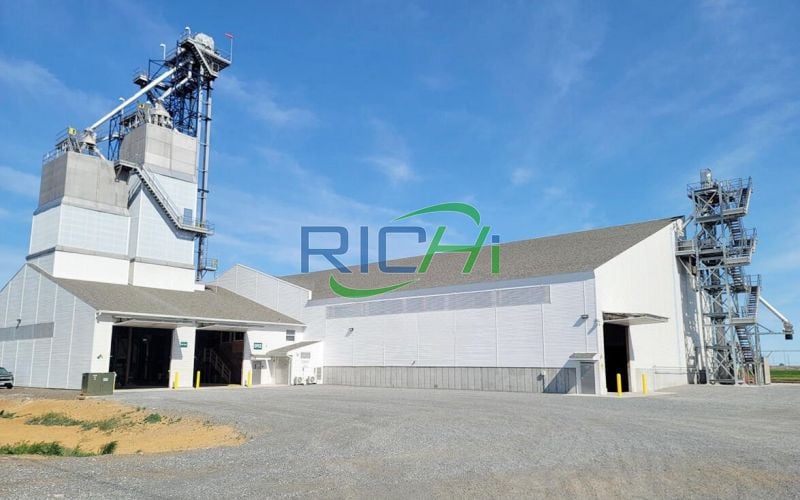
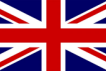
● UK
organic fertilizer mixer machine in Britain
- Applied to: pig manure fertilizer processing project
- Mixer model: SLHY 2.5L
- Mixed raw materials: pig manure, straw
→
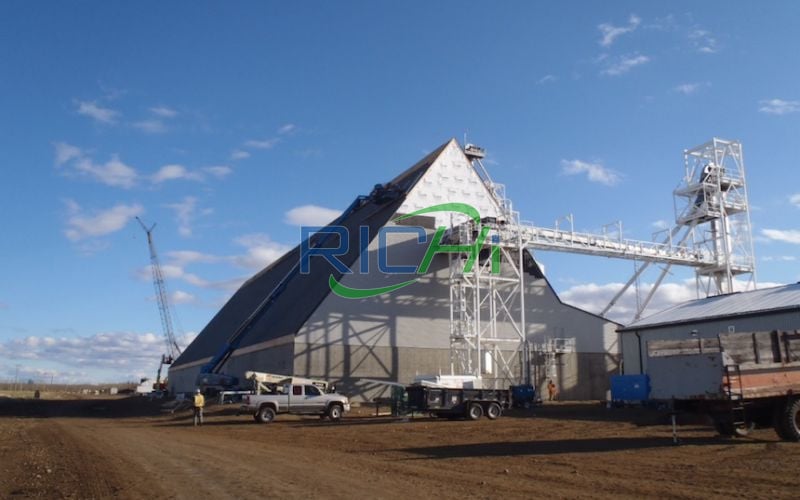
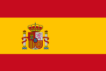
● Spain
organic fertilizer mixer for sale Spain
- Applied to: livestock manure organic fertilizer processing project
- Mixer model: SLHY1.0A
- Mixed raw materials: livestock manure, olive residue
→
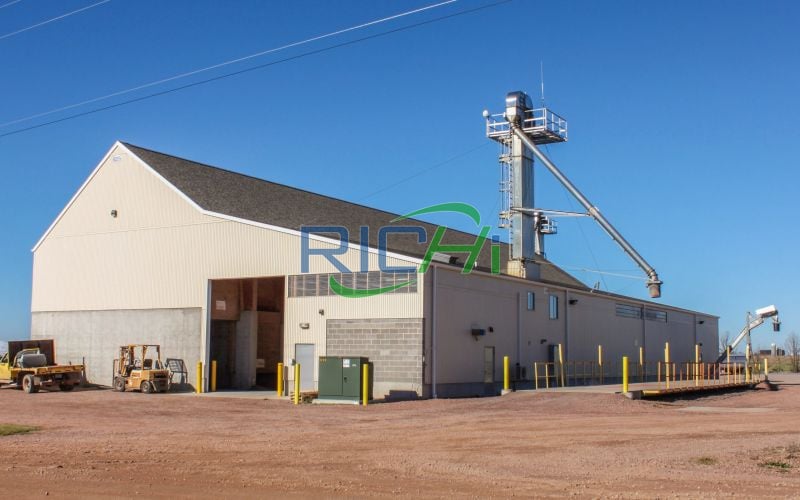
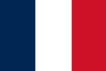
● France
manure mixing machine for sale France
- Applied to: cattle manure fertilizer processing project
- Mixer model: SLHY 2.5L
- Mixed raw materials: pig manure, crop
→
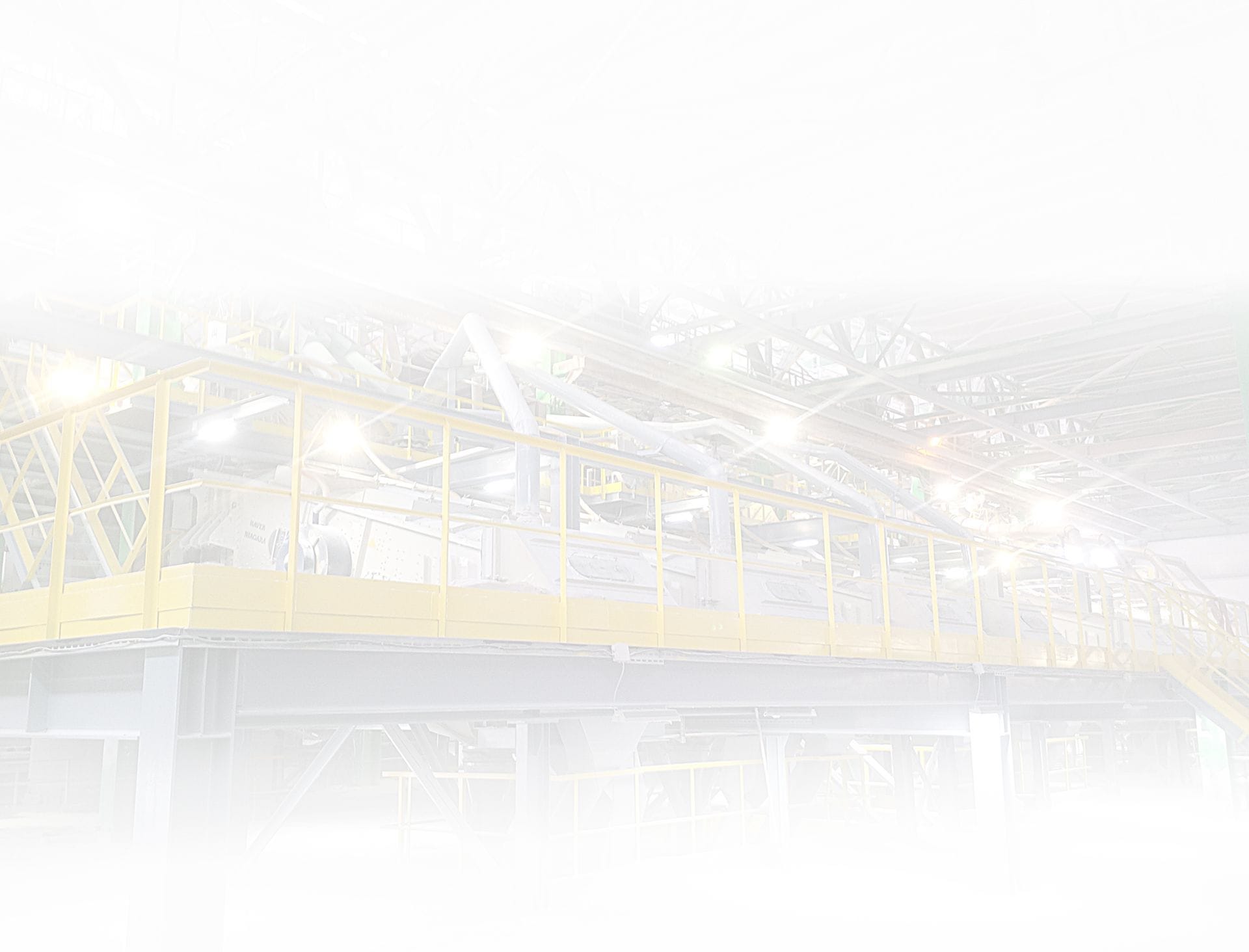
fertilizer mixer machine price
— Richi Machinery —
The price of a fertilizer mixer is usually between 3,000 and 50,000 US dollars. The fertilizer mixing machine cost is affected by many factors, and the specific price depends on the following factors:
- Model and capacity: large scale mixer is more expensive, and small equipment is cheaper.
