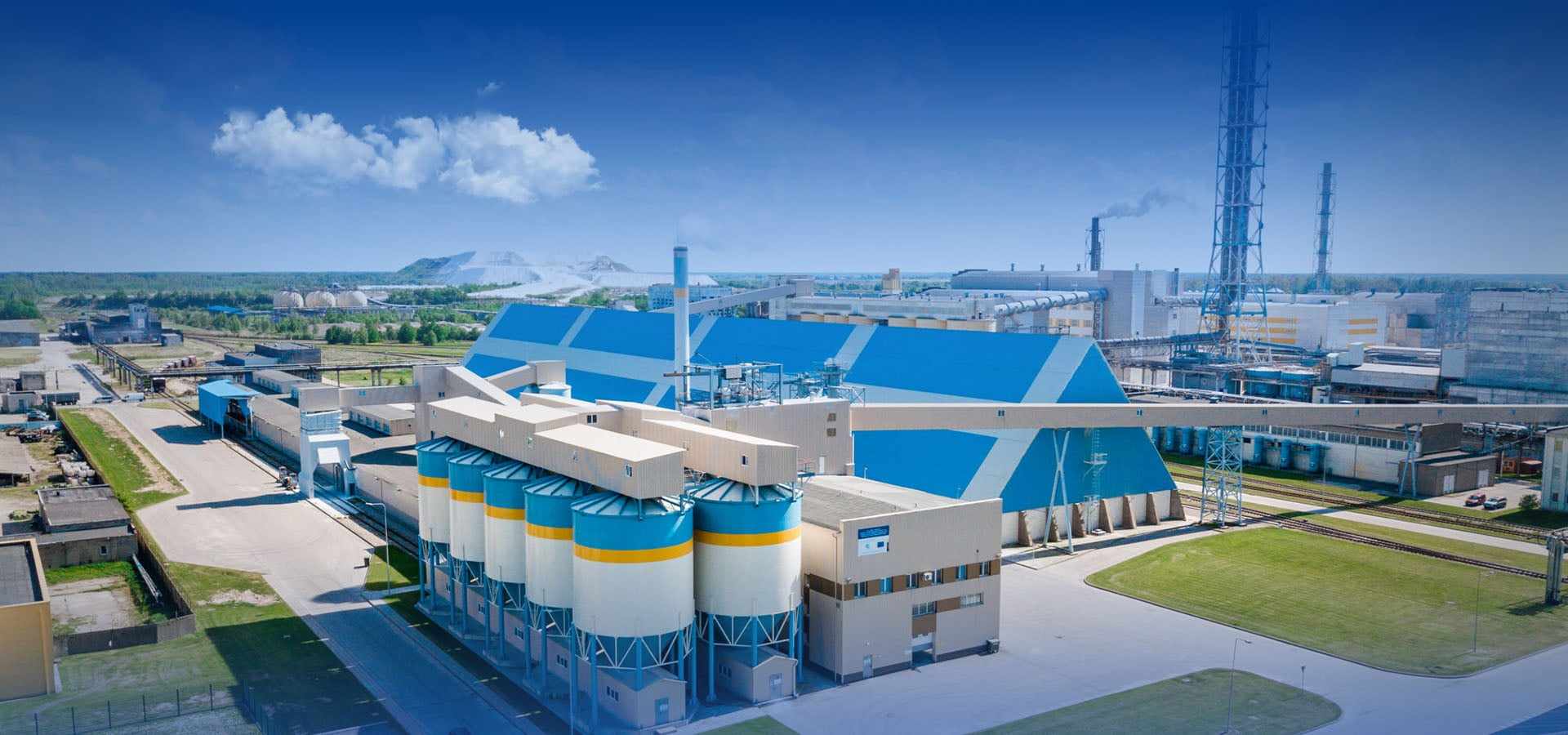
Efficiency, innovation, reliability
Organic Fertilizer Production Plant
Organic fertilizer production plant represent production specific and flexible solutions that cover the entire process from feeding to packaging. It refers to a production line that converts organic waste into organic fertilizer through a series of mechanical equipment and process flows. This production line mainly uses organic waste such as livestock and poultry manure, plant straw, and urban garbage as raw materials, and converts them into organic fertilizers rich in nutrients through biological fermentation technology.
Organic fertilizer production plant solution
— Richi Machinery —
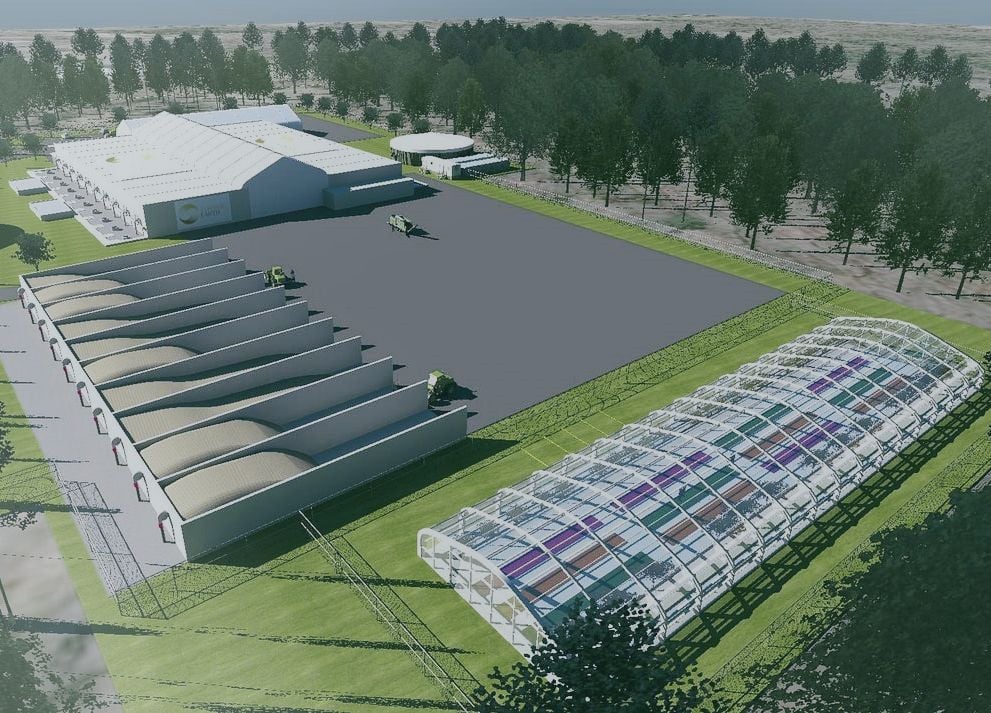
The organic fertilizer production plant covers a complete set of organic fertilizer processing systems, starting from livestock and poultry manure raw materials, through the accumulation and fermentation of agricultural and forestry waste, food waste and other accessories, until the production of organic fertilizer.
This production line not only includes various links of fertilizer production such as manure fermentation, raw material mixing, granule processing, drying and packaging, but also involves many process flows such as fermentation equipment, granulation equipment, crushing equipment, mixing equipment, screening equipment, cooling equipment, drying equipment, coating equipment and automatic packaging equipment.
There are many types of organic fertilizers, including granular and powder fertilizers, as well as pure organic fertilizers, bio-organic fertilizers and organic-inorganic compound fertilizers.
From Single Fertilizer Production Machines to Complete Organic Fertilizer Production Plants. And Everything In-Between. RICHI Machinery designs and builds entire organic fertilizer production lines, custom production cells, and individual equipment for many segments of the fertilizer industry.
Customers who are suitable for investing in organic fertilizer production lines include: livestock and poultry farms, agricultural companies, food companies, environmental protection companies, waste recycling companies, breweries and all other places that generate organic waste.
1-60 T/H
Production capacity
Powder & granules
Product Type
Advantages of organic fertilizer production line
Our organic fertilizer production line adopts high-temperature aerobic fermentation technology, covering multiple links such as moisture regulation, carbon-nitrogen ratio adjustment, temperature control, pH value regulation, ventilation treatment and strain application, aiming to create high-quality organic fertilizer. The organic fertilizer production line constructed by RICHI Machineryhas the following advantages:
Adaptability:
Organic fertilizer processing line has a wide range of applicability and can process a variety of organic wastes, such as livestock and poultry manure, agricultural and forestry waste, sludge, waste organic matter, etc.
Customization:
Organic fertilizer production lines can be customized and modified according to different needs, plant structures, raw material types, product types, and process requirements to meet the personalized needs of different customers.
High efficiency:
The organic fertilizer production line adopts efficient mixing, crushing, granulation, drying, fermentation and other processes, which can convert organic waste into high-quality organic fertilizer in a short time and improve production efficiency. Ensure that the quality of the organic fertilizer produced is stable and the quality is guaranteed.
Reduce costs:
The use of organic fertilizer production lines can convert organic waste into organic fertilizers and reduce the cost of fertilizer purchases. At the same time, due to the high production efficiency of this equipment, it can meet the needs of large-scale production and bring more benefits to farmers.
Environmental protection:
The organic fertilizer production plant uses microbial fermentation technology in the production process to convert organic waste into organic fertilizer, achieving the dual goals of effective resource utilization and environmental protection. At the same time, the equipment has low operating energy consumption and high energy-saving benefits.
Intelligent:
Modern organic fertilizer production plants have introduced advanced control systems and sensor technologies to achieve automated and intelligent production operations. Operators can monitor and manage the operation of the equipment through remote control or automated control systems to improve production efficiency.
● RICHI MACHINERY
Raw materials for organic fertilizer production
The raw materials of organic fertilizer are very extensive, mainly including livestock and poultry manure, animal processing waste, crop straw, kitchen waste, soybean meal, cottonseed meal and other oil crop residues, edible fungus residues, wine lees, garden waste (such as fallen leaves, pruned branches, etc.), vinegar lees, vegetable residues, cassava residues, sugar residues, paper mills, slaughterhouses, food processing plants and other organic waste.
When making organic fertilizer, it is usually selected and proportioned according to the characteristics, nutritional content and production needs of the raw materials. At the same time, in order to ensure the quality and safety of organic fertilizer, the pretreatment, fermentation and processing of raw materials are also very important.
It should be noted that some raw materials may contain harmful substances such as heavy metals and pathogens, so they need to be strictly tested and processed before use. From testing to production, professional equipment is required. For example, organic fertilizer mixer, granulator, organic fertilizer dryer, etc.
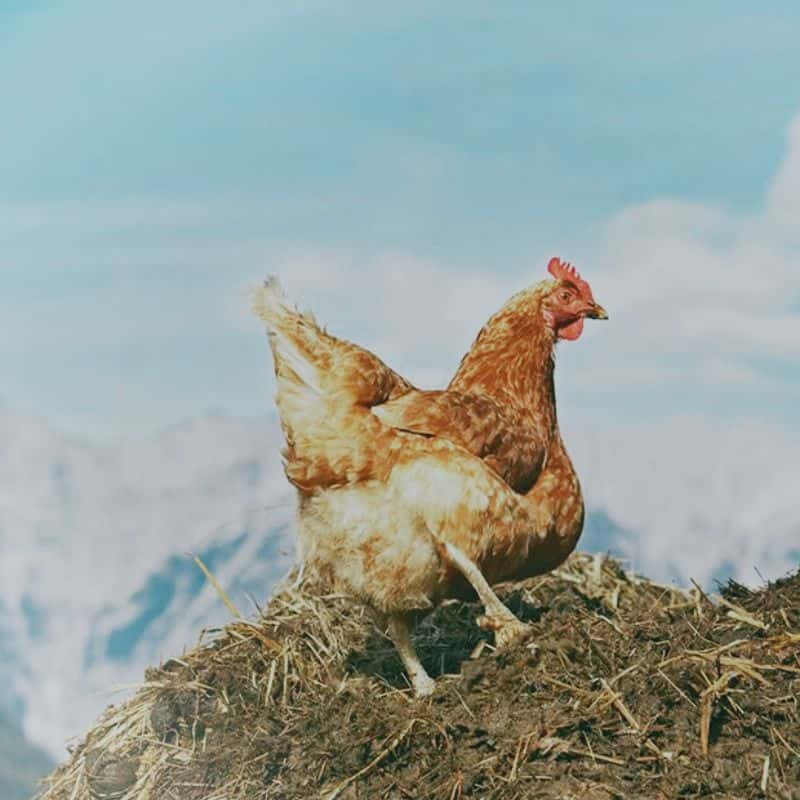
Livestock and poultry manure
Such as chicken manure, cow manure, sheep manure, pig manure, etc. These manures are rich in nutrients such as nitrogen, phosphorus, potassium, etc. There are also fish meal, bone meal, meat and bone meal, etc.
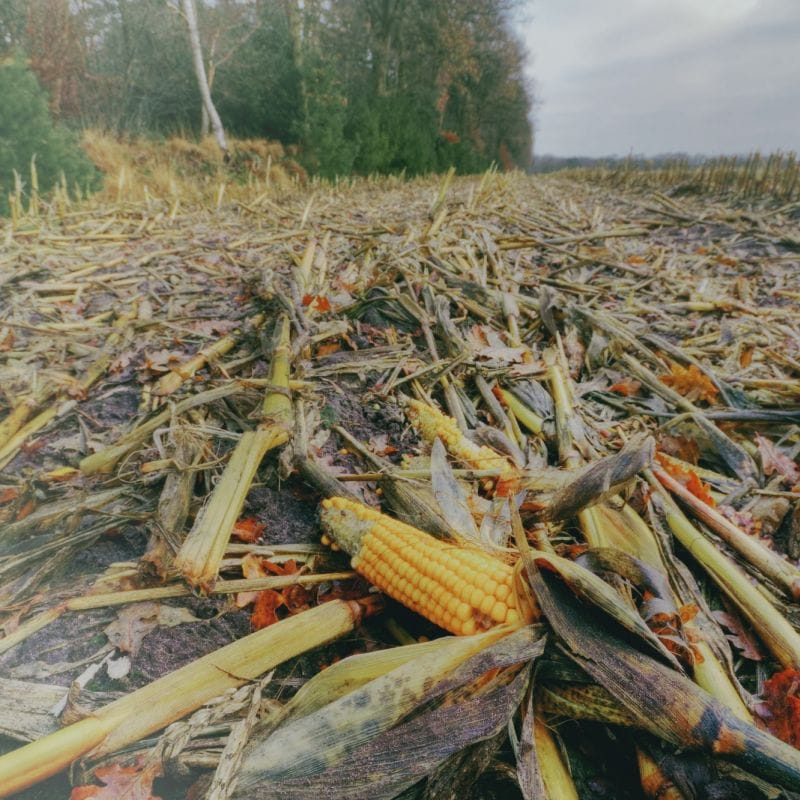
Agricultural and forestry waste
Such as rice straw, wheat straw, corn stalk, rice husk, bagasse, sawdust, peanut shells, coconut shells, banana peels, citrus peels, etc. These agricultural and forestry wastes can be converted into organic fertilizer after treatment.
