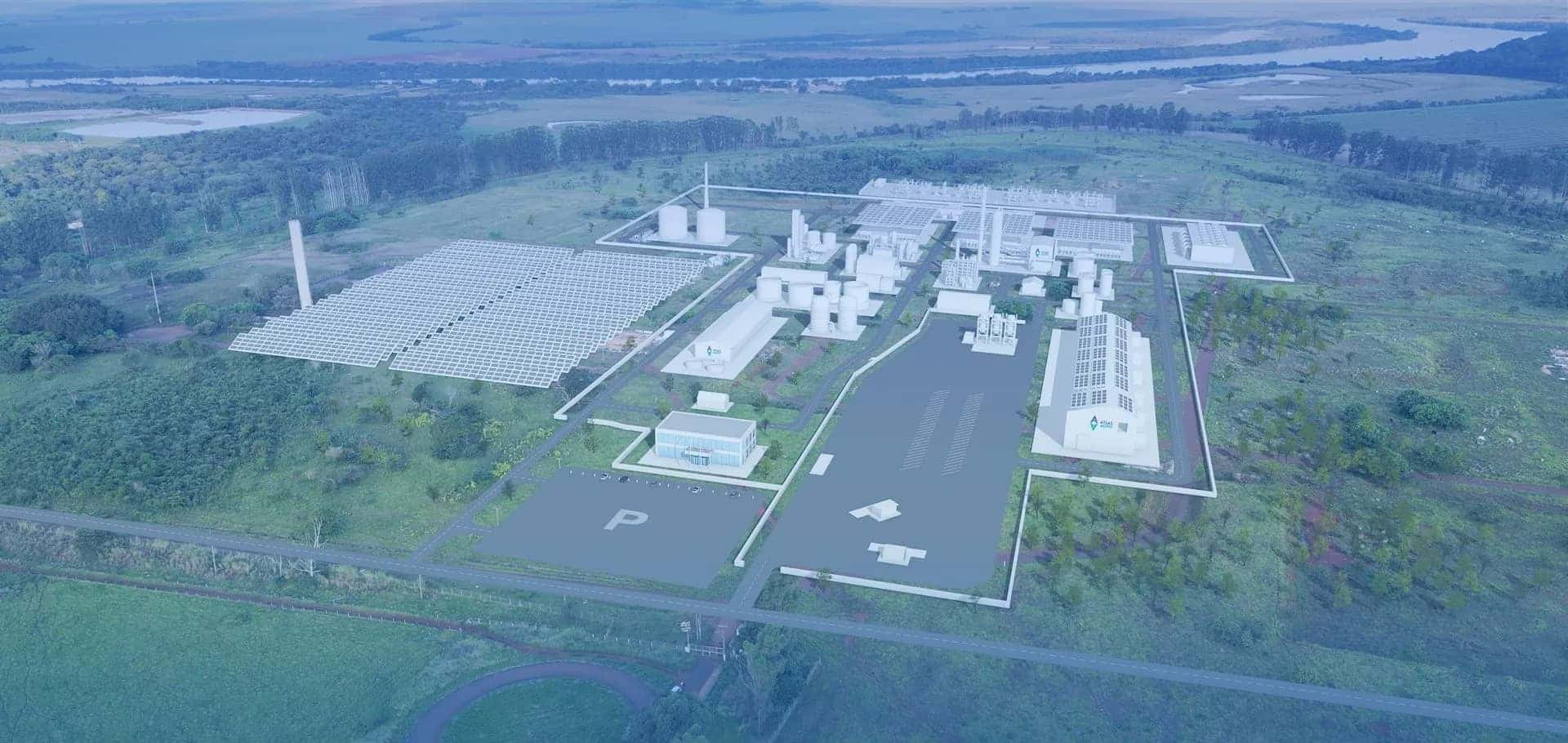
Compost Manufacturing Plant In Germany
installation country
Germany
Production Capacity
1-1.5T/H
Project Investment
$350,000
Product type
Granules
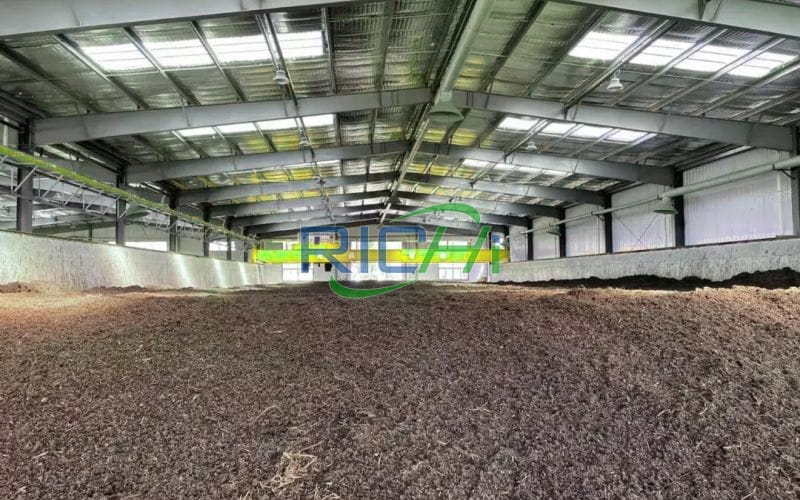
This project was invested and built by a German brewery.