- Brand and quality: well-known brand mixer is more expensive, but the quality is guaranteed.
- Function and degree of automation: mixer with a high degree of automation is more expensive.
- Material and manufacturing process: mixer using high-quality materials and advanced technology is more expensive.
- After-sales service: mixer with perfect after-sales service is more expensive.
Model | FOB Price (USD) |
SLHY0.5A | 3,000-6,000 USD |
SLHY1.0A | 6,000-10,000 USD |
SLHY1.0A | 10,000-14,000 USD |
SLHY 2.5L | 27,000 -32,000 USD |
SLHY3.5L | 30,000-40,000 USD |
SLHY5.0L | 35,000-45,000 |
SLHY7.5L | 40,000-50,000 |
If you want to buy a fertilizer mixer, be sure to compare more. I hope that product quality is the key to your final decision whether to buy it or not, not just the price. After all, the higher the quality, the lower the later maintenance cost and the longer the service life.
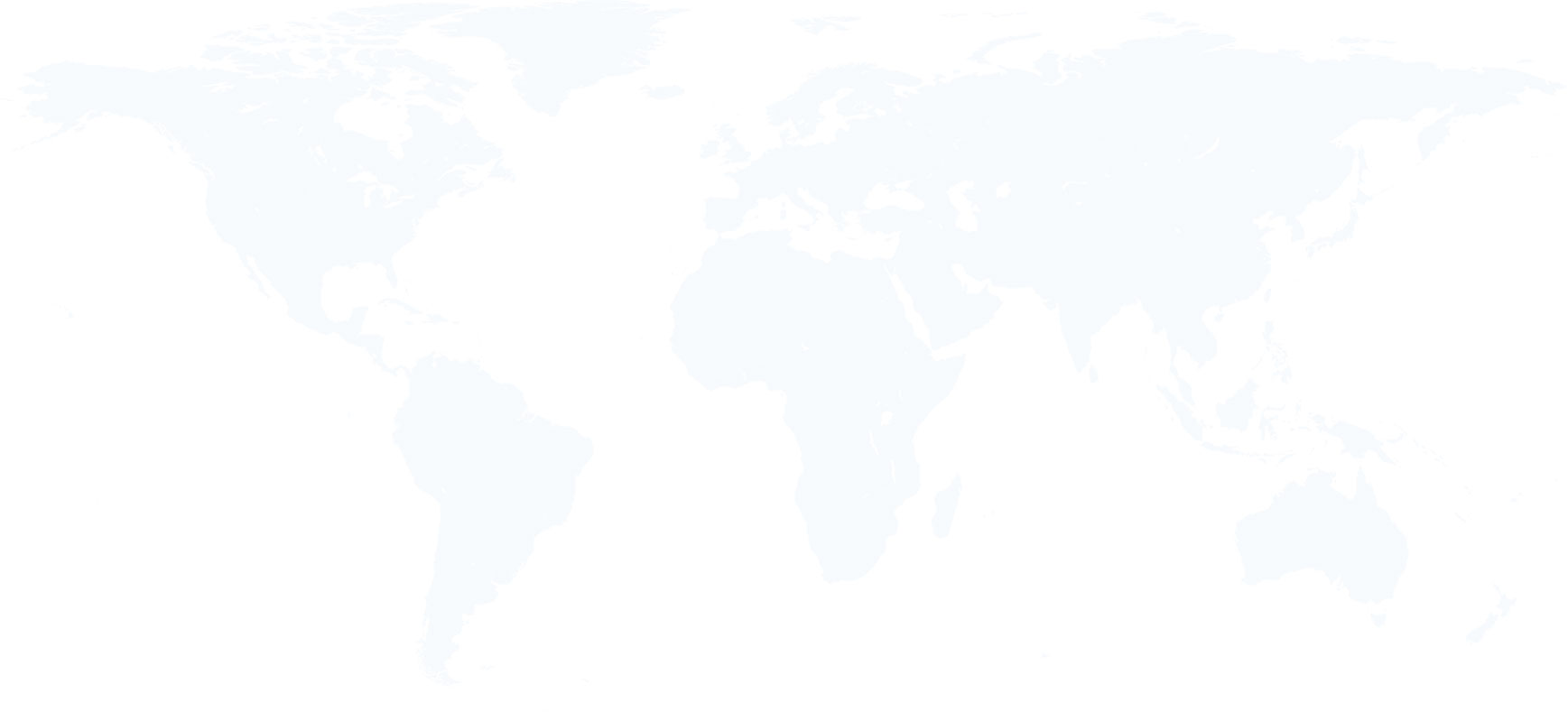
RICHI MACHINERY
Related Products
As part of wide fertilizer mixer range, RICHI provides different models of fertilizer mixing machines specially tailored to the requirements of various fertilizer manufacturers.
You can choose the corresponding mixer according to your requirements, or let our technical consultant recommend it for you.
Our fertilizer mixing equipment meets the toughest standards for quality and long-term performance. RICHI’s attention to detail is meticulous, because every detail in design and fabrication translates to an increase in production. Our fertilizer blenders are capable of performing a variety of mixing operations.
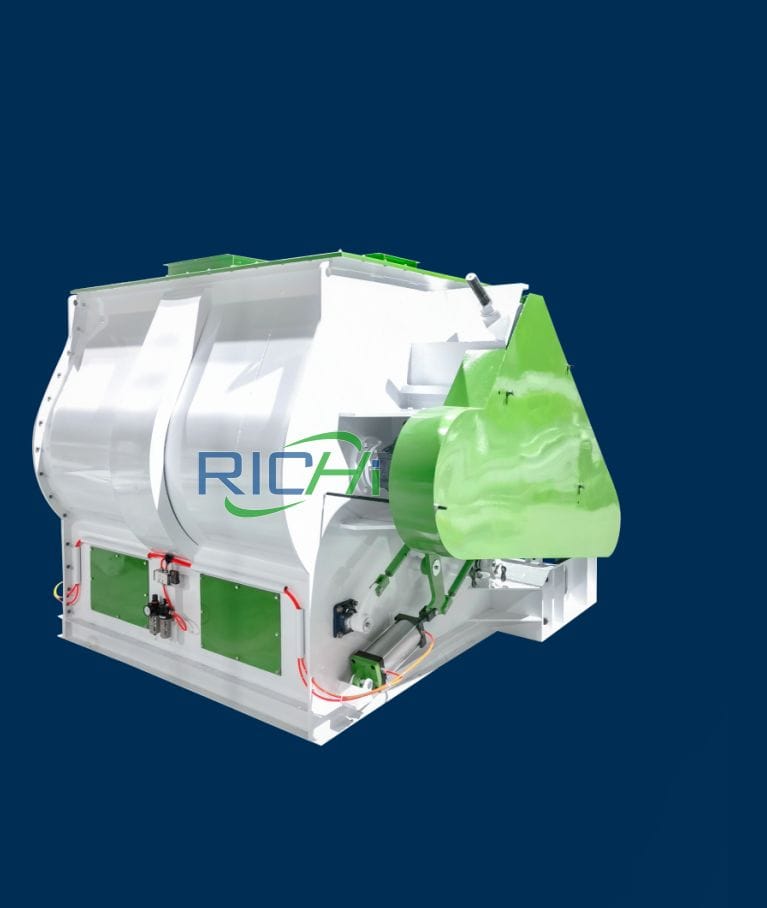
compound fertilizer mixer
The materials are mixed horizontally by the horizontally placed stirring shaft and paddles. The mixing uniformity is high, which is suitable for large-scale production and for mixing a variety of raw materials.