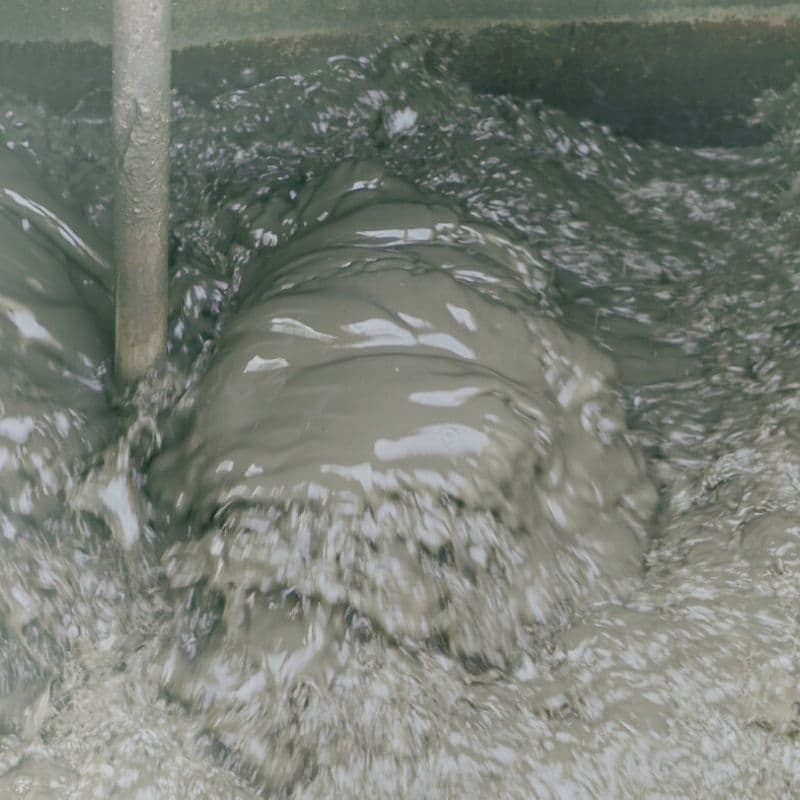
sludge
Sludge can be used as organic fertilizer raw material through composting, anaerobic digestion, thermal drying, etc. Sludge mainly comes from sewage treatment plants, water plants, and river and lake dredging.
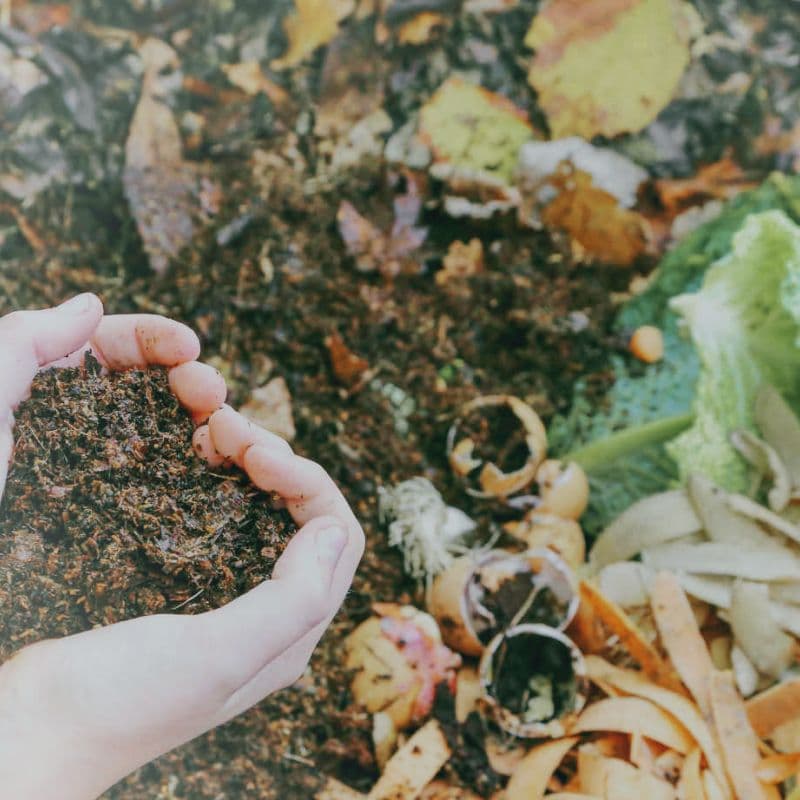
Food waste
Such as leftovers, fruit peels, etc., these wastes are rich in organic matter and can be converted into organic fertilizers after classification, treatment and fermentation.
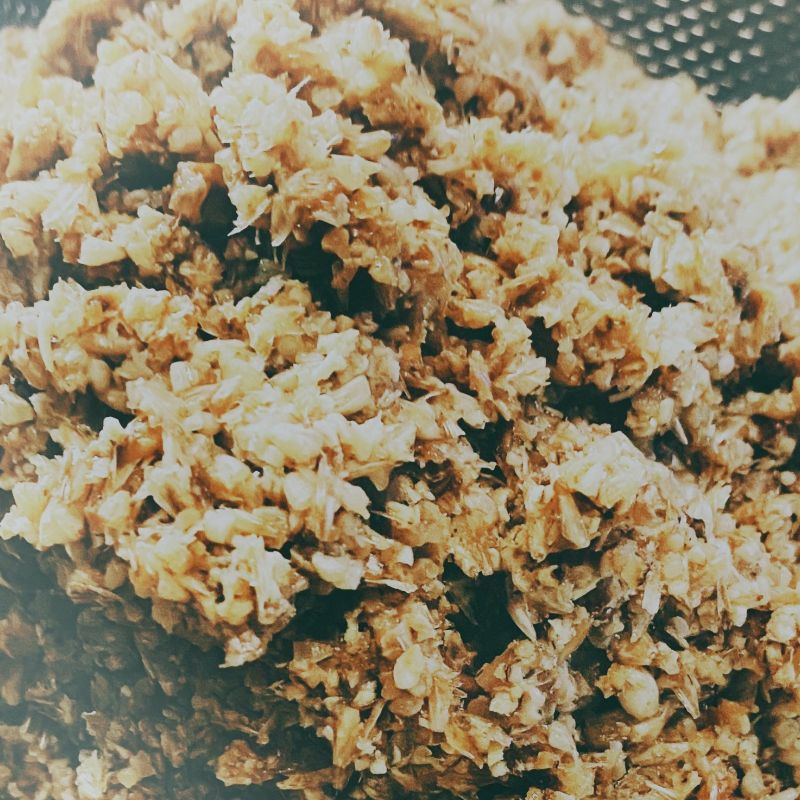
Industrial waste
Wine lees, vinegar lees, cassava slag, sugar slag, etc. These industrial by-products can be converted into organic fertilizers after treatment.
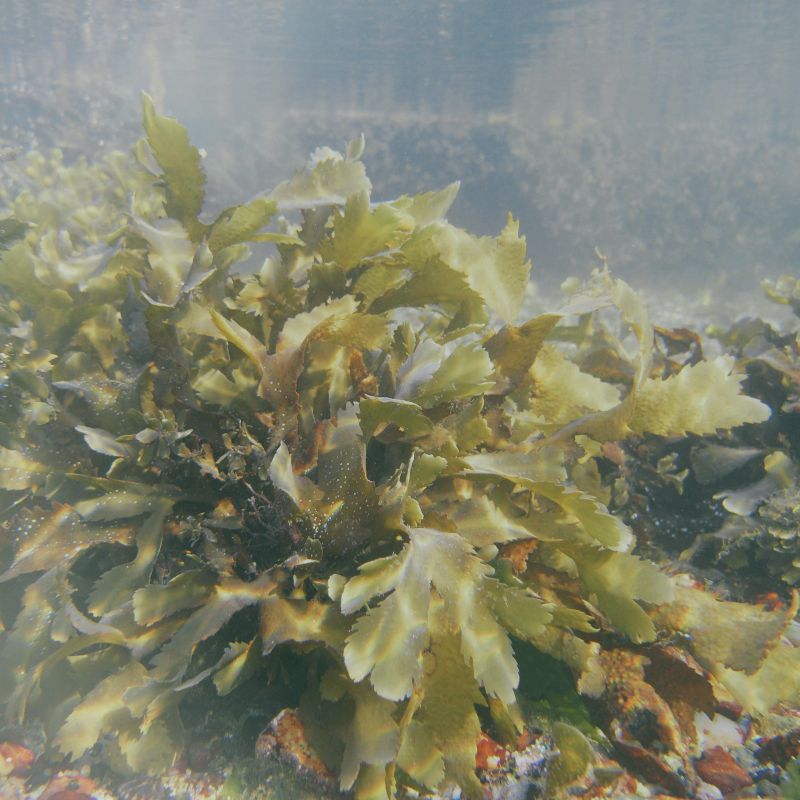
Other organic waste
Seaweed, peat, humic acid, earthworm castings, wood ash, bean dregs, fish meal, bone meal, these raw materials can also be used as raw materials for processing organic fertilizers.
organic fertilizer manufacturing process
Organic fertilizer production plant covers multiple links, such as fermentation, granulation, crushing, mixing, screening, cooling, drying, coating and automatic packaging.
Organic fertilizer production lines can be configured in a variety of ways according to process requirements, plant conditions and financial conditions.
Some customers require a standard and complete organic fertilizer process solution, some customers only require composting and fermentation technology, and some customers require crushing and mixing technology… According to customer needs, our organic fertilizer processing technology and equipment can be flexibly adjusted.
Raw material collection and classification
Collect organic raw materials such as livestock and poultry manure, straw, kitchen waste, etc. Classify and screen to remove non-organic impurities such as plastic and metal.
Raw material crushing and mixing
Crush large pieces of raw materials (such as straw) into small particles. Mix different raw materials in proportion and adjust the carbon-nitrogen ratio (25:1 to 30:1).
Adjust moisture
Add water or dry the raw materials to adjust the moisture content to 50%-60% to create suitable conditions for fermentation.
Add fermentation agent
Add fermentation agent (such as EM bacteria or Bacillus subtilis) to promote the decomposition of organic matter.
Composting
Pile the raw materials into piles and cover them with breathable materials. Turn the piles regularly to ensure ventilation and control the temperature at 50-70℃. The fermentation time is usually 15-30 days until the materials are fully decomposed.
Crushing and screening
Use fertilizer crusher to crush the fermented material into fine powder. Screen out impurities that are not completely decomposed to ensure that the material is fine and uniform.
Mixing ingredients and granulation
Add trace elements (such as calcium, magnesium, zinc) or other functional auxiliary materials (such as humic acid) as needed to improve fertilizer efficiency. Use a granulator to press the material into granules. Adjust the particle size (usually 2-5 mm) to meet different needs.
Drying and cooling
Send the granules into the dryer to reduce the moisture to 10%-15% to improve the particle strength. Cool to room temperature to prevent the granules from agglomerating.
Coating treatment
Use a coating machine to coat the granules. The coating material can be selected from resin, paraffin or polymer materials. After coating, the slow release performance, moisture resistance and compressive strength of the granules can be improved.
Screening and packaging
Use a screening machine to separate qualified particles. Particles that are too large or too small can be reprocessed. The finished particles are packed into moisture-proof packaging bags and stored in a dry and ventilated place to avoid moisture.
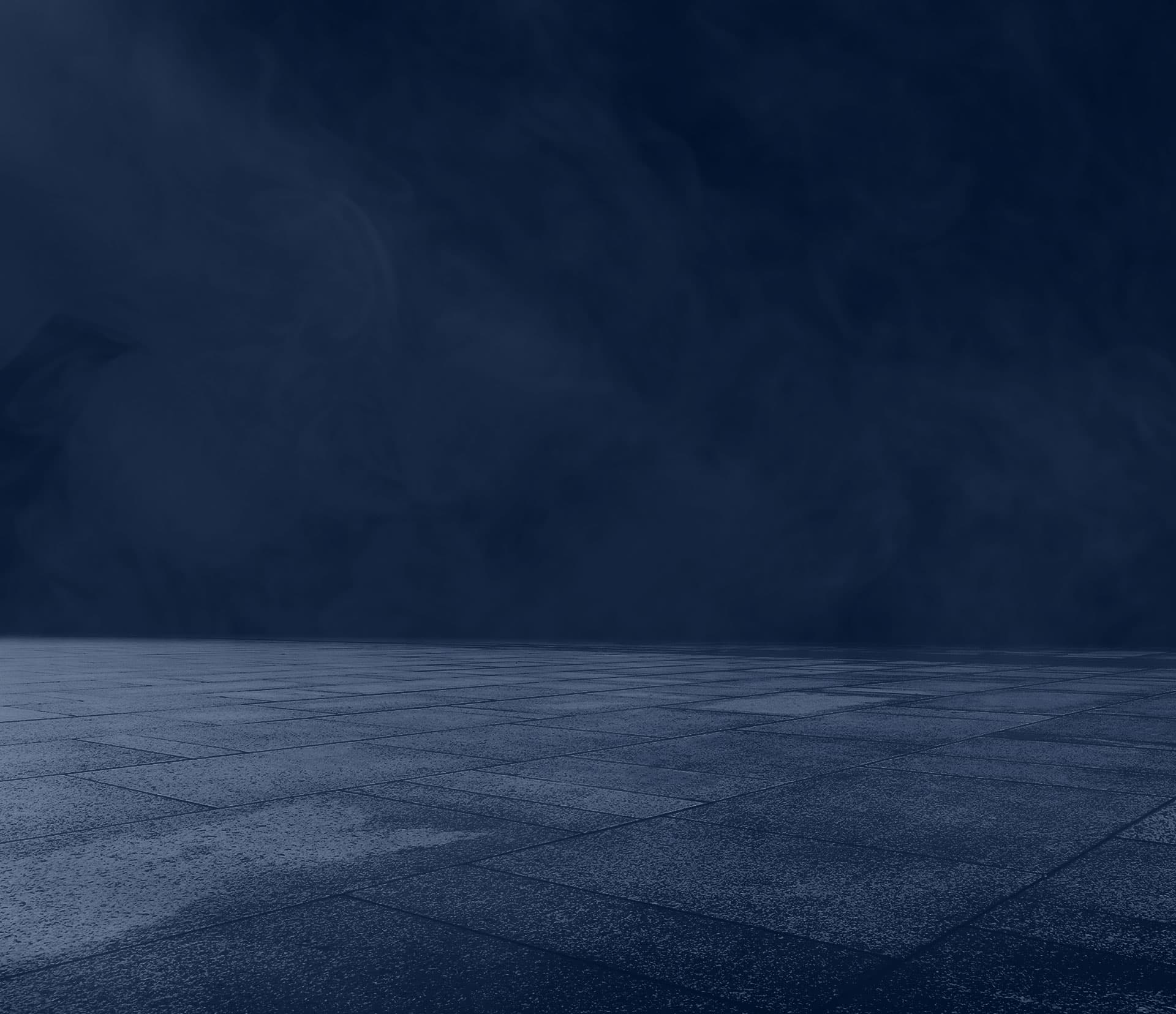
Organic Fertilizer Production Plant design & equipment
— Richi Machinery —
Our full-line production systems for organic fertilizer offer a holistic solution for complex production requirements and raw material properties from product feeding to final packaging covers all steps. Designing the process of organic fertilizer production plant requires comprehensive consideration of raw material characteristics, production scale, equipment selection, product quality, automation and intelligence, safety and hygiene, environmental protection requirements.
Our individually configurable fertilizer systems are perfect for the precise and efficient production of various organic fertilizer such as powders and granules, optimizing the production plants and increasing operational efficiency. The modular design allows for quick adaptation to different organic fertilizer and raw material properties.
Our organic fertilizer plant optimizes the entire organic fertilizer process, which leads to a significant increase in efficiency. They seamlessly integrate various crushing, fermentation, mixing, granulation, drying and packaging technologies into a single, coordinated production line, making them ideal for industries that place high demands on precision, automation and safety.