The German government has always encouraged farmers to use organic fertilizers and reduce the use of chemical fertilizers through organic agriculture policies. It also provides financial subsidies and funding to support the production and application of organic fertilizers, especially the subsidies for organic agriculture.
In response to the German national policy, the project client built a “bio-organic fertilizer composting base project” with a total area of 9012 square meters and a construction area of 2401 square meters.
The compost manufacturing plant in Germany project uses poultry and livestock feces, food residues and sludge; brewery residues and filter mud; sludge and fermentation bacteria from domestic sewage treatment plants as raw and auxiliary materials, and produces 80 million tons of compost clinker and 2000 tons of organic fertilizer granules annually.
It is worth mentioning that although the project is mainly based on composting, the customer also purchased our FZLH250 organic fertilizer granulator equipment with an output of 1-1.5t/h. According to customer feedback, in the actual production process, granulation is currently only used as an experimental process. Therefore, the output of granulation is not included in the total output of the project.
RICHI MACHINERY
Construction Content
The main construction content of the project includes production greenhouses, drying yards, office buildings, etc., and the construction of corresponding supporting facilities for public works such as water supply and drainage. The project has a total of 20 employees, none of whom are boarded and lodged in the project, working 300 days a year and 8 hours a day.
The construction status of the compost manufacturing plant in Germany project is shown in the following table.
Item | Building name | Main engineering content | ||
Main engineering | Production greenhouse | There are 3 production greenhouses for composting fermentation | ||
Raw material yard shed, finished product warehouse | Warehouse, finished product warehouse | |||
Comprehensive building | Office | |||
Laboratory | Production and fermentation bacteria | |||
Public engineering | Power supply | Municipal power supply | ||
Water supply | Municipal water supply | |||
Drainage | After the domestic sewage is treated in a three-level septic tank to meet the standards, it will be reused for irrigation of the mountains and forests around the project and will not be discharged | |||
Environmental protection engineering | Noise control | Noise reduction, vibration reduction, workshop sound insulation and other measures | ||
Waste gas control | Production greenhouse | The stench generated by the fermentation and compost turning process is led to a unified set of biological filtration and purification equipment through a negative pressure fan for treatment, and then discharged through a 15m exhaust pipe; the dust generated by the enclosure, spraying of deodorants and screening in the granulation workshop is discharged in an unorganized manner after being treated with water spraying and dust reduction | ||
Raw material yard shed | ||||
Wastewater treatment | Domestic sewage | Domestic sewage is treated in a three-level septic tank to meet the standards and is reused for irrigation of the mountains and forests around the project, and is not discharged | ||
Initial rainwater | The production shed, raw material yard and warehouse of the project are all enclosed, and interception ditches are set around the buildings. The initial rainwater is discharged to the south pond after sedimentation in the interception ditch. | |||
Solid waste management | Unqualified organic fertilizer | Reused as raw materials for production | ||
Domestic waste | Collected and transported by the sanitation department |
RICHI MACHINERY
Main economic and technical indicators
The main economic and technical indicators of the compost manufacturing plant in Germany project are shown in the following table.
No. | Item | QTY |
1 | Total building area | 2401m2 |
2 | Total land area | 9012m2 |
Among them | Production shed | 2401m2 |
Raw material yard shed, finished product warehouse | 3611m2 |
RICHI MACHINERY
Product plan and product technical indicators
The product plan for this compost manufacturing plant in Germany project is as follows:
Product Name | Annual Output |
Compost Clinker | 80 million tons |
The compost clinker products of this project are bagged. After fermentation and dehydration, they are used for agricultural land and comply with the standard requirements of the German Agricultural Sludge Pollutant Control Standard. The requirements for each product index are shown in the table below.