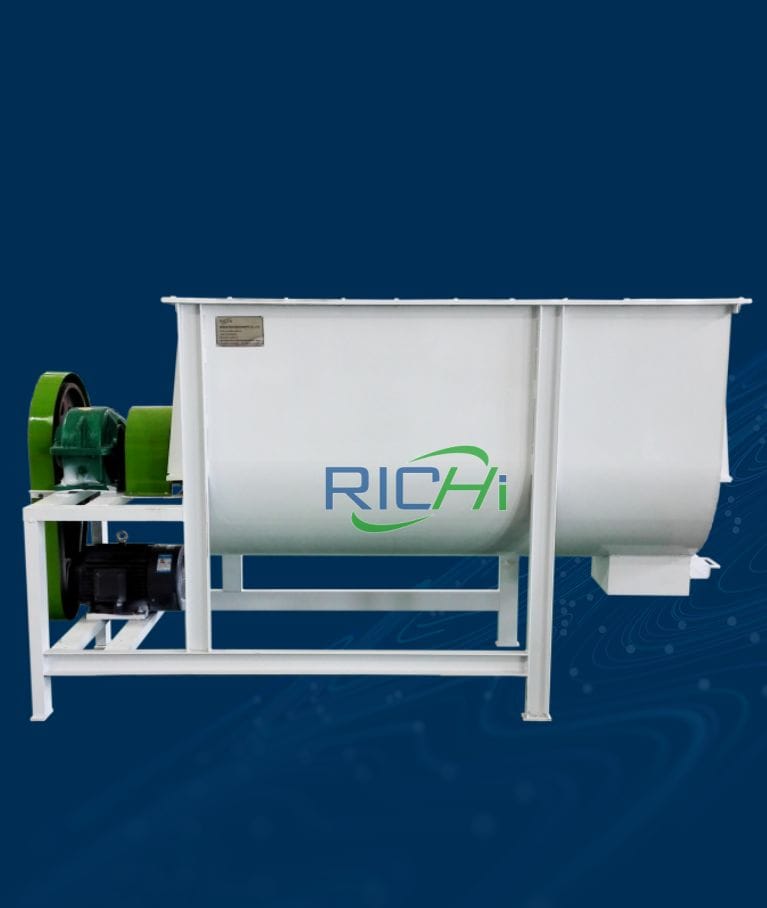
manure mixing machine
Manure mixer can blend powder & granules evenly. You can use it for organic fertilizer production. RICHI MACHINERY provides complete using methods for you.
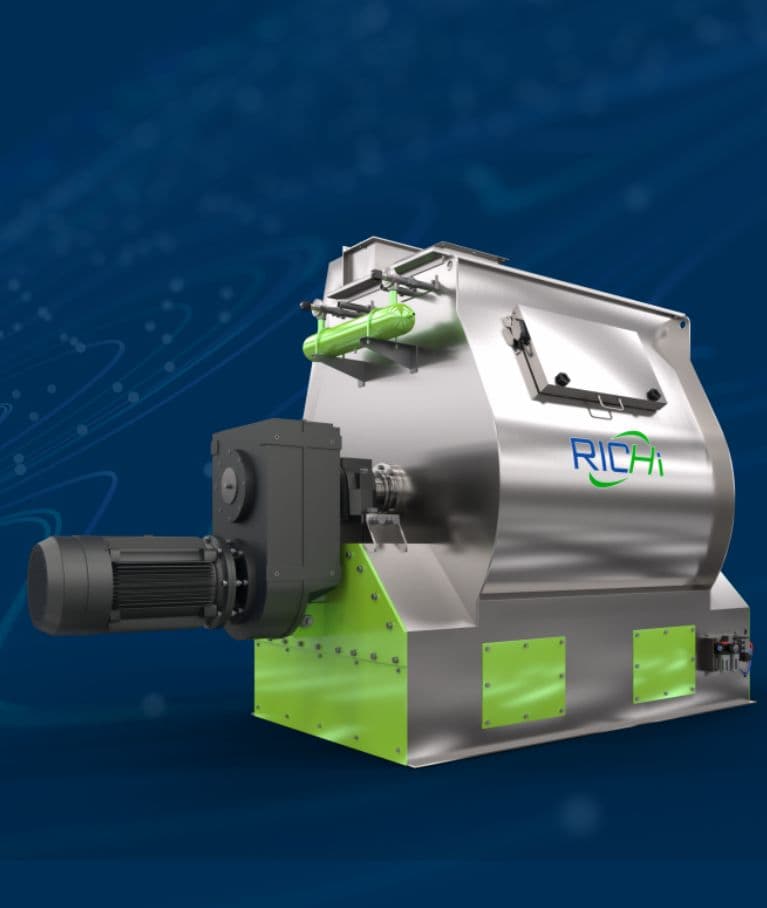
npk fertilizer mixer
NPK fertilizer mixer overcomes the mixtures chromatography and distributaries phenomena caused by different proportion of raw materials and particle size.
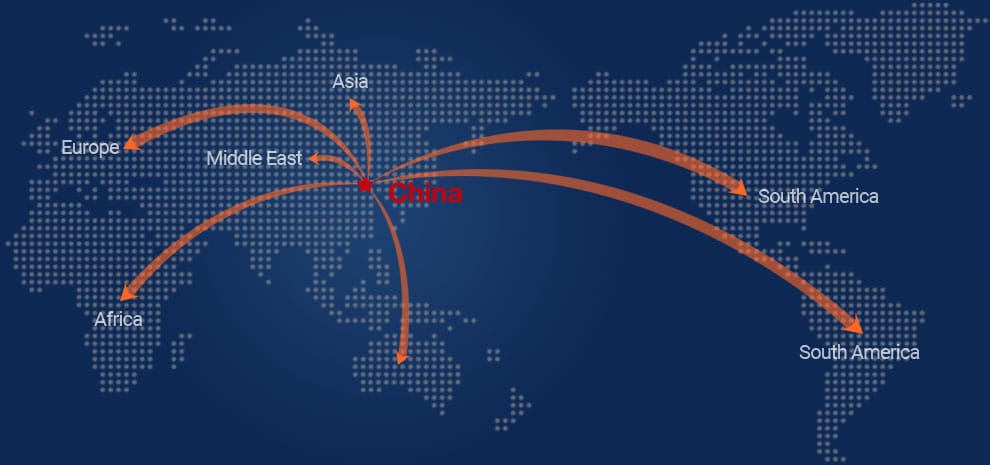

RICHI fertilizer mixing machines are the ideal solution to meet the requirements of the fertilizer market in terms of quality, maintenance and mixing technology.
How to choose a fertilizer mixing machine?
There are several key factors to consider when choosing a fertilizer mixing machine:
- Material properties: The humidity, viscosity, particle size and density of the fertilizer raw materials will affect the mixing effect. Materials with higher humidity may cause caking or adhesion, so it is necessary to choose equipment that adapts to high humidity. Materials with different particle sizes and densities require different types of mixing equipment, and materials with larger particle sizes or higher densities require stronger stirring forces.
- Mixing effect: The fertilizer mixer needs to ensure the uniform distribution of the various components of the fertilizer and avoid the unevenness of the main components in the fertilizer, which will affect the quality of the final product.
- Production scale and output requirements: Small production lines and large production lines have different requirements for the capacity, efficiency and continuity of fertilizer mixers.