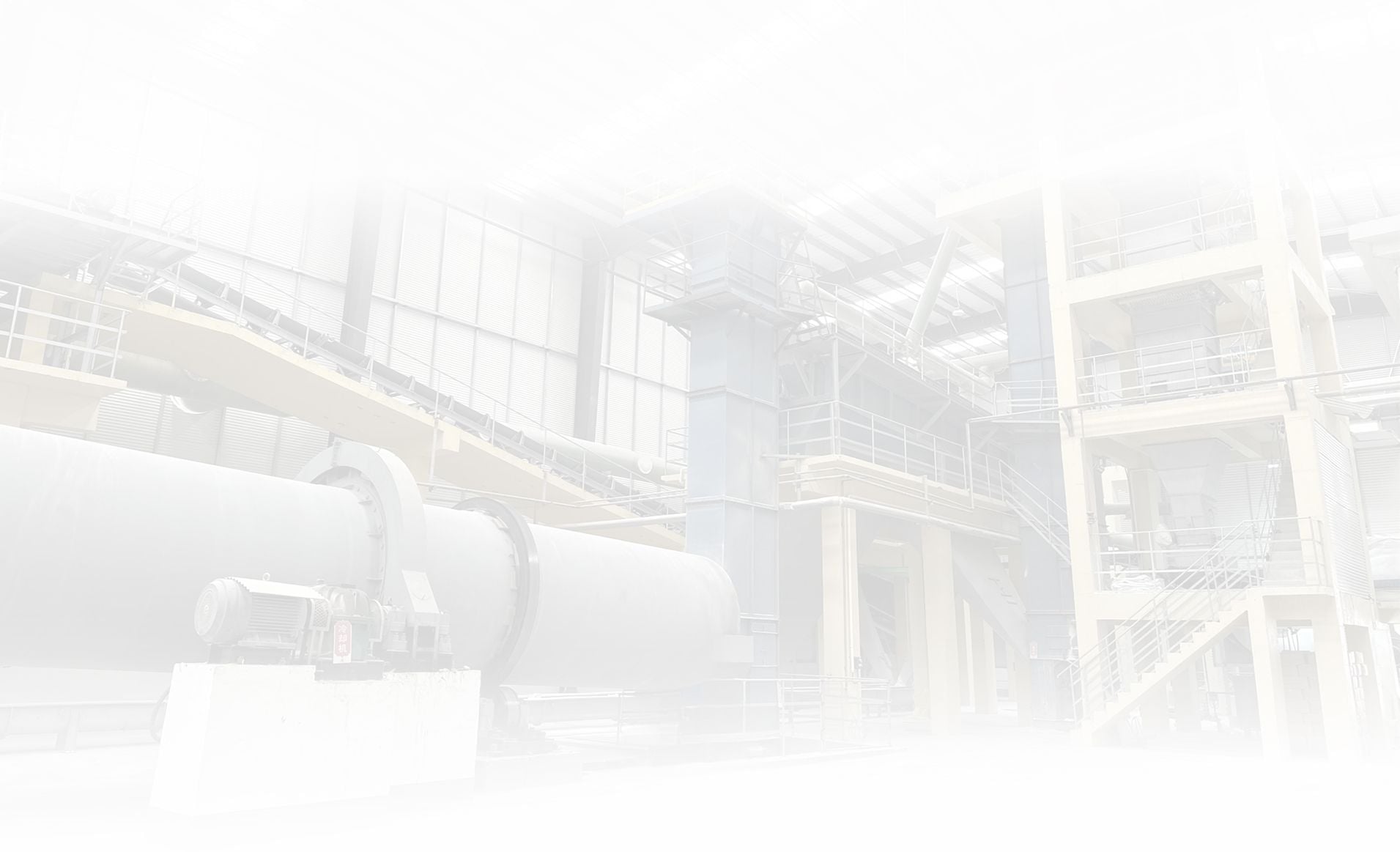
organic fertilizer production plant cost
— Richi Machinery —
The organic fertilizer production plant price is usually between 20,000-1,500,000 USD. This price only refers to the price of a full set of organic fertilizer equipment.
Production Scale | Investment Cost (USD) | Total Power | Profit cycle |
1-2T/H | 20,000-220,000 | 27-75KW | 0.5-3 Year |
3-4T/H | 40,000-350,000 | 47-75KW | |
5-6T/H | 60,000-480,000 | 53-165KW | |
8-10T/H | 10,000-600,000 | 68-259KW | |
10-12T/H | 150,000-800,000 | 125-410KW | |
12-15T/H | 200,000-1,100,000 | 358-620KW | |
15-20T/H | 35,0000-1,500,000 | 545-870KW | |
Higher capacity to 60 t/h | … | … | |
About the profit: 1. Depends on the customer’s local organic fertilizer price and raw material price, which is determined by the difference of resources in different regions; 2. Depending on the operating cost of the organic fertilizer equipment, it is composed of worker wages, electricity costs, and wearing parts costs, among which worker wages and electricity fees are relatively fixed, and the cost of wearing parts is related to the configuration and operation of the entire fertilizer making equipment; 3. It depends on the customer’s management of the complete organic fertilizer production plants. Responsible managers & skilled fertilizer equipment operators are the foundation for the smooth operation and high returns of any organic fertilizer plants. |
Cost to start an complete organic fertilizer production plant:
The construction cost of an organic fertilizer production plant involves land, plant, equipment, installation, energy, environmental protection, labor, raw materials, transportation, approval and other aspects. The specific cost varies depending on the project scale, equipment selection and regional differences.
Land cost | Plant construction cost | Equipment purchase |
Land purchase or lease costs: need to be determined according to geographical location and area. If it is leased, long-term rent needs to be considered. | Plant design and construction: including raw material warehouse, fermentation workshop, production workshop, finished product warehouse, etc., involving building materials and construction costs. | Such as fermentation tanks, compost turners, crushing equipment, mixing equipment, granulation equipment, drying and cooling equipment, screening equipment, packaging equipment, conveyors, dust removal equipment, etc. |
Installation and commissioning | Power and energy | Environmental protection facilities |
Equipment installation and commissioning: Professionals are required to ensure the normal operation of the equipment. | Power facilities: including transformers, cables, etc. Energy consumption: such as electricity, fuel, etc. | Such as deodorization equipment, wastewater treatment system, noise reduction measures. |
Labor costs | Raw material costs | Transportation and logistics |
Staff wages: including production, management, technical personnel, etc. | Raw material procurement: such as livestock and poultry manure, straw, etc. | Transportation equipment: such as forklifts, trucks, etc. Logistics costs: transportation costs of raw materials and finished products. |