Concentration limits of pollutants in sludge products:
Indicator classification | Pollutant limit | |
Appearance and smell | A-level (cultivated land, gardens, pastures) sludge products | B-level (gardens, pastures, cultivated land without edible crops) sludge products |
Moisture content/% | ≤60 | |
PH | 5.5~8.5 | |
Particle size/mm | ≤10 | |
Organic matter (on a dry basis)/% | ≥20 | |
Ascaris egg mortality/% | ≥95 | |
Fecal coliform bacteria value | ≥0.01 | |
Total cadmium (on dry basis) (mg/kg) | <3 | <15 |
Total mercury (on dry basis) (mg/kg) | <3 | <15 |
Total lead (on dry basis) (mg/kg) | <300 | <1000 |
Total chromium (on dry basis) (mg/kg) | <500 | <1000 |
Total arsenic (on dry basis) (mg/kg) | <30 | <75 |
Total nickel (on dry basis) (mg/kg g) | <100 | <200 |
Total zinc (on dry basis) (mg/kg) | <1200 | <3000 |
Total copper (on dry basis) (mg/kg) | <500 | <1500 |
Ore Oil (on dry basis) (mg/kg) | <500 | <3000 |
Benzo(a)pyrene (on dry basis) (mg/kg) | <2 | <3 |
Polycyclic aromatic hydrocarbons (on dry basis) (mg/kg) | <5 | <6 |
RICHI MACHINERY
Main raw and auxiliary materials and annual usage
The main raw and auxiliary materials and annual usage used in this compost manufacturing plant in Germany project are shown in the following table:
No. | Raw and auxiliary material name | Annual usage | Remarks |
1 | Livestock excrement | 1.3 million t/a | Main material, purchased from outside, moisture content is about 30% |
2 | Food residues and biogas residue | 35 10,000 t/a | as the main material, purchased from outside, with a moisture content of about 54% |
3 | Brewery residue and filter mud | 335,000 t/a | as the main material, purchased from outside, with a moisture content of about 54% |
4 | Sludge from domestic sewage treatment plants | 15,000 t/a | is an auxiliary material, purchased externally. The collection, transportation, storage, treatment and disposal of the sludge from the domestic sewage treatment plant involved in the project shall comply with local regulations |
5 | Fermentation bacteria | 10t/a | laboratory culture |
6 | Deodorant | 150t/a | purchased externally |
7 | Packaging bags | 50,000 pieces/a | purchased externally |
RICHI MACHINERY
Raw material composition and test results
The raw materials of this compost manufacturing plant in Germany project are poultry and livestock feces, food residues and biogas residues; brewery residues and filter mud; domestic sewage treatment plant sludge and fermentation bacteria, which are general solid wastes. The test results of the composition of the project sludge raw materials (food residues and biogas residues; brewery residues and filter mud; domestic sewage treatment plant sludge, etc.) are detailed in the table below.
No. | Content of sludge raw materials | Maximum allowable content (based on dry sludge) (mg/kg) | ||
Item | (mg/kg) | |||
1 | Total cadmium | <2.5 | 5 | Acidic soil (PH<6.5) |
2 | Total mercury | 2 | 5 | |
3 | Total lead | 48.3 | 300 | |
4 | Total chromium | 55 | 600 | |
5 | Total arsenic | 9.5< /td> | 75 | |
6 | Total Nickel | 16.8 | 100 | |
7 | Total Zinc | 144 | 2000 | |
8 | Total Copper | 71.3 | 800 | |
9 | Boron | 6.18 | 150 | |
10 | Mineral oil | 0.23 | 3000 | |
11 | Benzopyrene | 0.28 | 3 | |
12 | pH | 3.75 | / | |
13 | Exchangeable calcium | 6.01cmol (1/2Ca+)/kg | / | |
14 | Sulfide | 2.25 | / | |
15 | Chloride ion | 0. 184g/kg | / | |
16 | Water content | 54.00% | / | |
17 | Organic matter | 39. 12 | / |
From the above data, it can be seen that the sludge components used in this project meet the requirements of the German “Pollutant Emission Standards for Urban Sewage Treatment Plants”.
According to local regulations, all types of sludge raw materials transported by this project must be tested for composition before entering the factory, and each sludge component should meet the requirements of the local urban sewage treatment plant pollutant emission standards.