- Energy consumption and efficiency: Efficient fertilizer mixing equipment can save energy and reduce production costs. While ensuring the mixing quality, the energy consumption of the equipment needs to be considered.
- Equipment durability and maintenance requirements: The fertiliser mixer should have a long service life and be easy to maintain and clean, especially when handling different batches or different materials, the cleanliness and corrosion resistance of the equipment are very important.
- Footprint and installation requirements: The size and footprint of the equipment need to be adapted to the space of the production environment. Oversized equipment may not be suitable for small-scale or space-constrained production environments.
- Ease of operation: The fertilizer mixing machine should be easy to operate, adjust and control to reduce the operator’s labor intensity and improve production efficiency.
- Adaptability and flexibility: Selecting mixer with a certain degree of flexibility can adapt to different material types or changes in the production process to ensure the continuity and stability of the production process.
- Cost and cost-effectiveness: The initial investment and subsequent operating costs of the mixer need to be considered comprehensively. Under the premise of ensuring quality and efficiency, choosing cost-effective equipment can reduce the overall production cost.
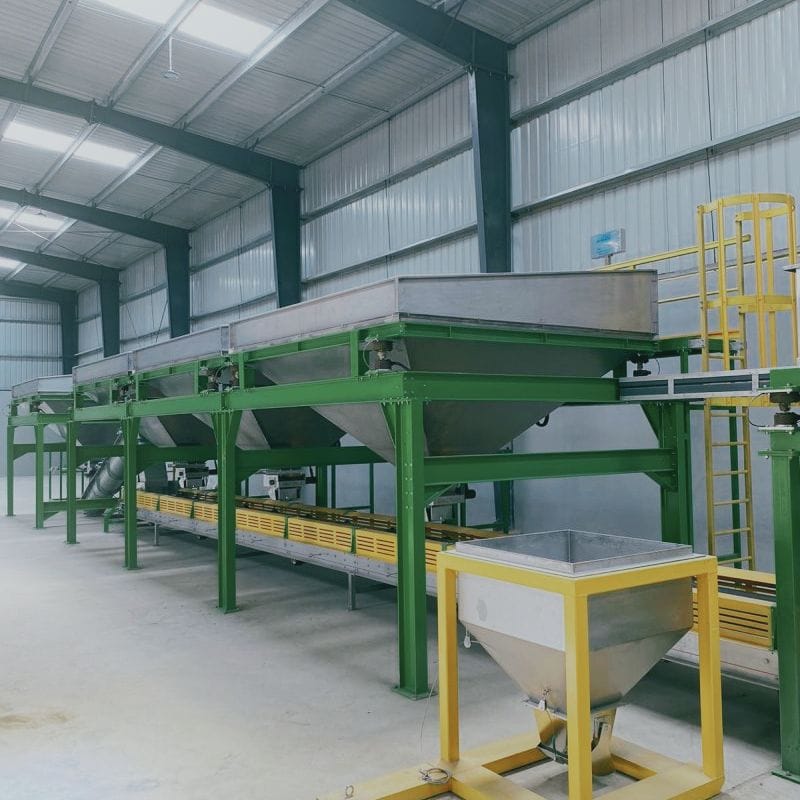
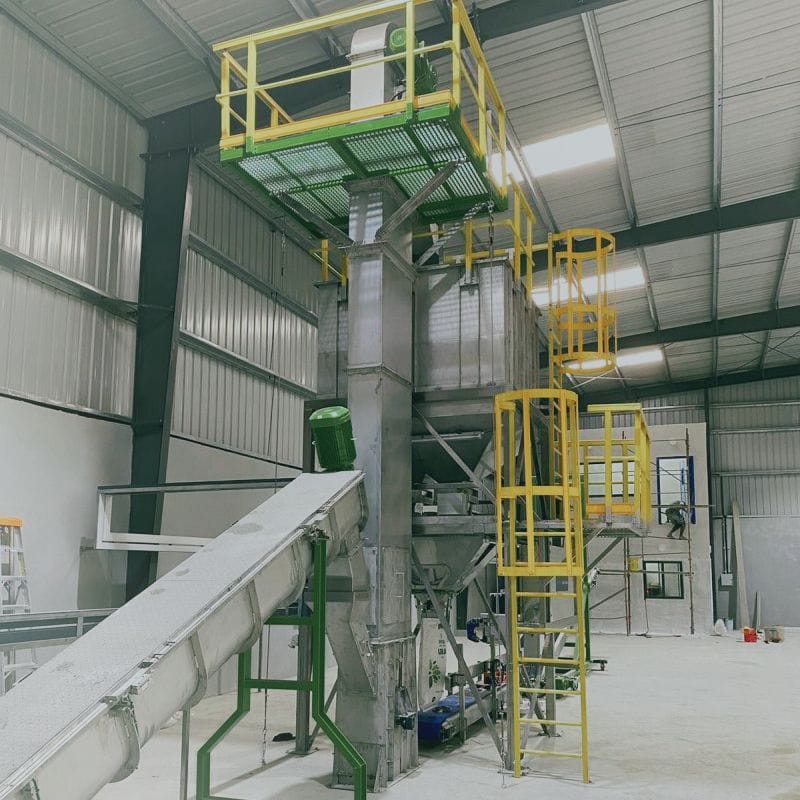
Customized service of fertilizer mixing machine
Due to their popularity and versatility, today many large and small suppliers offer ribbon-type fertilizer mixers. It is important to select a well-equipped mixer that is suitable for your specific application and built by a trusted manufacturer, as quality and performance can vary greatly between OEMs.
Off-the-shelf models are an excellent solution for urgent needs, but it should be noted that customizing a multi-purpose fertilizer mixing machine to meet your own process requirements does not significantly increase capital costs and lead times.
The key is to define your goals in detail so that you can confidently select a mixer that is neither under-specified nor over-engineered. Here are 2 questions to consider carefully.
1.Standard Duty or Heavy Duty?
Before contacting a supplier for pricing, be sure to verify the actual bulk density of your product as accurately as possible. While batch size is always expressed in weight, mixer models are assigned capacity. Therefore, the batch size required (not batch weight) determines the mixer size.
Bulk density also determines horsepower and whether a standard or heavy-duty model is required. Most standard fertilizer mixers can generally handle bulk densities of about 35 lbs/ft3. Heavy-duty ribbon mixers can be used for denser products.
2. Consider the maximum and minimum batches a particular model can accommodate.
Remember that optimal mixing in a fertilizer mixer requires a certain amount of product – at least 30-40% of the rated capacity. When working with a smaller volume, the mixer may not create enough contact between the agitator and the product.
● RICHI MACHINERY
Maybe you are interested in other fertilizer equipment
In addition to fertilizer mixers and fertilizer mixing systems, as a manufacturer and builder of a complete fertilizer production line, we can also provide fertilizer crushers, organic fertilizer granulator machines, fertilizer dryers, fertilizer coating machines, dehydrators, fertilizer balers, fertilizer conveyors, fermentation equipment, deodorization equipment, environmental protection equipment, etc. Mainly equipment used for fertilizer processing, we can design and manufacture them.