Licenses and Approvals | Other costs | Maintenance and repairs |
Environmental approval: Approval from the environmental protection department is required. Production license: Relevant production licenses are required. | Insurance costs: Insurance for equipment, plant, etc. Working capital: For daily operations. | Equipment maintenance: Regular maintenance and repair costs. |
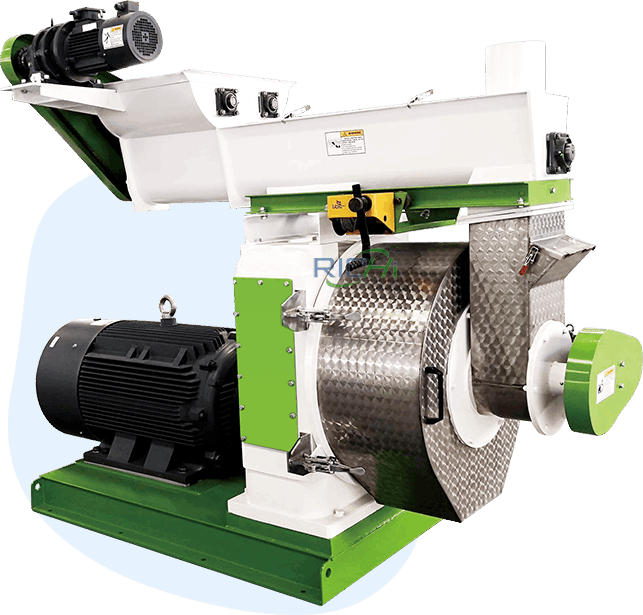
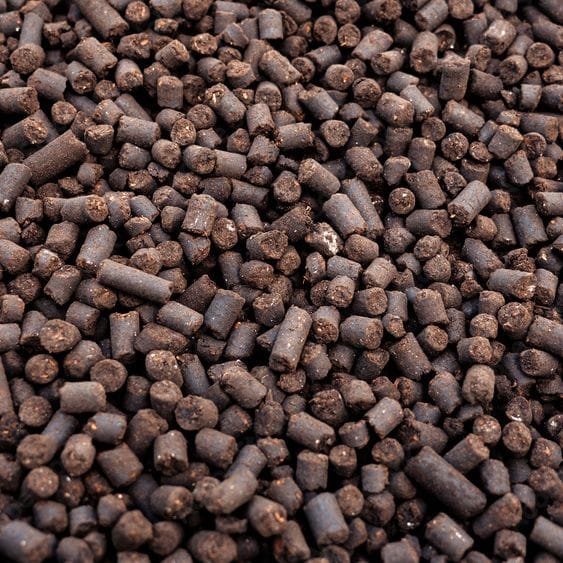
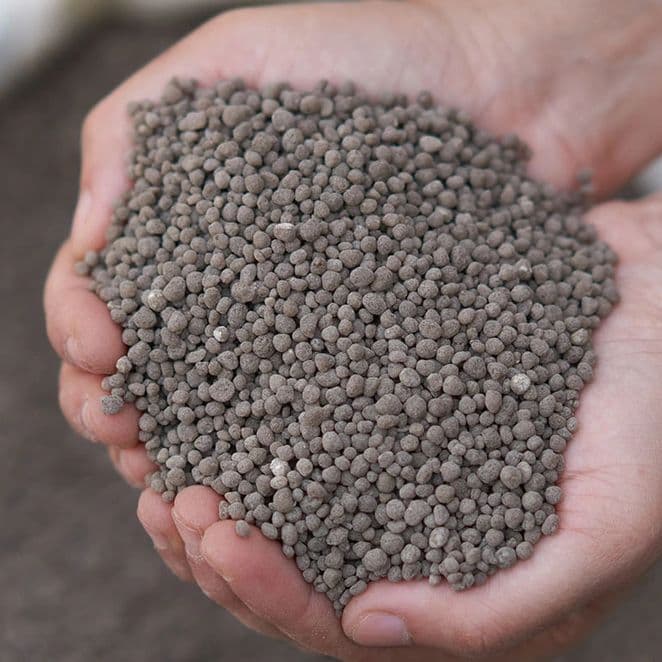
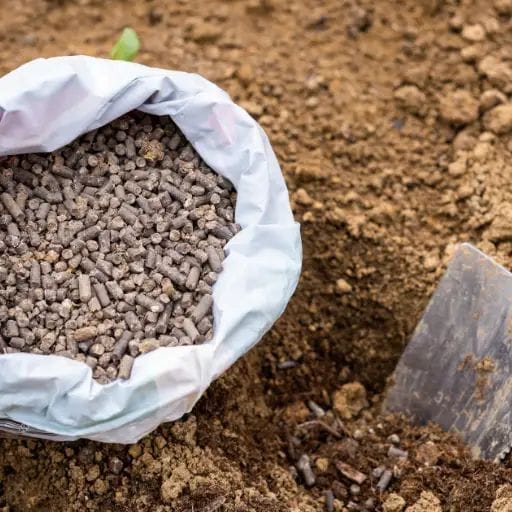
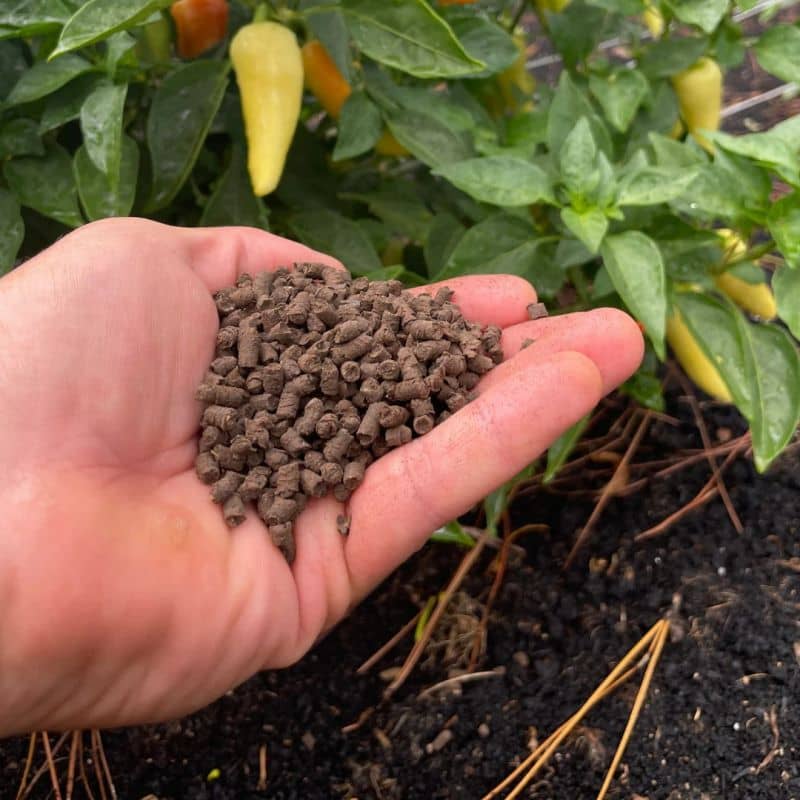
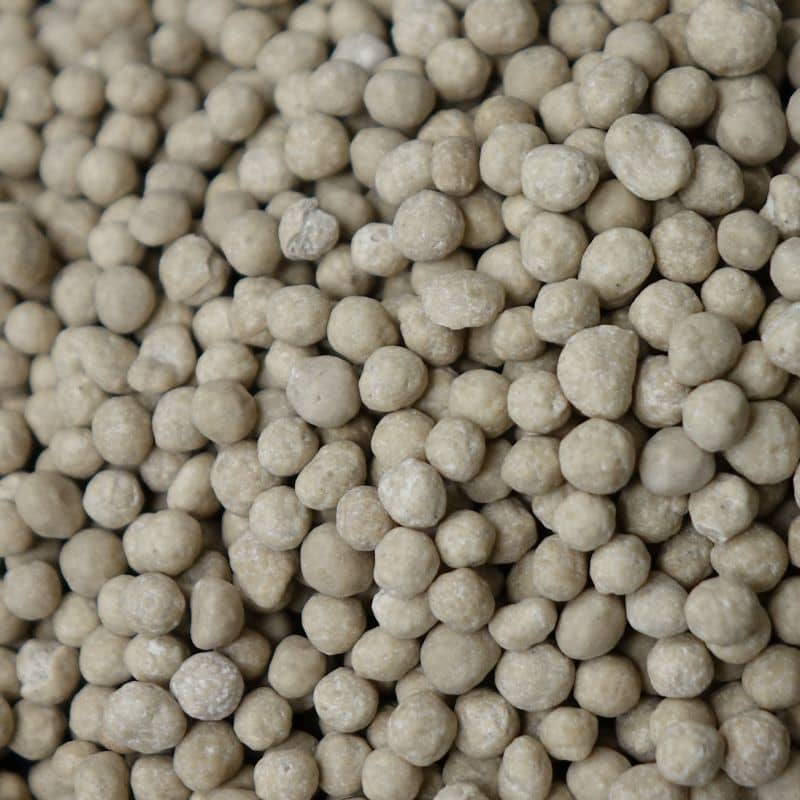
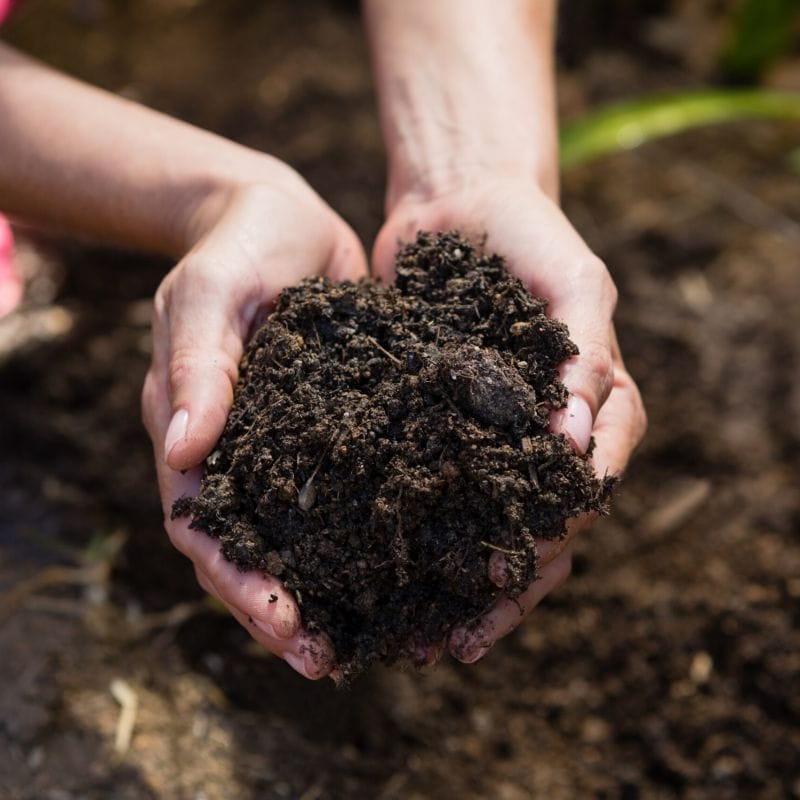
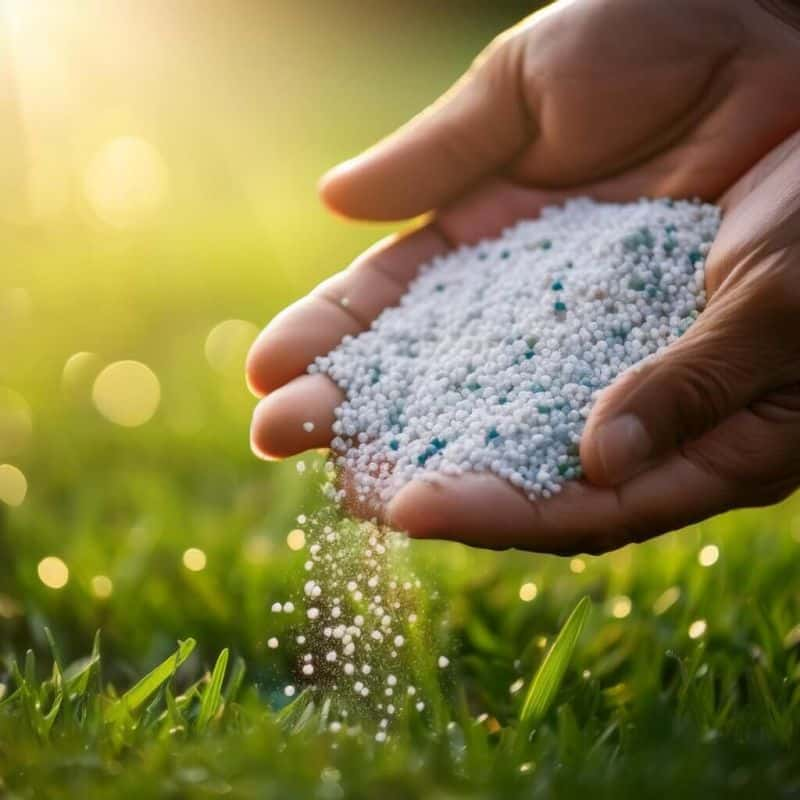
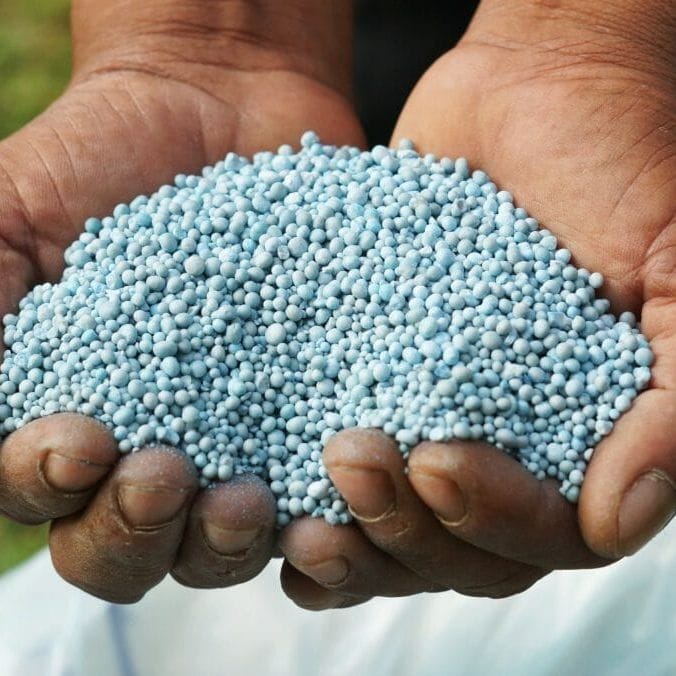
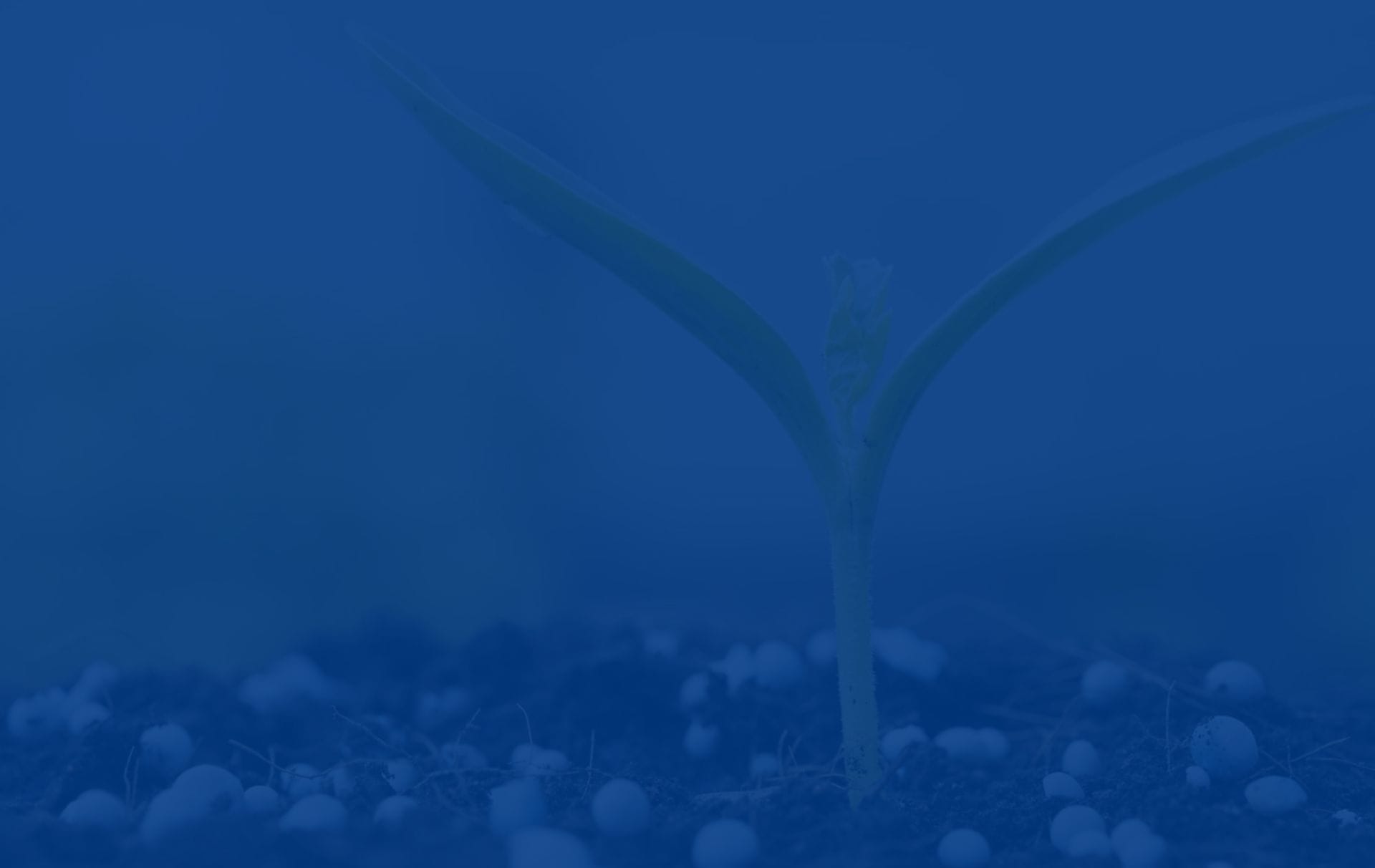
organic fertilizer production plant projects
In RICHI MACHIINERY,Every organic fertilizer production project an individual solution according to a standardized process. We’re committed to helping organic fertilizer manufacturers achieve success by providing reliable organic fertilizer prouduction solutions tailored to their unique needs. From optimizing production plants to streamlining entire operations, our solutions have made a tangible impact on our customer’s bottom line. Explore our organic fertilizer production cases to see how we’ve solved businesses unique challenges.
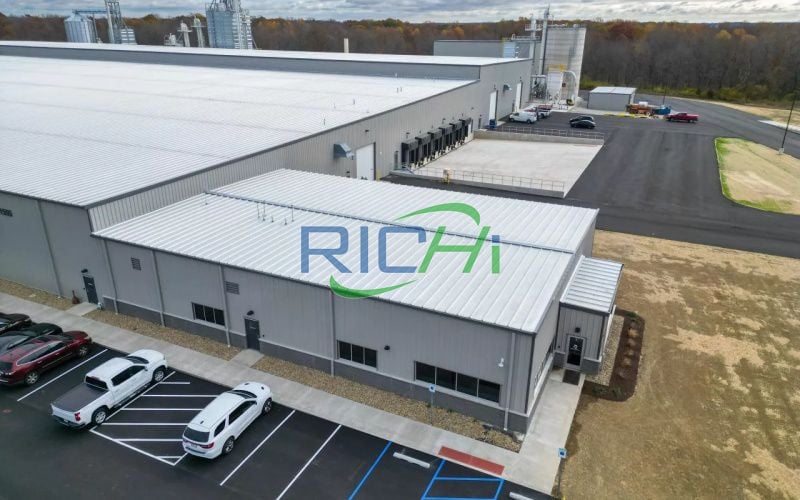
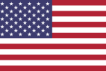
● United States
Organic Fertilizer Production Line In United States
- raw materials: Pig manure, cow manure, chicken manure, straw
- capacity: 10-12T/H
- project investment: $530,000
→
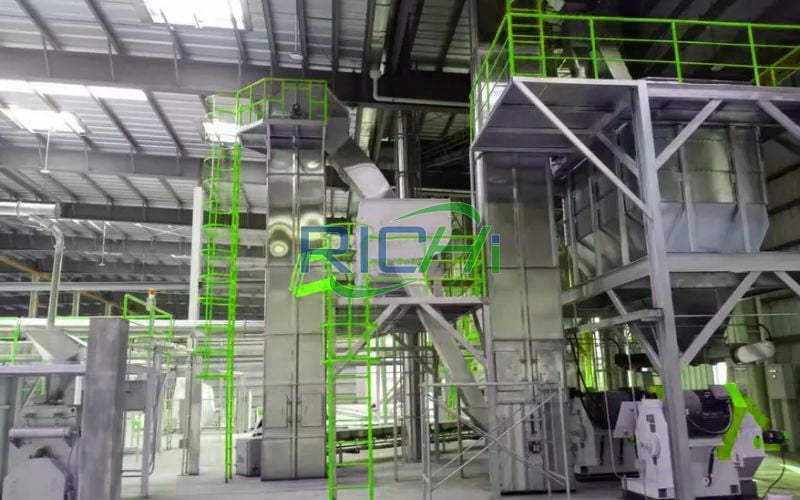
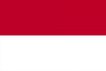
● Indonesia
Fertilizer Blending Plant in Indonesia
- raw materials: Peat soil, Tobacco stems, Mushroom waste residue
- capacity: 10T/H
- project investment: $270,000
→
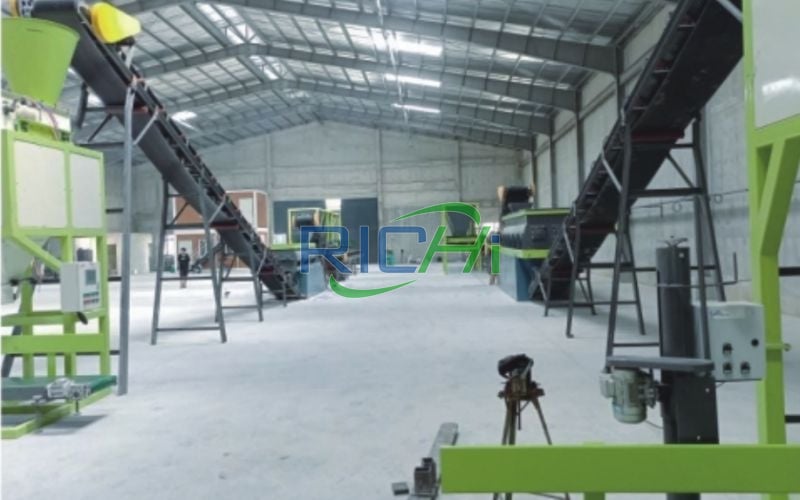
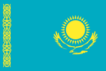
● Kazakhstan
Organic Fertilizer Manufacturing Plant In Kazakhstan
- raw materials: Beer mud, Pig manure, Soybean meal
- capacity: 10-12T/H
- project investment: $460,000
→
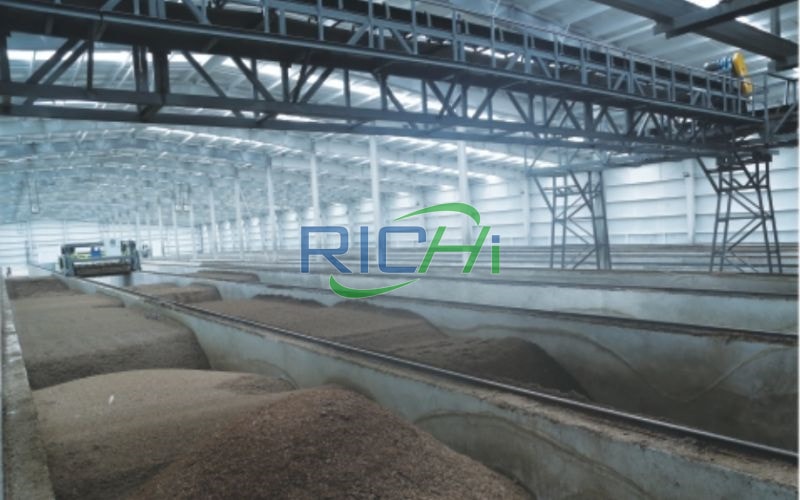
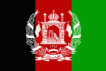
● Afghanistan
Organic Manure Production Plant In Afghanistan
- raw materials: Livestock and poultry manure, Charcoal powder
- capacity: 10T/H
- project investment: $330,000
→
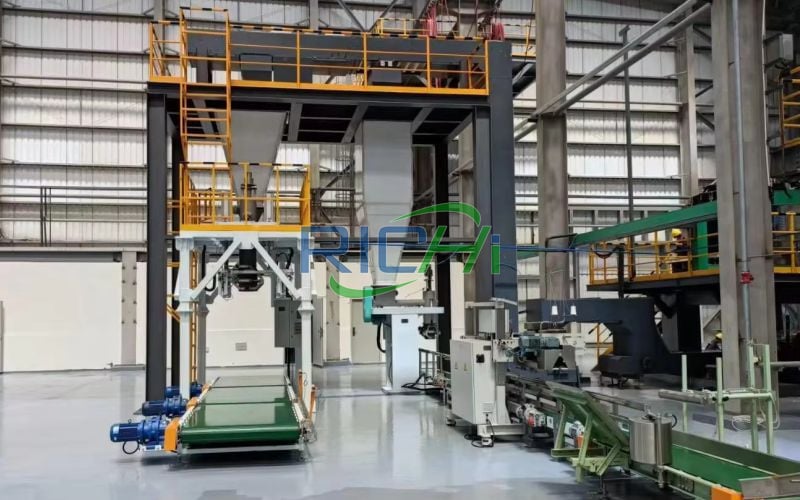
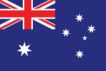
● Australia
Small Scale Fertilizer Plant In Australia
- raw materials: Chicken Manure, Rice bran, Sawdust, Egg shell
- capacity: 1-2T/H
- project investment: $110,000
→
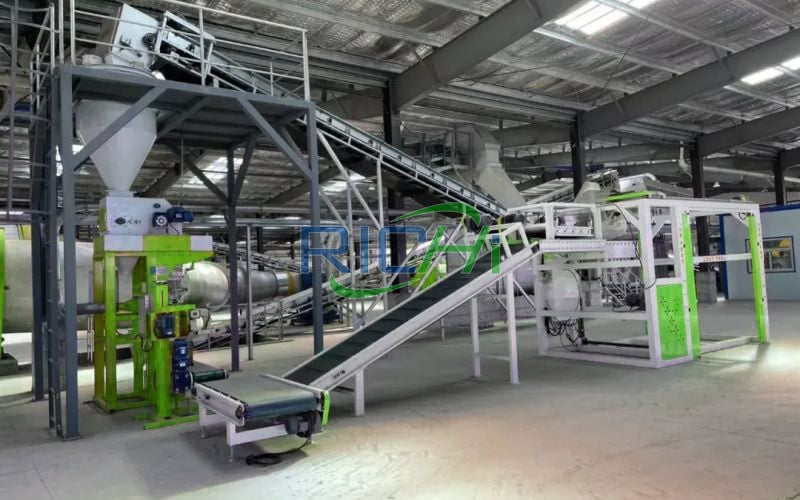
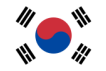
● South Korea
Organic Fertilizer Processing Plant In south Korea
- raw materials: Livestock and poultry manure, Agricultural waste
- capacity: 4T/H
- project investment: $160,000
→
[case study] organic fertilizer production plant in United States
Next, we will share with you one of our American organic fertilizer production plant projects.