RICHI MACHINERY
Main compost fertilizer making machines list
The main fertilizer making machines used in this compost manufacturing plant in Germany project are shown in the following table.
No. | Equipment Name | Specification Model | QTY | Purpose |
1 | Strip Composting Tank | 1×2×50 | 10 | Fermentation, dehydration, ripening |
2 | Solar Drying Shed Iron Frame Structure | / | 1 | Material Piling and Dehydration |
3 | Ventilation system | QSR100 | 1 | High temperature dehydration and fermentation of raw materials |
4 | Deodorization and environmental protection equipment | / | 1 | Fermentation and deodorization |
5 | Vertical fertilizer crusher machine | LP30 | 1 | Crushed materials |
6 | Quantitative packaging scale | LCS-BZY | 1 | Automatic measurement and packaging |
7 | Forklift | PW50 | 2 | Raw material proportioning and turning |
8 | Turning machine | XGFD2600 | 1 | Raw material dehydration, Aerobic fermentation |
9 | Forklift | 3T | 2 | Finished product stacking, loading and unloading |
10 | fertilizer Dryer | / | 1 | Drying |
11 | Reservoir | / | 2000 | Collect sewage to prevent leakage and environmental pollution |
12 | organic fertilizer granulator machine | FZLH250 | 1 | Process the fermented materials into granules |
RICHI MACHINERY
Water supply and drainage system
Water supply
The water used in this compost manufacturing plant in Germany project mainly comes from municipal water supply. The water used in the project is mainly for the living of employees. There are 20 employees in this project, none of whom eat or stay in the factory and work 300 days a year. The water consumption of employees is calculated as 155L/person/day, and the living water consumption is 3.1m3/d (930m3/a).
Drainage
The project adopts a rainwater and sewage diversion system, and the project wastewater mainly comes from domestic sewage. The project sets up a reuse water tank at the outlet of the septic tank wastewater, and collects the wastewater treated by the tertiary septic tank into the reuse water tank.
The treated wastewater is used for irrigation of the surrounding mountains and forests. The reuse water tank is connected to the mountain and forest water supply with a thin hard PVC pipe, and the necessary switches are set. When irrigation is needed, just turn on the switch. Therefore, after the domestic sewage of the project is treated in the tertiary septic tank to meet the standards of the “Agricultural Irrigation Water Quality Standard”, it is reused for irrigation of the surrounding mountains and forests of the project and is not discharged.
The initial rainfall of the project is 4210m3/a. The production greenhouse, raw material yard and warehouse of the project are all enclosed. There are interception ditches around the buildings. The initial rainwater is discharged to the south pond after sedimentation through the interception ditch.
Power supply system
The power supply of the compost manufacturing plant in Germany project is supplied by the municipal power grid, with an annual power consumption of 800,000 kWh. No boilers or generators are installed.
RICHI MACHINERY
Composting process design
Based on the raw material and process requirements of the customer, we designed the composting process and organic fertilizer production process for the customer as follows:
(1) Yard
Sludge raw materials (food residues and sludge; brewery residues and filter mud; sludge from domestic sewage treatment plants, etc., with a moisture content of 54%) are transported into the factory area by closed dump trucks and directly unloaded into the environmental protection greenhouse. The environmental protection greenhouse is equipped with a sun roof and cofferdams around it.
Deodorant is added to the sludge raw materials when they enter the factory, and the moisture content is reduced to 30%-40% after natural drying for 4-5 days (adjusted according to weather conditions). The moisture content of livestock and poultry manure is about 30% when it enters the factory, and no drying is required. The storage yard is set up in a light-transmitting shed and surrounded on all sides, so no dust is generated. The sludge raw materials are exposed to sunlight to remove moisture, and the exposure process will produce odor.
(2) Fermentation
The composting fermentation of this project adopts the “aerobic composting fermentation” method. The complete composting process consists of four stages: low temperature, medium temperature, high temperature and cooling. The composting temperature is generally 50~60℃, and can reach up to 70~80℃. The composting process mainly includes two fermentation processes: primary fermentation and post-fermentation.
① Primary fermentation
The main fermentation of this compost manufacturing plant in Germany project is carried out in the production shed, and the mixed materials are evenly spread in the workshop. In the initial stage of composting, for 1-3 days, since the oxygen-containing materials can meet the needs of microorganisms, aerobic microorganisms first decompose perishable materials, and then absorb the carbon/nitrogen nutrients of the decomposed organic matter. Some nutrients are used for bacterial reproduction, and the remaining nutrients are decomposed into carbon dioxide and water, while releasing heat to increase the temperature of the pile.