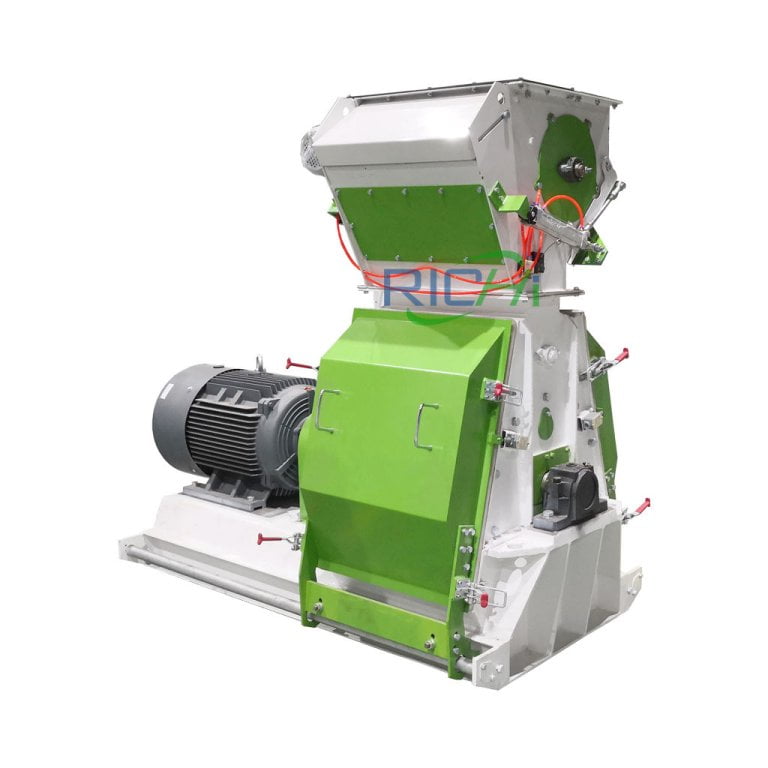
● Crushing
fertilizer crusher machine
Our easy operation chain crusher is mainly used for int and fertilizer processing, and is the ideal equipment to crush many fertilizer materials.
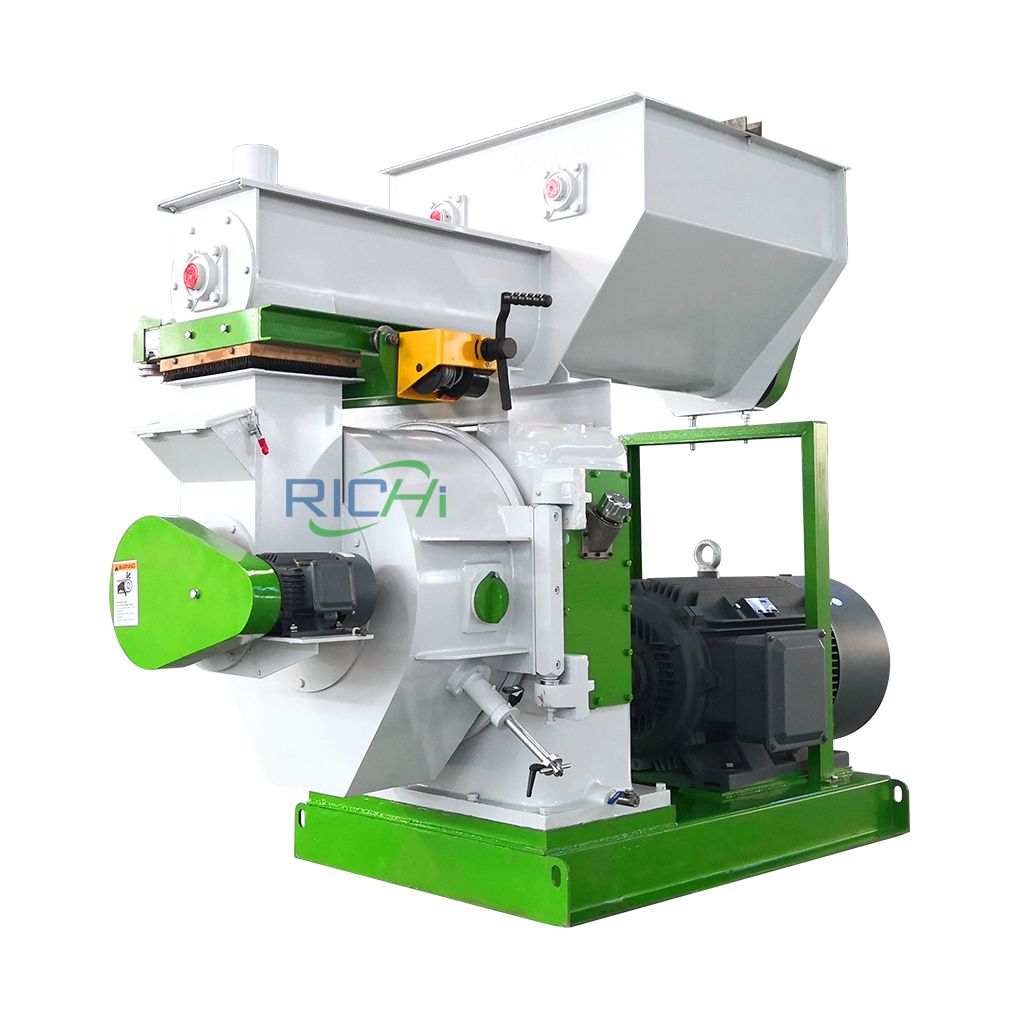
● Pelleting
fertilizer granulator
This fertilizer granulator equipment is developed to keep continuous organic & compound fertilizer granulation, achieving a super-efficient fertilizer granulation process.
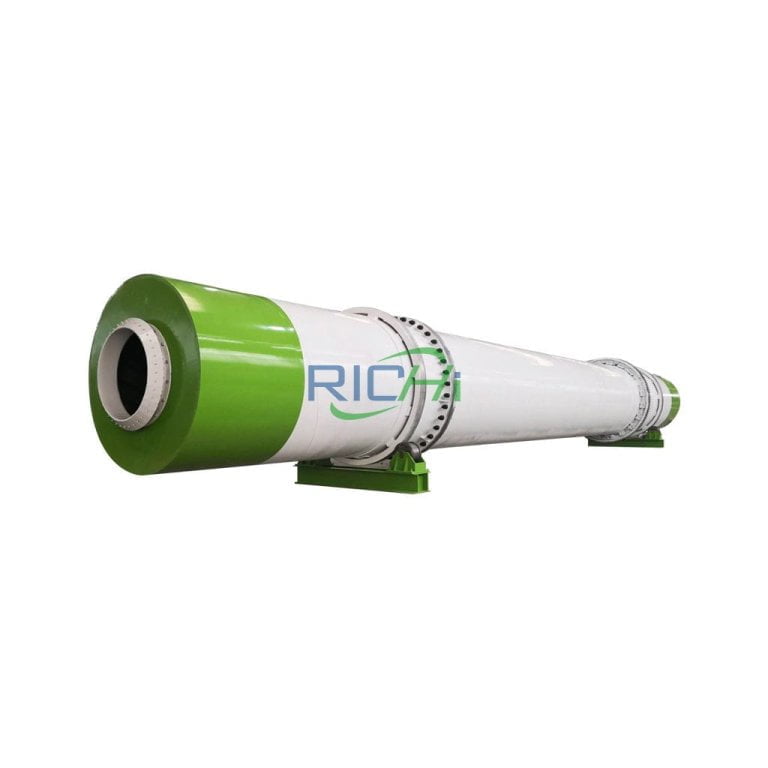
● Drying
fertilizer drying machine
Fertilizer dryer is a machine for drying pelleted fertilizer. It can not only dry fertilizer granular, but also can dry fresh animal waste, such as animal manure, video waste, sludge, etc.