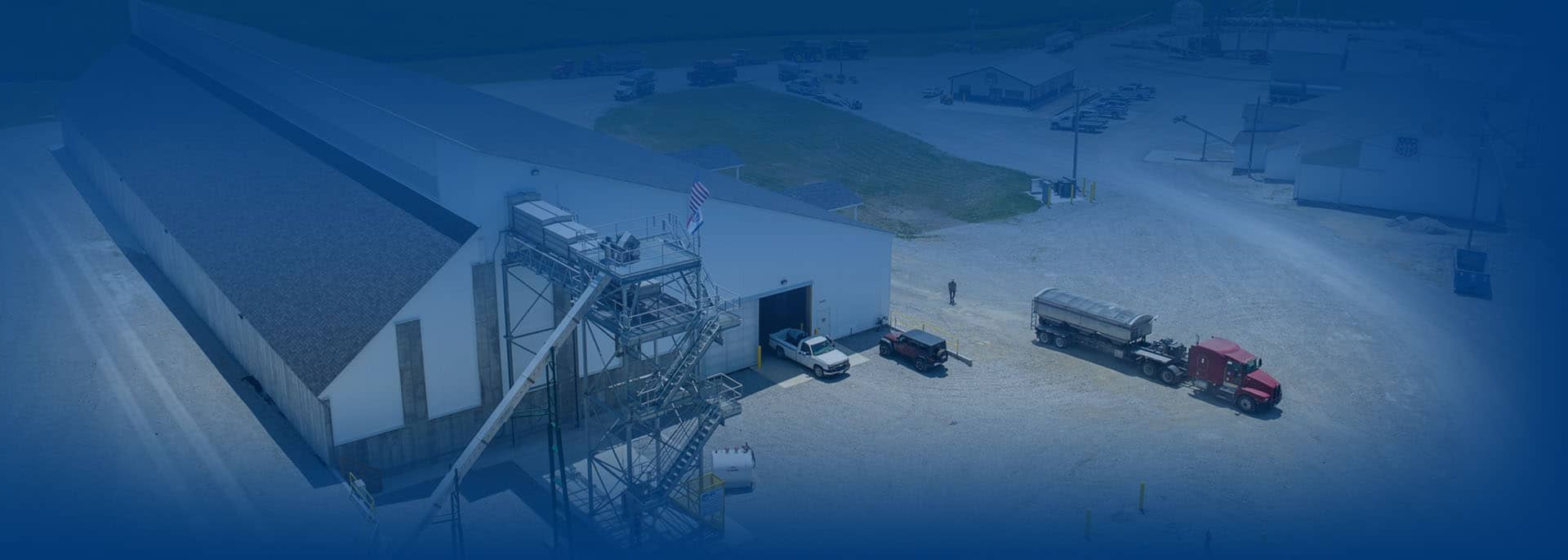
8T/H organic fertilizer production plant in United States
This is an organic fertilizer pellet production plant with an annual output of 20,000 tons and an hourly output of 8 tons. The customer mainly uses sludge and straw as the main raw materials. The main equipment used in this project includes fermentation tanks, crushers, mixers, dryers, organic fertilizer granulators, coolers, automatic packaging machines, etc.
The project mainly built production workshops, warehouses, guard rooms, etc.
Name | Engineering composition | Construction content |
Main engineering | Production workshop | Steel structure integrated building, one floor, divided into storage area 1200m2, processing area 500m2, crushing area 200m2, fermentation area 1000m2 by functional zoning. |
Auxiliary engineering | Guard room | Brick-concrete structure, one floor, covering an area of 10m2 |
Sludge storage tank | Located in the workshop, it is a semi-above-ground tank body, covering an area of 1000m2, with a cofferdam set around it, and the tank body is focused on anti-seepage. | |
Straw storage area | Located in the workshop, covers an area of 200m2 | |
Warehouse | Located on the east side of the factory boundary, covers an area of 500m2, used for storage of raw materials and finished products. | |
Comprehensive office building | 3 buildings, each with three floors, used for office and accommodation of employees, brick-concrete structure, total area of 250m2 | |
Public engineering | Water supply | The water used in this project mainly includes workshop water and employee living water, and the water supply source is the municipal tap water supply network. |
Drainage | The drainage system of the project implements a rainwater and sewage diversion system. Rainwater is discharged into the municipal rainwater network through the rainwater pipes in the factory area through surface runoff. Domestic sewage is reused in production after being treated in septic tanks and is not discharged. | |
Power supply | Accessed by the municipal power grid, it can meet production needs |
product plan
Product Name | Output |
Organic Fertilizer | 20000t/a |
organic fertilizer production plant process design
- Crushing:
The purchased straw is crushed by a crusher. - Material mixing:
The project purchases sludge and straw from domestic sewage treatment plants, and auxiliary materials include activators, fermentation agents, deodorant liquid, etc. Sludge and straw are in bulk, and a sludge storage tank is set up. A cofferdam is set up around it and anti-seepage measures are set up.
Fermentation agents and deodorant liquid are in barrels. First, the sludge and straw from the sewage treatment plant are put into the fermentation area, and then put into the mixer by a forklift. According to the proportion, they are mixed by a semi-enclosed mixer. - Anaerobic fermentation and aging:
The mixed materials are put into the fermentation tank from the mixer by a spiral closed conveyor belt, and then put into the fermentation tank by a forklift. Compost clinker and straw are used as conditioners to change the air permeability, and activators are added to make the anaerobic bacteria more active, so that the fermentation is in an optimal state of maturity.
The fermentation time is 8 days. This process maintains a constant temperature of about 55℃~65℃, uses electric heating as a heat source for high-temperature fermentation, and uses an anti-odor film to seal. The moisture contained in the sludge produces some water vapor. After the fermentation time is up, the fertilizer is aged by natural stillness. - Screening:
The dried material is screened by a screening machine with a screen of 4.5mm. The screened material naturally falls into the bottom of the screening machine, which is a closed space.
It enters the conveyor belt through the discharge port and is transported to the semi-finished material factory for cooling; the screened material (>4.5mm) returns to the crusher for crushing. - Air cooling:
The semi-finished products after screening are temporarily stored in the semi-finished material silo. Since the material contains a certain amount of moisture, the moisture of the material is evaporated and the heat is taken away through the air collection effect of the factory to achieve the purpose of air drying and cooling. - Granulation:
The air-cooled fertilizer is compressed, extruded, and granulated through a granulator for packaging.
Construction content
Item | Indicators |
Appearance | Brown particles |
Effective number of live bacteria | 100 million/ml |
Water content | Less than 10% |
Fineness | Particle size 2.5mm~4.5mm |
Organic matter (in terms of C) | 25% |
pH | 6.0~7.5 |
Number of miscellaneous bacteria | 20% |
Validity period | Not less than six months |
Ascaris egg mortality | 95%~100% |
Escherichia coli value | October 1 |
Mercury and its compounds (in terms of Hg) | ≤5mg/kg |
Cadmium and its compounds (in terms of Cd) | ≤3mg/kg |
Chromium and its compounds (in terms of Cr) | ≤70mg/kg |
Arsenic and its compounds (as As) | ≤30mg/kg |
Lead and its compounds (as Pb) | ≤60mg/kg |
Organic matter mass fraction (on a drying basis) % | ≥45 |
Total nutrients (nitrogen + phosphorus pentoxide + potassium oxide) mass fraction | ≥5.0 |
Water (fresh sample) mass fraction% | ≤3 |
Acidity and alkalinity | 5.5 ~8.5 |
Total arsenic (on a dry basis) | ≤15mg/kg |
Total mercury (on a dry basis) | ≤2mg/kg |
Total lead (on a dry basis) | ≤50mg/kg |
Total cadmium (on a dry basis) | ≤3mg/kg |
Total chromium (on a dry basis) | ≤150mg/kg |
Moisture content% | ≤30 |
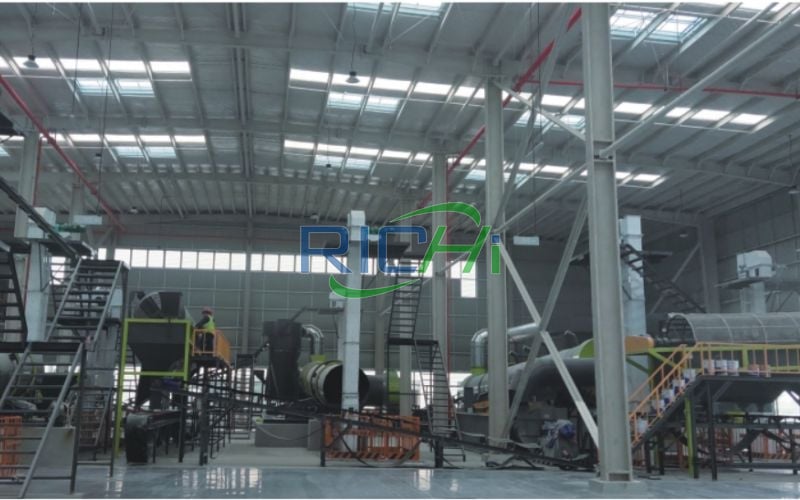
Raw material consumption
Raw material name | Usage amount |
Sludge | 20000t/a |
Straw | 5005t/a |
High-efficiency fermentation agent | 300t/a |
Activator | 5000t/a |
Plant deodorant | 2t/a |
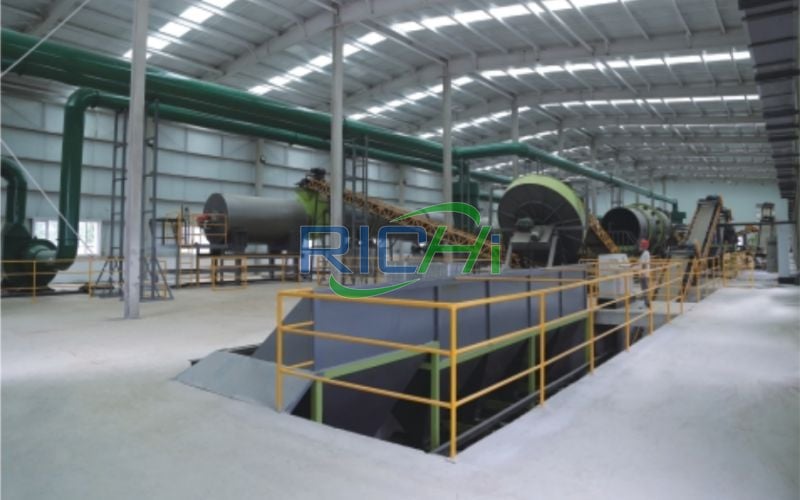
Employees and work system
The project has 30 employees, working 300 days per year, 2400 hours per year, and adopts a single-shift work system.
RICHI MACHINERY
how to make organic fertilizer for business?
Starting an organic fertilizer business can be a profitable and environmentally friendly venture, especially with the growing demand for sustainable agricultural practices. Below is a step-by-step guide on how to make organic fertilizer for business and organic fertilizer production plant:
Understand the Market and Regulations
- Market Research: Identify the demand for organic fertilizers in your target market (e.g., organic farms, home gardeners, landscaping companies).
- Regulations: Check local and national regulations for organic fertilizer production, including permits, environmental compliance, and labeling requirements.
Choose Raw Materials
Organic fertilizers are made from natural materials. Common raw materials include:
- Animal Manure: Cow, poultry, horse, or sheep manure.
- Plant Waste: Crop residues, grass clippings, leaves, and straw.
- Food Waste: Fruit and vegetable scraps.
- Industrial Byproducts: Compost from food processing or brewery waste.