When the temperature is 25-45℃, mesophilic microorganisms are relatively active; as the temperature of the pile continues to rise, when the temperature is 45-65℃, thermophilic microorganisms such as thermophiles and actinomycetes gradually dominate, are decomposed, and humus begins to form.
Practice has proved that when the composting temperature is above 60℃ for three days, parasite eggs and pathogens in the material can be killed, achieving the purpose of harmless composting. The process of gradually increasing the temperature from low temperature to high temperature is the process of harmless composting.
When the compost is maintained at high temperature (45~65℃) for 10 days, pathogens, eggs, etc. are all killed. The main fermentation process (including compost turning) of this fertilizer plant project takes 15-20 days. After the main fermentation, the moisture content of the material drops to about 32%.
② Compost turning
When the compost temperature rises to above 60℃, keep it for 48 hours before turning the compost (but when the temperature exceeds 70℃, the compost must be turned immediately. The compost temperature should not exceed 70℃, otherwise it will cause the beneficial microorganisms to dormant or even die).
When turning the compost, be sure to turn the compost evenly and thoroughly, and turn the lower layer materials into the upper part of the compost as much as possible for full decomposition. The number of turnings depends on the composting process.
Generally, the compost can be turned once every 2-5 days to provide oxygen, dissipate heat and make the materials ferment evenly. This compost manufacturing plant in Germany project uses a compost turning machine to turn the compost. If the material is found to be too dry during fermentation, water should be sprayed in time when turning the compost to ensure smooth fermentation. The oxygen content of the pile weight is maintained between 5-15%. The oxygen content is expressed as ventilation volume.
③ Post-fermentation
Based on fermentation, as the temperature of the compost drops, the mesophilic microorganisms begin to become active again, and the compost enters the second fermentation. This period can be called the post-fermentation or aging stage. This is conducive to the decomposition of organic matter that is difficult to decompose into relatively stable organic matter such as humus and amino acids, which greatly improves the fertilizer efficiency. With the help of turning the pile, it can generally be decomposed in 15-20 days.
The characteristics of mature organic compost are: the temperature of the compost naturally drops in the later stage, it no longer attracts flies, there is no odor, the texture is soft, the volume is reduced, it is dark brown or black brown, and the eggs are dead; taking fecal coliform group as the evaluation index, the possibility of the presence of pathogens is also very small when the fecal coliform value is 0.1-0.01; the moisture content of the mature organic fertilizer is less than 30%, and the post-fermentation process is carried out in the workshop.
(3) Granulation and screening
The mature fertilizer will be granulated by compost pellet making machine and screened by fertilizer screening machine; the unqualified fertilizer after screening will be collected and re-entered the granulation process.
(4) Drying
The finished pellets are dried in a chicken manure drying machine, and then put into storage, packaged and sold after being sampled and qualified.
RICHI MACHINERY
Analysis of rationality of fertilizer plant layout
The wind direction in the area where the compost manufacturing plant in Germany project is located is northerly all year round. Green belts are set up around the project, and the living and office areas are all in the upwind direction.
The raw material yard and production greenhouse of this project are fully enclosed, and the raw materials entering the project are sprayed with deodorants to suppress the amount of odor generated by the project. At the same time, the odor generated by fermentation and turning the pile is led to a set of biological filtration and purification equipment through a negative pressure fan for treatment and deodorization, and then discharged through a 15m exhaust pipe.
A large area of greening is planned to be planted at the boundary of the project to beautify the environment, and at the same time, it can absorb odors, thereby reducing the impact of odors on the surrounding environment. After taking the above measures, the odor generated during the project operation period has little impact on the living and office rooms in the factory area.
The project area is compactly arranged, from the entry and exit, storage of raw materials and various auxiliary materials, the flow of semi-finished products in each process to the storage and delivery of products, so that the semi-finished products at each stage can be circulated in sequence, and it is convenient for the company to reasonably use land resources in the future development.
At the same time, according to relevant design specifications, the fire protection level is determined and fire passages are set. From the perspective of environmental protection, the overall layout of the plant area of the project is very reasonable.
RICHI MACHINERY
What is the prospect of building composting and organic fertilizer production lines in Germany?