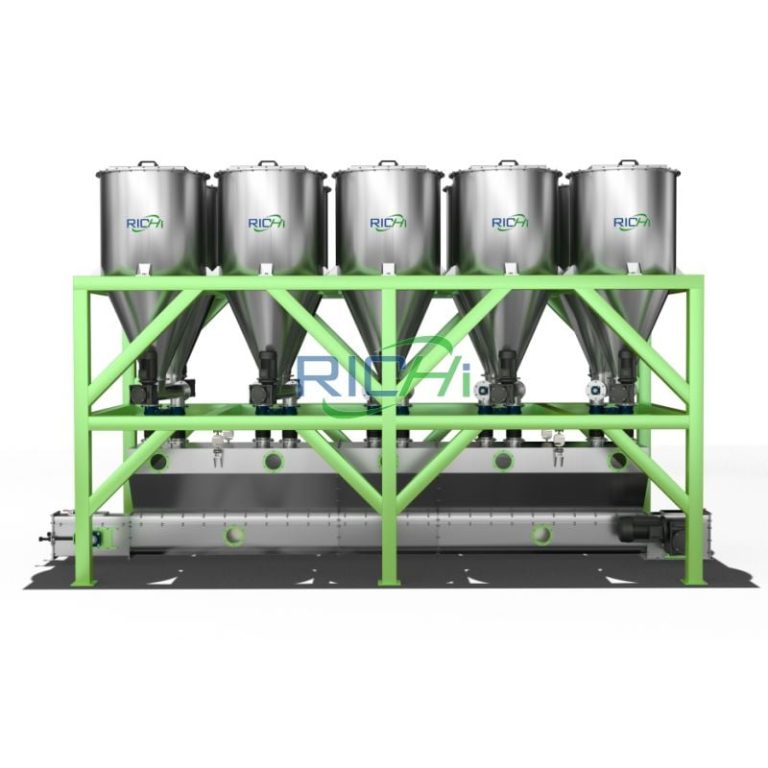
● Batching
fertilizer batching machine
Fertilizer batching equipment, can be used for fertilizer mixing. We provide mini, large, dynamic, static & mobile batching machine for manned fertilizer plant.
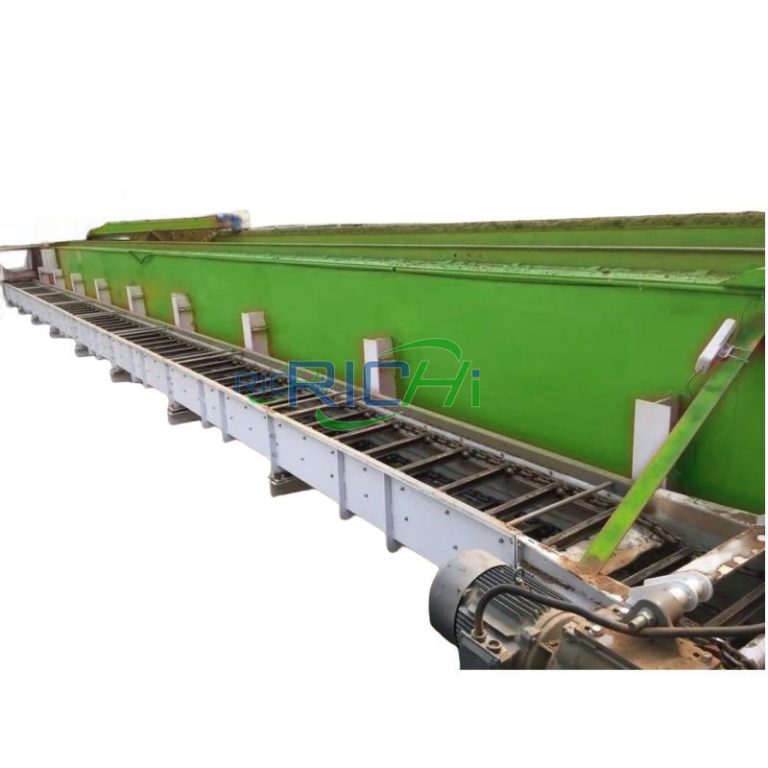
● Turning
manure compost turner
This compost turning machine is designed to tow behind a tractor and adopt a hydraulic control system. It lifts and tumble compost materials.
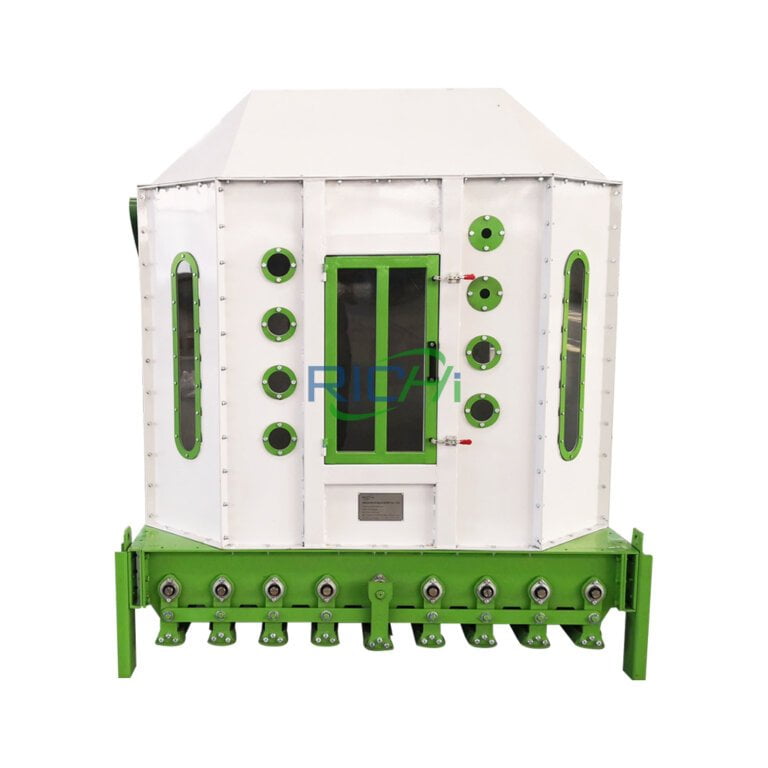
● Cooling
fertilizer cooling machine
Fertilizer pellet cooler is a machine for lowering temperature of granulated fertilizer pellets. It is important in both organic & compound fertilizers production process.
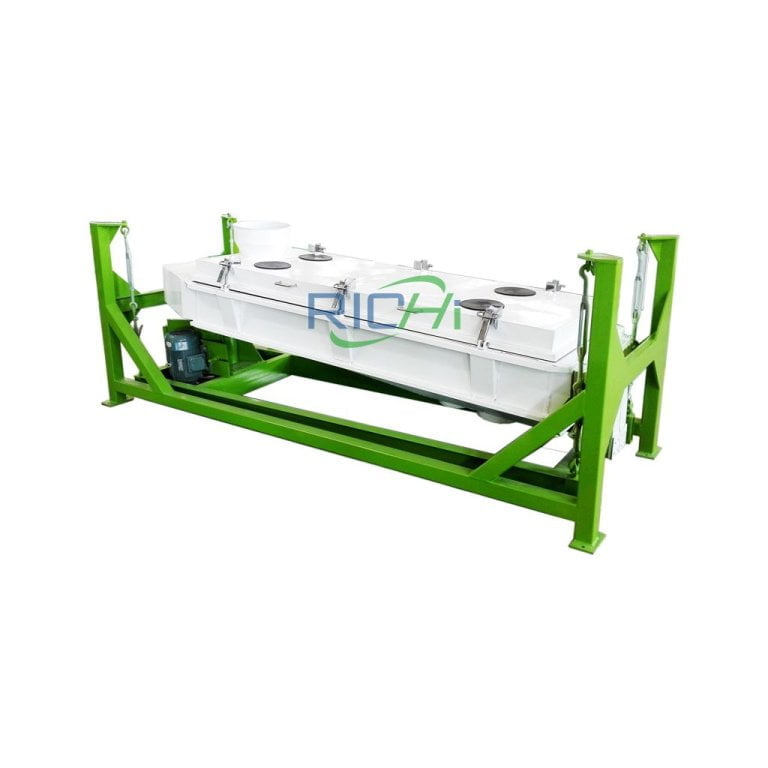
● Screening
fertilizer screener
For fertilizer production and the manufacture of fertilizer granulates, we produce high-performance fertilizer screening machines with very precise screening cuts.