- Other Materials: Bone meal, fish emulsion, seaweed, and biochar.
Set Up a Production Facility
- Location: Choose a site with enough space for raw material storage, composting, and production. Ensure it is close to raw material sources and target markets.
- Equipment: Invest in the necessary equipment, such as: compost turners or mixers, grinders, granulators, drying machine or screening and packaging machines, etc.
Composting Process
Composting is a key step in organic fertilizer production. Follow these steps:
- Cure the Compost: Allow the compost to mature for 2-6 months until it is stable and odor-free.
- Shred Raw Materials: Break down large materials into smaller pieces for faster decomposition.
- Mix Ingredients: Combine carbon-rich materials (e.g., straw, leaves) with nitrogen-rich materials (e.g., manure, food waste) in a 3:1 ratio.
- Pile or Windrow: Create compost piles or windrows (long rows of compost) and turn them regularly to aerate.
- Monitor Conditions: Maintain moisture (40-60%) and temperature (50-70°C) for optimal microbial activity.
Processing and Granulation
- Crushing and Mixing: Crush the composted material and mix it with additional nutrients (e.g., bone meal, rock phosphate) if needed.
- Granulation: Use a granulator to shape the fertilizer into pellets for easier application.
- Drying and Cooling: Dry the granules to reduce moisture and cool them for storage.
- Screening: Separate oversized or undersized granules to ensure uniform product quality.
Packaging and Labeling
- Packaging: Use durable, eco-friendly bags or containers for packaging.
- Labeling: Include essential information on the label, such as:
- Product name.
- Nutrient content (e.g., NPK ratio).
- Usage instructions.
- Organic certification (if applicable).
Obtain Organic Certification
If you want to market your product as “organic,” obtain certification from a recognized organization (e.g., USDA Organic, EU Organic, or local certifiers).
Follow the guidelines for organic production, including using approved raw materials and avoiding synthetic additives.
Marketing and Sales
- Target Customers: Focus on organic farmers, home gardeners, landscaping companies, and nurseries.
- Branding: Create a strong brand that emphasizes sustainability and quality.
- Distribution Channels:
- Sell directly to farmers or through agricultural supply stores.
- Use online platforms (e.g., Amazon, Etsy) to reach home gardeners.
- Promotion: Attend trade shows, advertise in agricultural magazines, and use social media to promote your product.
Video of organic fertilizer production plant
An organic fertilizer production plant can not only meet the local fertilizer demand, but also meet the needs of the surrounding market. Organic fertilizer is widely used in various fields such as farmland, fruit trees, flowers, landscaping, soil improvement, etc., and has a very good effect.
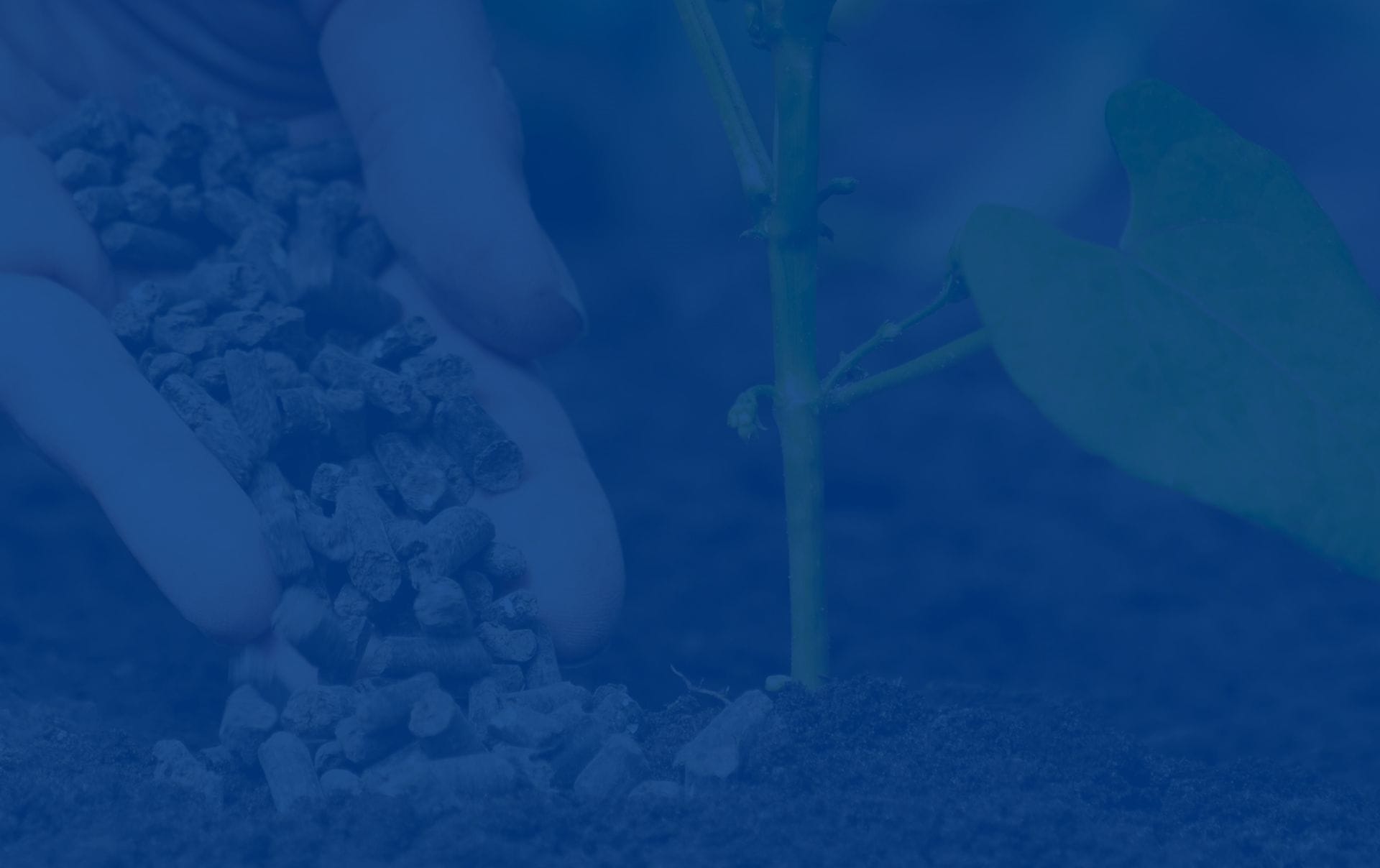
Explore more fertilizer plant solutions
At RICHI MACHINERY, we not only offer organic fertilizer production lines, we also offer a comprehensive range of fertilizer processing plant and equipment, ranging from stand-alone machines to complete turnkey fertilizer production systems.
Our diverse options and custom-engineering abilities ensure that we can meet your application’s unique requirements. We also offer installation, field service technical support, contract packaging, warehousing programs, and inventory services, and we’ll train your staff before leaving your site to make sure you get the most out of your investment.
Contact us today for a trusted partner to help you improve your productivity and profitability through industry-leading fertilizer processing technology.
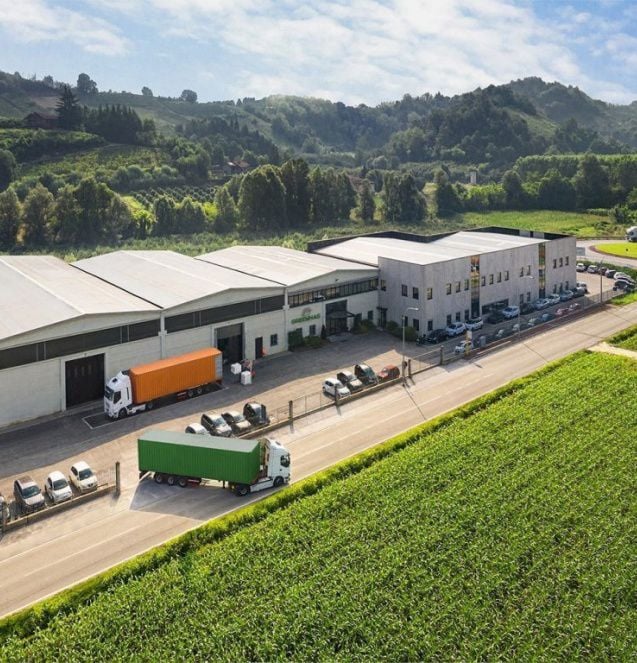
compound fertilizer production line
Compound fertilizer production line refers to a complete production system that produces compound fertilizer by combining nitrogen (N), phosphorus (P), potassium (K) and other nutrients in a certain proportion through chemical synthesis or physical mixing.
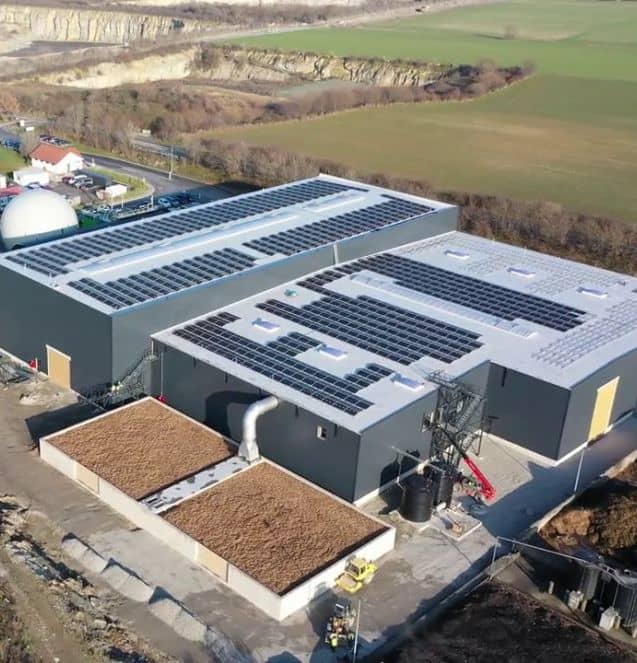
fertilizer blending plant
Fertilizer Blending Plant is a facility that produces customized compound fertilizers by physically mixing multiple single fertilizers (such as urea, diammonium phosphate, potassium chloride, etc.) in specific proportions.
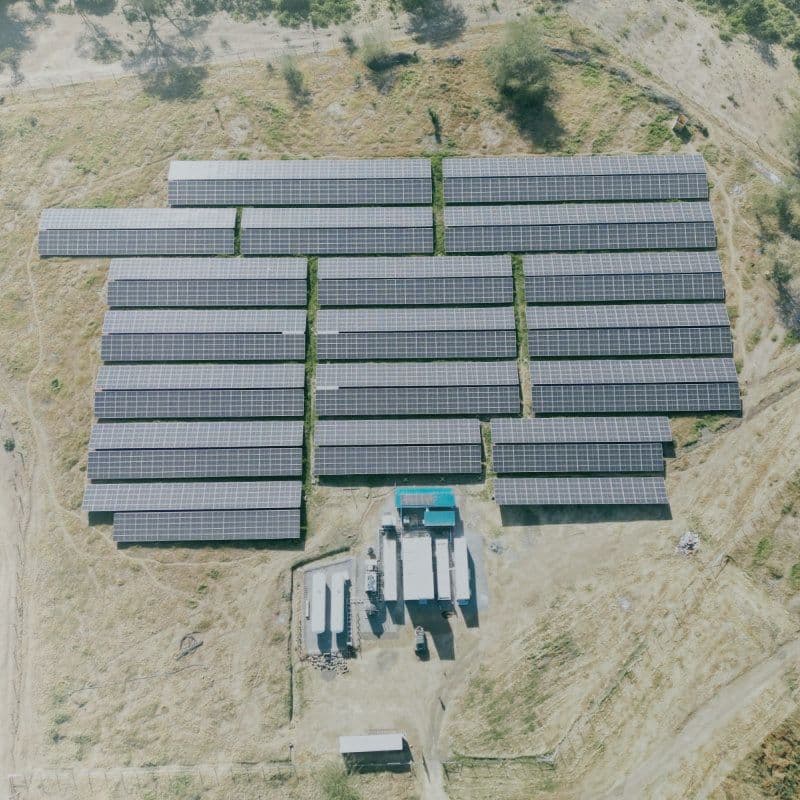
1-2T/H
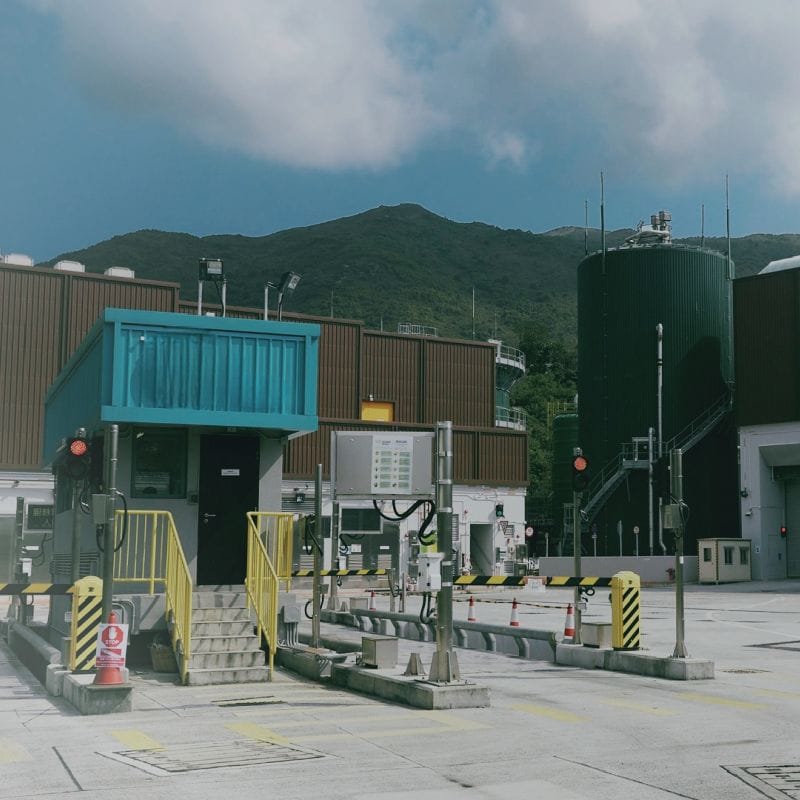
3-4T/H
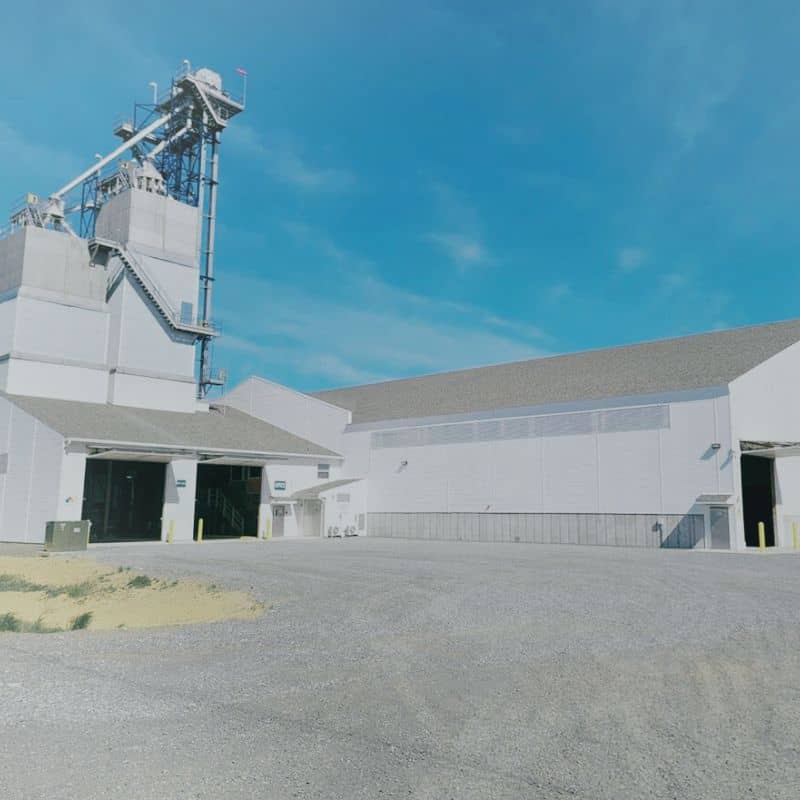
5-6T/H
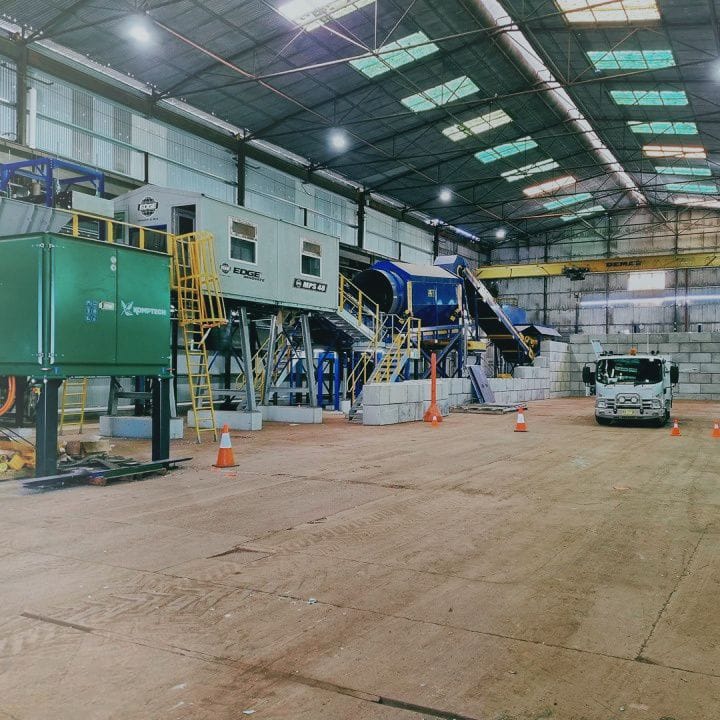
8-10T/H

12-15T/H
Frequently asked questions
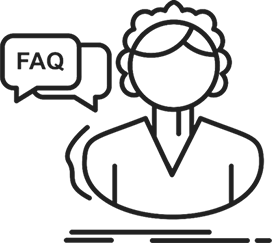
What issues need to be considered when configuring equipment for an organic fertilizer production plant?