There is a very good prospect for building composting and organic fertilizer and compost manufacturing plant in Germany. The main reasons include Germany’s emphasis on environmental protection and sustainable development, the rapid development of organic agriculture, and the government’s policy support for waste management and circular economy. The following is a detailed analysis of this prospect:
German agriculture and environmental protection background
Germany is one of the largest economies in Europe, with developed agriculture, especially animal husbandry and planting, which are large in scale, generating a large amount of agricultural waste (such as livestock and poultry manure, crop residues).
The German government attaches great importance to environmental protection and sustainable development, and is committed to reducing greenhouse gas emissions, promoting circular economy and organic agriculture.
The production of compost and organic fertilizer is in line with Germany’s environmental protection policy, can effectively treat agricultural waste, reduce environmental pollution, and provide a sustainable source of fertilizer for agriculture.
Market demand
- Growth of organic agriculture: Germany is one of the largest organic food markets in Europe, the area of organic agriculture is increasing year by year, and the demand for organic fertilizer continues to grow.
- Consumer preference: German consumers have a high acceptance of organic food, which has promoted the development of organic agriculture, and in turn driven the demand for organic fertilizer.
- Waste management needs: Germany’s strict environmental regulations require farms and food processing companies to properly handle organic waste. Composting and organic fertilizer production are effective ways to solve this problem.
Policy support
EU Common Agricultural Policy (CAP): As a member of the European Union, Germany benefits from the EU’s financial support for organic agriculture and environmental protection projects.
German national policy:
- Circular Economy Law: Encourage the resource utilization of waste. Composting and organic fertilizer production are important components of the circular economy.
- Climate Protection Plan: The German government has set strict emission reduction targets. Composting and organic fertilizer production can reduce greenhouse gases such as methane produced during the decomposition of organic waste.
- Organic agriculture subsidies: The government provides subsidies for organic agriculture to encourage farmers to use organic fertilizers.
- Waste management regulations: Germany has strict regulations on the treatment of agricultural waste. Composting and organic fertilizer production are environmentally friendly solutions that comply with regulations.
Technology and production feasibility
- Mature composting and organic fertilizer production technology: Germany is a world leader in environmental protection technology and agricultural technology, and composting and organic fertilizer production technology is very mature.
- Automation and intelligence: Germany has a strong industrial base, and production lines can be highly automated and intelligent to improve production efficiency.
- Utilization of by-products: By-products (such as biogas) generated during the production of compost and organic fertilizers can be further utilized to improve economic benefits.
Competition and challenges
- Market competition: Although the German organic fertilizer market has grown rapidly, some local and international companies have entered, and competition may intensify.
- Initial investment cost: The construction of organic fertilizer and compost manufacturing plant in Germany requires a certain amount of capital investment, including equipment procurement, technology introduction and factory construction.
- Stability of raw material supply: The stable operation of the production line depends on the continuous supply of agricultural waste, and it is necessary to establish long-term cooperative relationships with farms, food processing companies, etc.
- Strict environmental protection requirements: Germany has extremely high environmental protection requirements, and organic fertilizer production plants need to comply with relevant emission standards and waste treatment regulations.
Economic benefits
- Cost and benefits: Agricultural waste has a low cost as a raw material, while compost and organic fertilizer are sold at a high price, especially in areas where organic agriculture is developed, with a large profit margin.
- Stable market demand: With the promotion of organic agriculture, the market demand for compost and organic fertilizer will continue to grow.
- Export potential: German compost and organic fertilizer can not only meet local demand, but also be exported to other EU countries.
Development suggestions
- Market research: Before investing, it is necessary to conduct a detailed research on the compost and organic fertilizer market in each state of Germany to understand demand, competition and policy support.
- Cooperation model: Cooperate with local farms, food processing companies or waste management companies to ensure raw material supply and sales channels.
- Environmental protection technology: Use advanced environmental protection technology to ensure that the production line complies with German environmental protection regulations.
- Brand building: Improve the market competitiveness of products through certification (such as organic certification) and brand promotion.
There is a very good prospect for building organic fertilizer and compost manufacturing plant in Germany, especially driven by environmental protection policies, organic agriculture and circular economy, market demand will continue to grow.
However, investors need to fully consider challenges such as market competition, initial investment and environmental protection requirements, and formulate a reasonable business plan to ensure the successful operation of the project. By leveraging Germany’s technological advantages and policy support, compost and organic fertilizer production lines are expected to become an investment project with both economic and environmental benefits.
If you are interested in building a compost manufacturing plant in Germany project, feel free to contact RICHI Machinery for technical support on organic fertilizer processing plant design, equipment configuration, production line layout, civil engineering solutions, etc.!