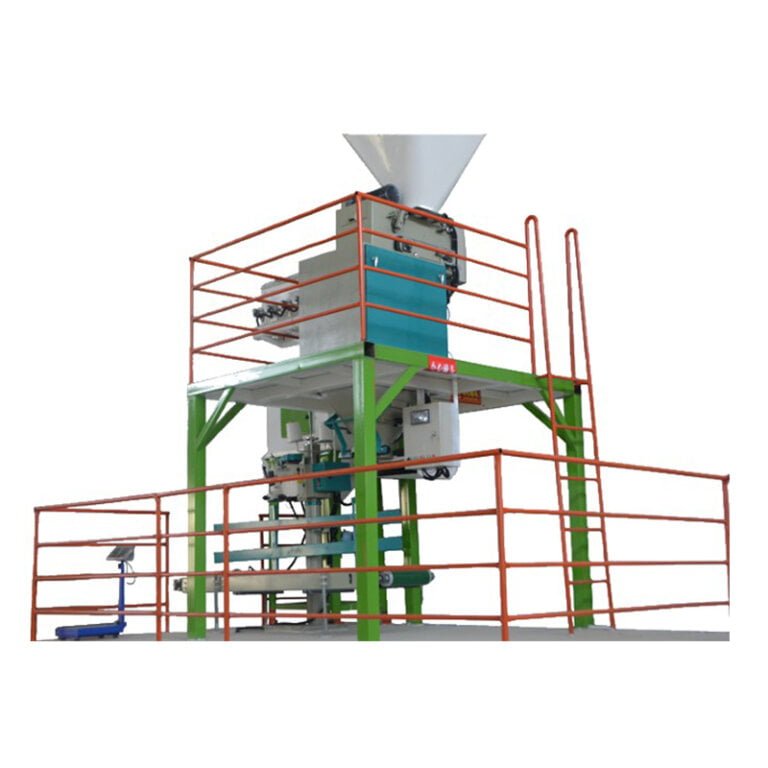
● Packaging
fertilizer bagging machine
RICHI provides fast and automated fertilizer bagging and palletizing machines for granular and powdered products. Easy to operate and maintain.
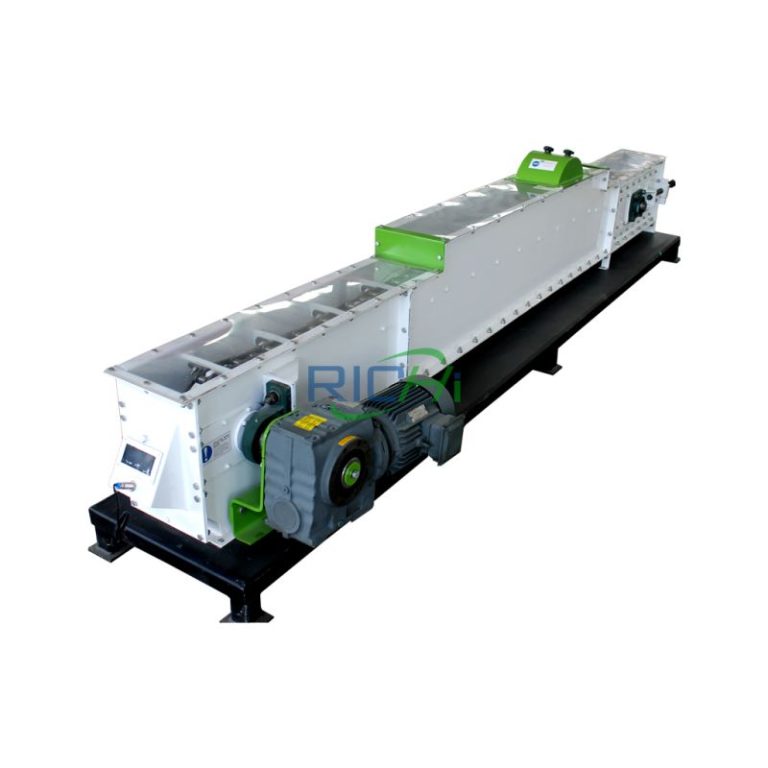
● Conveying
fertilizer conveyor
Our belt conveyors are available in 18”, 24”, 30 or 36” widths with custom to fit lengths. Custom designed to fit your building needs, and fertilizer production needs.
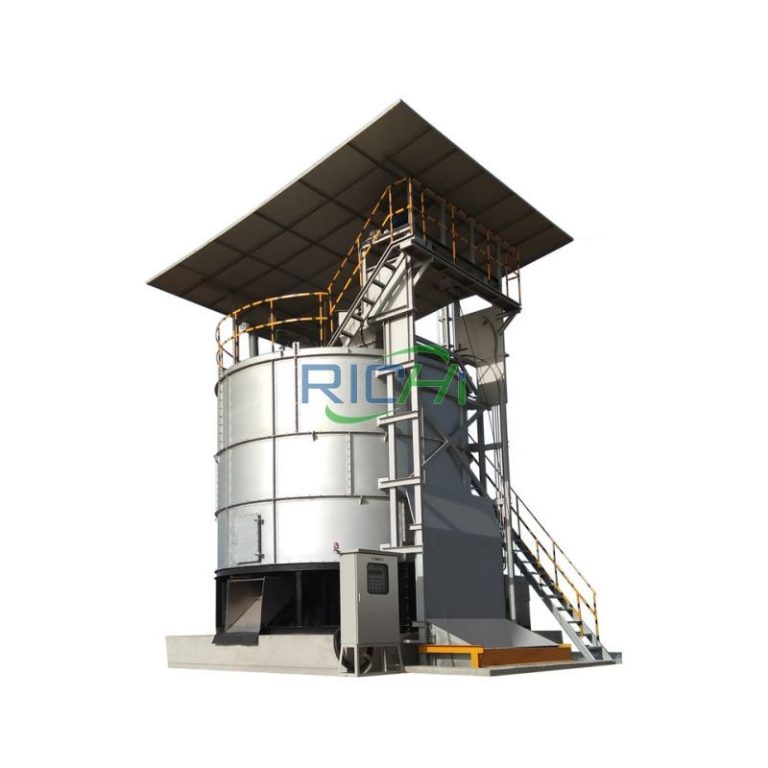
● Fermentation
Fermentation tank
Fermentation tanks are containers designed to support the fermentation process. They provide an optimized environment for microorganisms to thrive.
Frequently asked questions
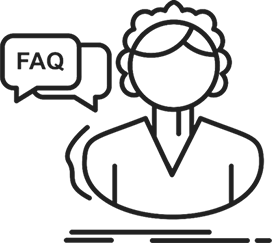
What are the main parts and structure of fertilizer mixing machine?
- Rotor and its transmission
The rotor is composed of ribbon spiral blades, shafts, rings and support rods. The blades are divided into inner and outer circles, which are left-handed and right-handed respectively.
When the rotor rotates, the left-handed blade pushes the material from one end to the other, and the right-handed blade moves the material in the opposite main direction. Through the convection of the two streams of materials and the turning of the materials sent to the two end side plates, the mixing purpose is achieved through repeated movements.
The outer blades of the rotor are equipped with adjustment plates, which can be adjusted in the direction of the axis. By adjusting the position of the adjustment plate, the amount of material pushed by the outer blades can be changed, so that the amount of material pushed by the inner and outer blades is equal.
At the left end of the rotor close to the inner wall of the mechanism, the outer blade support rods are equipped with adjustable scraper plates so that the materials in the four corners of the machine can be fully mixed.
The rotor shaft is driven by a sprocket, and the driving sprocket is decelerated by a cycloidal pinwheel reducer.
- Machine body
There are two inner and outer wall panels at both ends of the machine body. The space between the inner and outer wall panels is connected to the upper and lower parts of the machine body. When feeding and discharging materials, the air discharged by the materials can circulate in this space without overflowing from the fertilizer mixing machine.
There are observation doors and two feed ports on the top cover of the machine body. The top cover of the mixer body is divided into three sections, one of which is an observation door for maintenance. The other two sections are large cover plates. When in use, holes can be opened to connect the feed pipe or pneumatic gates can be installed according to process requirements.