When configuring equipment for an organic fertilizer production plant, several key issues need to be considered to ensure efficient, stable and economical operation of the production line. The following are the main considerations:
- Production demand
- Capacity requirements: Select appropriate equipment specifications and quantities based on target output.
- Product type: Different products may require different equipment, such as granular fertilizer, powdered fertilizer, etc.
- Process flow
- Process design: Clarify each production link (such as fermentation, crushing, mixing, granulation, drying, cooling, screening, packaging) and its sequence.
- Equipment matching: Ensure that the equipment in each link can be smoothly connected to avoid bottlenecks.
- Equipment selection
- Performance parameters: Select equipment that meets production needs, such as processing capacity, power, efficiency, etc.
- Brand and quality: Choose a reliable brand to ensure equipment durability and stability.
- Degree of automation: Select manual, semi-automatic or fully automatic equipment according to needs.
- Space layout
- Plant size: Ensure that the organic fertilizer production plant layout is reasonable and leave enough space for operation and maintenance.
- Logistics channel: ensure smooth transportation of raw materials and finished products.
- Energy consumption
- Power demand: evaluate the total power demand of the equipment and ensure that the power supply system matches.
- Fuel consumption: if there is drying equipment, the fuel type and consumption need to be considered.
- Environmental protection requirements
- Waste gas treatment: configure deodorization and dust removal equipment to ensure that emissions meet the standards.
- Wastewater treatment: if wastewater is generated, a treatment system needs to be configured.
- Noise control: take noise reduction measures to reduce noise pollution.
- Safety and compliance
- Safety protection: the equipment needs to be equipped with necessary safety devices, such as emergency shutdown, protective cover, etc.
- Compliance: ensure that the equipment complies with relevant regulations and standards.
- Maintenance and repair
- Maintenance convenience: choose equipment that is easy to maintain to reduce downtime.
- Spare parts supply: ensure that the equipment spare parts are adequately supplied for timely replacement.
- Cost control
- Initial investment: comprehensively consider the costs of equipment purchase, installation, commissioning, etc.
- Operating costs: Evaluate long-term costs such as energy consumption, maintenance, and labor.
- Technical support and training
- Supplier support: Choose suppliers that provide good technical support and after-sales service.
- Employee training: Ensure that operators and maintenance personnel are fully trained.
- Scalability and flexibility
- Scalability: Consider future capacity increases and choose scalable equipment.
- Flexibility: Choose equipment that can adapt to a variety of products and processes to improve organic fertilizer production plant flexibility.
- Logistics and supply chain
- Raw material supply: Ensure that the supply of raw materials is stable and the equipment can adapt to different raw material characteristics.
- Finished product transportation: Consider the packaging and transportation needs of finished products and configure appropriate packaging equipment.
Configuring organic fertilizer production plant equipment requires comprehensive consideration of production needs, process flow, equipment selection, space layout, energy consumption, environmental protection requirements, safety compliance, maintenance and repair, cost control, technical support, scalability, and logistics supply chain to ensure that the production plant operates efficiently, stably, and economically.
What civil engineering works are needed to build an organic fertilizer production line?
The civil engineering works of organic fertilizer production line projects cover many aspects to ensure the smooth operation of the production line and meet environmental protection requirements. The following are the main civil engineering works:
- Plant construction
- Raw material warehouse: used to store raw materials such as livestock and poultry manure and straw, which need to be moisture-proof and ventilated.
- Fermentation workshop: equipped with fermentation tanks or fermentation pools, which need to be corrosion-resistant and easy to clean.
- Production workshop: install crushing, mixing, granulation, drying, cooling, screening and other equipment, which need sufficient space and good ventilation.
- Finished product warehouse: used to store finished organic fertilizers, which need to be moisture-proof and ventilated.
- Ground hardening and drainage system
- Ground hardening: The floor of the workshop and warehouse needs to be hardened, usually with concrete, to ensure load-bearing and durability.
- Drainage system: build drainage ditches and sewage treatment facilities to prevent water accumulation and water pollution.
- Fermentation facilities
- Fermentation tanks or fermentation pools: used for raw material fermentation, which need to be corrosion-resistant and easy to clean, usually with concrete or anti-corrosion materials.
- Compost turning machine track: If there is a compost turning machine, a track needs to be built.
- Environmental protection facilities
- Waste gas treatment facilities: such as deodorization towers, dust collectors, etc., to reduce waste gas emissions.
- Wastewater treatment facilities: Build sedimentation tanks, filter tanks, etc. to treat production wastewater.
- Noise control facilities: such as soundproof walls to reduce noise pollution.
- Power and energy facilities
- Distribution room: Install transformers, distribution cabinets, etc. to ensure power supply.
- Energy supply facilities: If there is drying equipment, fuel storage facilities need to be built.
- Office and living facilities
- Office building: used for management and office.
- Staff dormitory: If necessary, build staff dormitory.
- Canteen and toilet: Provide basic living facilities.
- Roads and logistics channels
- Factory roads: Build roads connecting workshops and warehouses to ensure smooth transportation.
- Logistics channels: Ensure convenient access for raw material and finished product transportation vehicles.
- Fences and gates
- Fences: Build fences to ensure the safety of the factory area.
- Gates: Set up main entrances and secondary entrances for easy management and transportation.
- Greening and landscape
- Green belts: Green around and inside the factory area to improve the environment.
- Landscape design: Appropriately design the landscape to enhance the image of the factory area.
- Firefighting facilities
- Fire passages: Ensure smooth access for fire trucks.
- Firefighting equipment: Equipped with fire extinguishers, fire hydrants, etc.
The civil engineering of the organic fertilizer production line project includes plant construction, ground hardening, drainage system, fermentation facilities, environmental protection facilities, power facilities, office and living facilities, roads and logistics channels, walls and gates, greening and landscape, and firefighting facilities, etc., to ensure the efficient, environmentally friendly and safe operation of the production line.
For most customers, the main construction is the production workshop, raw material workshop, fermentation workshop and finished product workshop, and the construction of other facilities can be selected according to the capital budget.
How much floor space is needed to build an organic fertilizer production plant? How big a factory building is needed?
The floor space and plant size of an organic fertilizer production line depend on multiple factors, including production scale, process flow, equipment selection, raw material and finished product storage requirements, etc. The following are some common reference data and considerations:
1. Factors affecting floor space and plant size
(1) Production scale:
- Small organic fertilizer production plant (annual output less than 5,000 tons): small floor space, usually 2,000-5,000 square meters.
- Medium organic fertilizer production plant (annual output 5,000-20,000 tons): large floor space, usually 5,000-15,000 square meters.
- Large organic fertilizer production plant (annual output more than 20,000 tons): larger floor space, usually more than 15,000 square meters.
(2) Organic fertilizer production process flow:
A complete organic fertilizer production line usually includes: raw material storage area, fermentation area, production workshop (crushing, mixing, granulation, drying, cooling, screening, packaging), finished product warehouse, etc.
Each area requires a certain amount of space, especially the fermentation area and production workshop.
(3) Equipment selection:
The size and degree of automation of the equipment will affect the plant requirements. For example, a fully automatic organic fertilizer production plant may require a larger space to arrange the equipment, but it can reduce the manual operation area.
(4) Raw material and finished product storage:
The storage of raw materials (such as livestock and poultry manure, straw, etc.) and finished products requires a larger space, especially the raw material storage area and finished product warehouse.
(5) Environmental protection requirements:
Environmental protection facilities (such as waste gas treatment and wastewater treatment) also need to occupy a certain area.
(6) Plant layout:
Sufficient passages (such as logistics passages and fire passages) and green areas need to be reserved in the plant area, which will also affect the total floor area.
2. Area requirements of each functional area
(1) Raw material storage area:
Raw materials usually need to be stacked in the open air or built in a simple shed. The area depends on the type of raw materials and the storage volume.
Generally, 500-2000 square meters are required.
(2) Fermentation area:
The fermentation area is the core area, usually including fermentation tanks or fermentation pools.
The area of the fermentation area depends on the fermentation method (stack fermentation, tank fermentation, etc.) and the fermentation cycle.
Generally, 1000-5000 square meters are required.
(3) Production workshop:
The production workshop needs to accommodate equipment such as crushing, mixing, granulation, drying, cooling, screening, and packaging.
The workshop height usually needs to be 5-8 meters and the area needs to be 500-2000 square meters.
(4) Finished product warehouse:
The finished product warehouse is used to store packaged organic fertilizers. The area depends on the output and storage cycle.
Generally, 500-3000 square meters are required.
(5) Environmental protection facility area:
Including waste gas treatment equipment (such as deodorization tower), wastewater treatment pool, etc.
Generally, 200-1000 square meters are required.
(6) Office and living area:
Including offices, staff dormitories, canteens, etc.
Generally, 200-1000 square meters are required.
(7) Roads and greening:
Logistics channels and fire passages need to be reserved within the factory area, usually accounting for 10%-20% of the total area.
3. Factory building height requirements
The height of the production workshop usually needs to be 5-8 meters to accommodate equipment and ventilation systems.
The height of the raw material storage area and finished product warehouse can be slightly lower, but it must meet storage and transportation requirements.
When planning the area and layout of the organic fertilizer production plant, our engineers will combine specific needs, process flow and environmental protection requirements to reasonably design the factory layout to ensure efficient production and environmental compliance.
Which industries are suitable for investing in organic fertilizer production plants?
Investing in organic fertilizer production lines has broad market prospects, especially driven by organic agriculture, environmental protection policies and sustainable development trends around the world.
Agriculture and food industry:
Organic agriculture: The global organic agricultural area continues to grow, especially in Europe, North America and Asia-Pacific. According to IFOAM (International Federation of Organic Agriculture Movements), the global organic agricultural area has exceeded 72 million hectares, and there is a huge demand for organic fertilizers. At present, many food companies are promoting sustainable supply chains, and investing in organic fertilizer production lines can provide them with stable organic raw materials.
Animal husbandry:
Livestock and poultry breeding enterprises: Animal husbandry produces a large amount of livestock and poultry manure, which can be used as raw materials for organic fertilizers. Investing in organic fertilizer production lines can help breeding companies realize waste resource utilization and create additional income.
Environmental protection and waste treatment industry:
Waste treatment companies: Organic fertilizer production lines can convert agricultural waste (such as straw, fruit and vegetable residues) and urban organic waste into organic fertilizers, which is in line with the concept of circular economy.
Gardening and Landscape Industry:
Gardening companies: Organic fertilizers are in great demand in home gardening, golf courses, parks and other fields. Gardening companies can invest in organic fertilizer production lines to meet market demand.
Energy and Biotechnology Industry:
Bioenergy companies: Organic fertilizer production may produce byproducts (such as biogas), which can be used as renewable energy by bioenergy companies.
At present, since the raw materials used in organic fertilizer processing are very wide, the industries that invest in organic fertilizer production lines are not limited to the above, and more and more customers from other industries are also preparing to enter the organic fertilizer processing industry.
how to produce organic fertilizer from chicken manure?
The production process of chicken manure organic fertilizer includes multiple links.
- First, the chicken manure is fermented, and this step is fully completed by the efficient turning of the compost turning machine.
- Then, the raw materials enter the crusher for crushing, and then pass through the screening machine to ensure the uniformity of the raw materials.
- Then, the ingredients are batched through the automatic batching system, crushed again by the double-shaft crusher, and granulated by the chicken manure granulator to form granular organic fertilizer.
- After that, the dryer dries the pellets, the dust collector removes dust, and the cooler cools.
- Finally, the dust-removed and cooled pellets are coated by the coating machine, and then finely screened by the screening machine, packaged by the automatic packaging machine, and finally the finished products are put into storage.
Each production process requires specific equipment to complete.
- First, the materials are piled and fermented, and this process is efficiently completed by the trough compost turning machine. Its new design not only saves space, but also reduces the equipment investment cost.
- Then, the crushing equipment, feeding mixing equipment, granulation equipment, screening equipment, drying equipment and packaging equipment will play a role in turn, together forming a fully automatic production line.
- The entire fertilizer production plant saves time and manpower, and usually only 6 people are needed to complete the entire operation.
In addition, we also need to understand the composition of the investment cost of the chicken manure organic fertilizer production plant. This will help us understand the operation and investment of the production line more comprehensively.
The investment cost of the chicken manure organic fertilizer production plant covers many aspects.
- First, the cost of raw materials is the basis, which directly determines the production cost of the product.
- Secondly, the transportation cost cannot be ignored, especially for the long-distance transportation of raw materials and finished products.