- Discharge control mechanism
The discharge control mechanism consists of a cylinder, a connecting rod mechanism, a linkage shaft, a travel switch, etc. The discharge door is installed on the linkage shaft, the linkage shaft and the driven rocker of the linkage mechanism are connected together, and the cylinder head and the active rocker are hinged.
The cylinder reciprocates, and the linkage shaft rotates through the linkage mechanism, thereby driving the discharge door to open or close (when the cylinder piston rod is pushed out, the discharge door is closed).
- Fixing of the main shaft bearing seat
Two pads are installed between the bottom surface of the main shaft bearing and the supporting surface on the machine body, and the contact surface between the two pads is an inclined surface. By moving the two pads, the height of the bearing seat can be adjusted, that is, the gap between the outer diameter of the rotor and the casing can be adjusted. The two ends of the bearing seat and the two pads below are tightened by bolts installed on the machine body.
- Liquid addition pipeline
The liquid addition pipeline is installed on the upper side of the machine body and consists of a pipeline, a nozzle, etc. The liquid is sprayed out in a fan shape through the nozzle, and the entire length of the casing has several nozzles evenly distributed. The inlet end of the pipeline is equipped with a flange, which is connected to the oil supply system.
What preparations need to be made before installing, adjusting and using a fertilizer mixing machine?
- A comprehensive safety inspection should be carried out before the equipment is installed.
- The machine has a large door for discharging, and the discharging connection port is the flange edge of the casing. A hopper of equivalent volume should be installed under the machine body.
The reduction motor is installed on the slide rail. The installation dimensions are shown in Figure 6. - Connect the feed pipe to the cover plate on the upper part of the machine body according to the process requirements.
- Install the transmission chain, adjust the position of the motor, make the chain transmission stable, and make the main shaft turn in the same direction as the arrow on the mixing casing, and then install the chain cover.
- Connection of the liquid addition system: The liquid addition pipeline is installed on the side of the machine, which consists of pipeline sprays, etc. The liquid is sprayed out in a fan-shaped mist through the nozzle, and there are 3-5 nozzles evenly distributed along the entire length of the pipeline in the machine.
- Before use, check the opening and closing of the discharging door, adjust the cylinder pressure and the stroke position, so that the discharging door can be level with the bottom of the casing when closed, and the opening can reach a certain angle, and the cylinder can run smoothly.
What should we pay attention to when using and operating a fertilizer mixing machine?
- Before use, the machine should be operated without load, and the operation should be smooth without abnormal vibration. The discharging mechanism should be observed to be tightly closed.
- When using, the reduction motor should be started first, and the material should be fed after the rotor rotates normally.
- The material surface in the machine body shall not be lower than the plane of the main shaft axis and higher than the diameter of the outer spiral belt.
- Additives should be added after half of the main material in the machine enters the batch, and grease should be sprayed after all the main material enters the machine. After spraying, it should be mixed for a period of time before discharging.
- Metal impurities should not be mixed in the material to avoid damage to the rotor blades.
- The use of reducers, cylinders, auxiliary parts, etc. should comply with the provisions of their instruction manuals.
- The working current of the mixer cannot exceed the rated current of the motor.
- When the machine is not in use, no grease should be left in the grease adding pipeline to avoid clogging the pipeline after the grease solidifies.
How to maintain the fertilizer mixing machine?
- The discharging mechanism should be kept flexible and dust should be removed regularly.
- The bearings should be lubricated regularly, and sodium-based grease should be used first.
- The transmission chain should be brushed with an appropriate amount of No. 30 mechanical oil and the chain should be cleaned regularly.
- Lubrication of the gear reducer motor.
(1) It is recommended to use No. 40-50 mechanical oil.
(2) After the first refueling, the oil should be replaced after 500 hours of operation. After that, the oil should be replaced every six months during continuous operation (8-hour working system). If the working time is extended, the oil change time can be shortened appropriately. - Faults and troubleshooting
(1) If a sudden shutdown occurs during use, the motor should be started after the discharging door is opened to discharge the material.
(2) If there is powder leakage from the discharging door, check the contact between the discharging door and the casing. If the discharging door is not tight or the sealing strip is aging, adjust the travel switch or the adjusting nut on the support arm or replace the sealing strip.
(3) If the discharging mechanism cannot operate normally, check whether there is any fault in the cylinder and air supply system.
How many materials can fertilizer mixing machine mix at the same time?
Fertilizer mixing machine is not limited to the type and quantity of materials, it is calculated by the capacity of each batch. So, you can choose the raw materials at will.
Do you provide installation drawings and instructions for the fertilizer mixer machine?
Of course, we will provide instructions for the installation and operation of the equipment. If there are any problems during the process, our engineers can provide corresponding technical support.
Do you have a running video of the fertilizer mixer?
Of course, based on our large number of project sites and production and trial machine experience, we have many running videos of mixers to share with you.
Do you provide trial machine services for fertilizer mixer machines?
Of course, before the equipment is shipped, customers can make an appointment for inspection and trial machine. You can also find a third party to be on site.
Why Choose RICHI fertilizer mixing equipment?
We Offer Equipment from Stock
Our 30,000 square meters facility houses a large on-site inventory of processing equipment for organic fertilizer and compound fertilizer industries.
Short Lead Times
Our expansive on-site inventory of new equipment is available for shipment to meet customer needs.
Experienced Work Force
Our sales staff has a combined 30 years of experience customizing mixer equipment for a variety of industry uses. Our highly skilled production staff and fabricators can manufacture equipment to customer specifications.
At RICHI Machinery, we specialize in manufacturing the best fertilizer mixing machines on the market, engineered to meet the demands of diverse industries. Whether you’re looking for horizontal mixers, vertical mixers, or other advanced mixers, RICHI offers top-tier solutions tailored to your needs. Our fertilizer mixing machines are designed with precision, performance, and durability in mind, ensuring they excel in every application.
ABOUT RICHI MACHINERY
RICHI MACHINERY has been an industry leader in the turnkey fertilizer processing equipment market for over two decades. Our expert product and engineering team offers quality mechanical and design services for all of our turnkey solutions. From single fertilizer making machine to full fertilizer production line installation, we deliver the quality and consistency that the world’s most advanced fertilizer industries demand.
- Expert fertilizer plant solutions backed by our ISO quality control system.
- Precision fertilizer equipment and fertilizer production plant installation capabilities.
- Turnkey fertilizer plant machinery manufacturing.
- Premium fertilizer equipment and fertilizer production line customization options including customization of different parts, combination of different equipment, durable paint, primer and powder coating options.

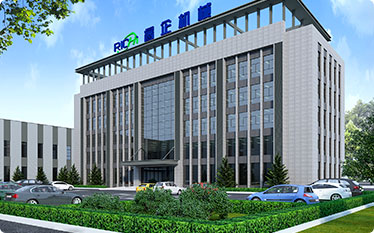
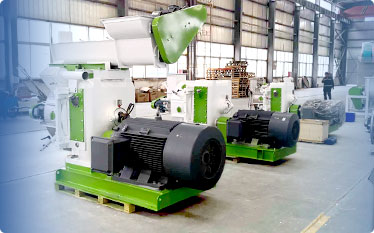
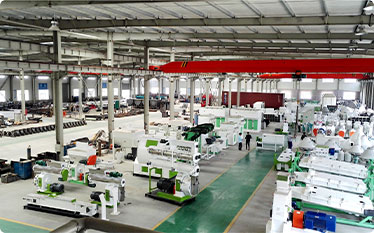
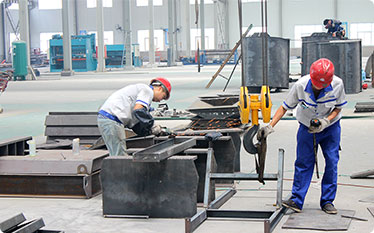