- In addition, labor costs are also a key factor, including labor input in the production process.
- At the same time, equipment depreciation costs, packaging costs, and equipment maintenance and management energy consumption are also expenditure items that must be considered.
By fully understanding these cost components, we can more reasonably plan and control the investment and operation of the chicken manure organic fertilizer production plant.
I want to build a 1-2T/H organic fertilizer production line? Can you send me the equipment list?
We need to determine the organic fertilizer processing technology first, and then determine the organic fertilizer equipment. Below, we can provide you with a standard configuration of a 1-2t/h organic fertilizer production line:
No. | Item | Qty |
1 | Compost Turner | 1set |
2 | Loading hopper | 1set |
3 | Belt Conveyor | 1set |
4 | Vertical crusher | 1set |
5 | Belt Conveyor | 1set |
6 | Powder screening machine | 1set |
7 | Belt Conveyor | 1set |
8 | Horizontal mixer | 1set |
9 | Screw conveyor | 1set |
10 | Belt Conveyor | 1set |
11 | Organic fertilizer Granulator | 1set |
12 | Granule polishing machine | 1set |
13 | Belt Conveyor | 1set |
14 | Rotary Dryer | 1set |
15 | Hot air Stove | 1set |
16 | Cyclone | 1set |
17 | ID Fan | 1set |
18 | Belt Conveyor | 1set |
19 | Granules screening machine | 1set |
20 | Cyclone | 1set |
21 | ID Fan | 1set |
22 | Belt Conveyor | 1set |
23 | Belt Conveyor | 1set |
24 | Belt Conveyor | 1set |
25 | Granule packaging machine | 1set |
26 | Dust collect pipes | 1set |
27 | Control cabinet | 1set |
28 | Amount | 27sets |
29 | Shipping costs | 3pcs |
30 | Total amount | 27sets |
What equipment is needed to develop a 3-5 ton cow dung organic fertilizer production line?
Below, we will list a standard 3-5t/h organic fertilizer production line equipment list for you. If your raw materials are Sugarcane Bagasse / Cow Dung / Sheep And Goat Dropping/ Chicken Dropping/ Slaughterhouse Sludge And Saw Dust etc., you can refer to this production line configuration:
No. | Item | Qty |
1 | Crawler Turner | 1set |
2 | Loading hopper | 1set |
3 | Vertical crusher | 1set |
4 | Powder screening machine | 1set |
5 | Fertilizer granulator | 1set |
6 | Granule polishing machine | 1set |
7 | Rotary Dryer | 1set |
8 | Hot air Stove | 1set |
9 | Cyclone for dryer | 1set |
10 | ID fan | 1set |
11 | Rotary cooler | 1set |
12 | Cyclone for cooler | 1set |
13 | ID fan for cooler | 1set |
14 | Granules screening machine | 1set |
15 | Granule packaging machine | 1set |
16 | Belt Conveyor*5m | 2set |
17 | Belt Conveyor*6m | 3set |
18 | Belt Conveyor*7m | 1set |
19 | Belt Conveyor*9m | 1set |
20 | Belt Conveyor*10m | 1set |
21 | Belt Conveyor*16m | 1set |
22 | Large inclination belt conveyor*5m | 1set |
23 | Large inclination belt conveyor*6m | 1set |
24 | Large inclination belt conveyor*7m | 1set |
25 | Dust Pipeline and chimney | 1set |
26 | Control cabinet | 1set |
27 | Total Amount | 29set |
28 | Shipping costs | 5pcs |
29 | Total amount | 29sets |
When processing organic fertilizers using different raw materials, are there big differences in processing technology ?
Yes, there are significant differences in processing technology and equipment when producing organic fertilizers using different raw materials. The choice of raw materials affects the entire production process, from pretreatment to final product formulation. Below is a detailed explanation of how different raw materials influence processing technology and equipment:
1. Raw Materials and Their Characteristics
Different raw materials have unique properties that impact the processing methods and equipment required:
Raw Material | Characteristics | Processing Challenges |
---|---|---|
Animal Manure | High moisture, high nitrogen content, may contain pathogens. | Requires dewatering, composting to kill pathogens, and odor control. |
Crop Residues | Dry, high carbon content, low nitrogen content. | Needs shredding, mixing with nitrogen-rich materials, and longer composting time. |
Food Waste | High moisture, high organic content, may contain oils and salts. | Requires dewatering, removal of contaminants, and careful composting to avoid odors. |
Sewage Sludge | High moisture, may contain heavy metals and pathogens. | Requires dewatering, sterilization, and heavy metal removal. |
Industrial Byproducts | Variable composition (e.g., brewery waste, sugarcane bagasse). | Needs pretreatment to standardize composition and ensure stability. |
2. Differences in organic fertilizer Productioon Technology
The organic fertilizer production plant technology varies depending on the raw material:
A. Pretreatment
- Animal Manure:
- Dewatering to reduce moisture.
- Composting to eliminate pathogens and stabilize nutrients.
- Crop Residues:
- Shredding or grinding to reduce size.
- Mixing with nitrogen-rich materials (e.g., manure) to balance carbon-to-nitrogen (C/N) ratio.
- Food Waste:
- Removal of non-organic contaminants (e.g., plastics, metals).
- Dewatering and mixing with bulking agents (e.g., sawdust, straw).
- Sewage Sludge:
- Dewatering and sterilization (e.g., thermal treatment, lime stabilization).
- Heavy metal removal (if necessary).
- Industrial Byproducts:
- Shredding, grinding, or drying to standardize the material.
B. Composting
- Animal Manure:
- Aerobic composting with regular turning to ensure proper aeration and pathogen reduction.
- Crop Residues:
- Longer composting time due to high carbon content.
- Addition of nitrogen sources (e.g., urea, manure) to accelerate decomposition.
- Food Waste:
- Requires careful monitoring to prevent odors and pests.
- May use enclosed composting systems (e.g., in-vessel composting).
- Sewage Sludge:
- Composting with bulking agents to improve aeration and reduce moisture.
- Industrial Byproducts:
- Composting time and method depend on the specific material (e.g., sugarcane bagasse decomposes faster than wood chips).
C. Post-Processing
- All Materials:
- Screening to remove oversized particles.
- Crushing and grinding to achieve uniform particle size.
- Granulation (optional) to produce pellets for easier application.
- Drying and cooling to reduce moisture and stabilize the product.
When processing organic fertilizers using different raw materials, are there big differences in equipment ?
The choice of organic fertilizer production plant equipment depends on the raw material and processing requirements:
Processing Step | Animal Manure | Crop Residues | Food Waste | Sewage Sludge | Industrial Byproducts |
---|---|---|---|---|---|
Pretreatment | Dewatering machine, mixer. | Shredder, grinder. | Contaminant separator, mixer. | Dewatering machine, sterilizer. | Shredder, dryer. |
Composting | Compost turner, windrow system. | Compost turner, mixer. | In-vessel composter. | Compost turner, bulking agent mixer. | Compost turner, mixer. |
Post-Processing | Screener, crusher, granulator. | Screener, crusher, granulator. | Screener, crusher, granulator. | Screener, crusher, granulator. | Screener, crusher, granulator. |
Odor Control | Biofilter, chemical scrubber. | Not typically required. | Biofilter, enclosed system. | Biofilter, chemical scrubber. | Not typically required. |
how to make organic fertilizer from kitchen waste?
The kitchen waste organic fertilizer production plant is a systematic production process of converting kitchen waste into organic fertilizer, involving multiple process links. The following is the detailed production process of the kitchen waste fertilizer production plant:
- Kitchen waste pretreatment
Collection and transportation: Collect kitchen waste from homes, restaurants, canteens and other places, and transport it to the treatment plant.
Sorting and crushing: Remove non-organic impurities such as plastic, metal, glass, etc. through manual or mechanical sorting. Use a crusher to break the kitchen waste into small pieces (usually less than 5 cm) for subsequent processing.
- Dehydration treatment
Reduce the water content of kitchen waste to facilitate subsequent fermentation. Reduce the water content of kitchen waste from 80%-90% to 60%-70%.
- Fermentation treatment
Fermentation is the core link of converting kitchen waste into organic fertilizer, which is divided into aerobic fermentation and anaerobic fermentation.
(1) Aerobic fermentation process:
Mix the dehydrated kitchen waste with conditioners (such as straw, sawdust, and bacterial agents) and adjust the carbon-nitrogen ratio (C/N) to 25:1-30:1. Pile the mixture in a fermentation tank or fermentation pool and turn the pile regularly to provide oxygen. The fermentation temperature is controlled at 50-70°C and lasts for 15-30 days.
(2) Anaerobic fermentation process:
Put the kitchen waste in an anaerobic fermentation tank and add anaerobic bacterial agents. Fermentation under anaerobic conditions produces biogas and organic fertilizer. The fermentation cycle is 30-60 days.
- Screening:
Use a screening machine to screen the fermented material to remove large pieces of material that have not been completely decomposed.
- Crushing:
Use a organic fertilizer crusher to further crush the screened material to ensure uniform particles.
- Blending:
Add functional bacterial agents or nutrients (such as phosphorus and potassium) as needed to improve fertilizer efficiency.
- Granulation:
Use an organic fertilizer granulator to make the material into granules for easy storage and application.
- Drying and cooling:
Use an organic fertilizer dryer to reduce the moisture content of the granules (usually less than 20%) and cool them down through a cooler.
- Packaging and storage
- Packaging: Use an automatic packaging machine to pack the organic fertilizer into bags, usually 10-50 kg/bag.
- Storage: Store the finished product in a dry, ventilated warehouse to avoid moisture.
- Environmental protection treatment
(1) Waste gas treatment:
The odor generated during the fermentation process is treated by a biological filter or a chemical scrubber.
(2) Wastewater treatment:
The wastewater generated during the dehydration process is discharged in compliance with the standards through sedimentation, filtration, biological treatment, etc.
(3) Residue treatment:
The undecomposed residue screened out can be returned to the fermentation stage or used as fuel.
What are the composting machines available in organic fertilizer production plants?
The tillers that can be used in organic fertilizer production plants include the following:
(1)Trough type compost turner
Also known as rail type compost turner, track type compost turner or compost turner, it is an ideal choice for compost fermentation of organic waste such as livestock and poultry manure, sludge garbage, sugar factory filter mud, dregs cake and straw sawdust.
This type of equipment is widely used in organic fertilizer plants and compound fertilizer plants. It includes a walking fermentation tank, a walking track, a power supply device, a compost turning part and a trough transfer device (suitable for multi-trough operation).
Among them, the compost turning part adopts efficient roller transmission, which is divided into two types: liftable and non-liftable.
(2)Rotary compost turner
Designed for handling large-span and high-depth organic waste such as livestock and poultry manure, sludge garbage, sugar factory filter mud, dregs cake and straw sawdust. This equipment is widely used in organic fertilizer plants, compound fertilizer plants, sludge and garbage plants, gardening fields and other places to help fermentation, composting and moisture removal operations.
(3)Crawler type turning machine
The crawler type turning machine adopts a four-wheel drive design, has forward, backward and turning functions, and is operated by a single person. The equipment can easily operate on the pre-stacked long strip fertilizer machine, and the fertilizer raw materials are turned, fluffed and moved through the rotating blade under the machine. After the operation is completed, a new strip pile will be formed, which is suitable for both open fields and workshop greenhouses.
The crawler type turning machine is equipped with a roller and a knife-shaped tooth, which is particularly suitable for flat stacking fermentation. It has both turning and crushing functions. It can not only evenly turn the manure base material, sludge and other materials with bacteria, but also effectively crush the fermented board agglomeration. It is an indispensable special equipment in fertilizer making operations.
The equipment is particularly suitable for the process requirements of microbial fermentation and storage of manure fertilizer, and can effectively mix the viscous storage manure with microbial preparations and straw powder. Compared with deep tank fermentation, it is faster and suppresses harmful gases produced during the fermentation process, such as hydrogen sulfide, ammonia and indole, which is both environmentally friendly and efficient.
In addition, the crawler compost turner has balanced power, low energy consumption and high output, which reduces the production cost of bio-organic fertilizer. Its reasonable design and reliable performance make it easy to control, easy to use in the pile site, and convenient to maintain.
(4)Chain plate compost turner
The chain plate compost turner is designed for trough aerobic composting of organic solid waste such as livestock and poultry manure, sludge garbage and straw. Its walking system adopts advanced variable frequency speed regulation technology, which not only adapts to different materials, but also ensures smooth operation.
The efficient compost turning ability makes it perform well in deep tank operations, thereby significantly shortening the fermentation cycle and improving production efficiency and product quality. In addition, the machine can flexibly adjust the walking speed according to the material resistance to enhance adaptability and flexibility.
After being equipped with a transfer vehicle, multi-tank equipment can be shared, which can easily expand the production scale and improve the use value of the equipment. The price range of small-sized chain plate type soil turner is between 60,000-100,000 yuan, and the specific price depends on the manufacturer.
Organic fertilizer fermentation tank is an ideal choice for treating organic waste such as pig manure, chicken manure, cow manure, sheep manure, mushroom residue, Chinese medicine residue, crop straw, etc. Its harmless treatment process only takes 10 hours, and it occupies less space and is pollution-free (closed fermentation).
The fermentation tank can completely kill pests and eggs, and the high temperature can be adjusted to 80-100℃, which is very suitable for the needs of the majority of breeding enterprises, circular agriculture and ecological agriculture to realize the resource utilization of waste.
The price range of the soil turner is between 20,000-300,000 US dollars, and the specific price depends on the manufacturer.
ABOUT RICHI MACHINERY
RICHI MACHINERY has been an industry leader in the turnkey fertilizer processing equipment market for over two decades. Our expert product and engineering team offers quality mechanical and design services for all of our turnkey solutions. From single fertilizer making machine to full fertilizer production line installation, we deliver the quality and consistency that the world’s most advanced fertilizer industries demand.
- Expert fertilizer plant solutions backed by our ISO quality control system.
- Precision fertilizer equipment and fertilizer production plant installation capabilities.
- Turnkey fertilizer plant machinery manufacturing.
- Premium fertilizer equipment and fertilizer production line customization options including customization of different parts, combination of different equipment, durable paint, primer and powder coating options.

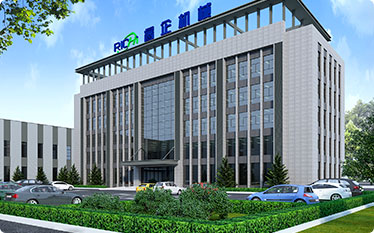
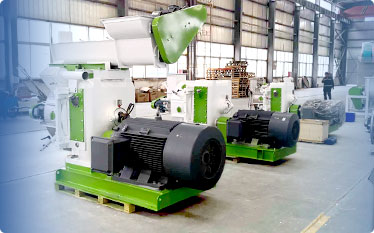
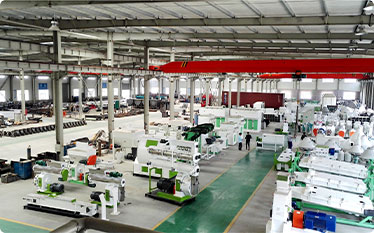
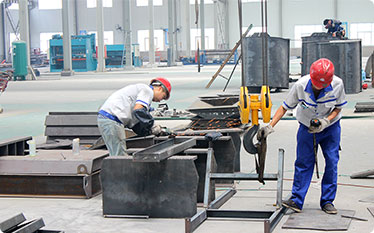